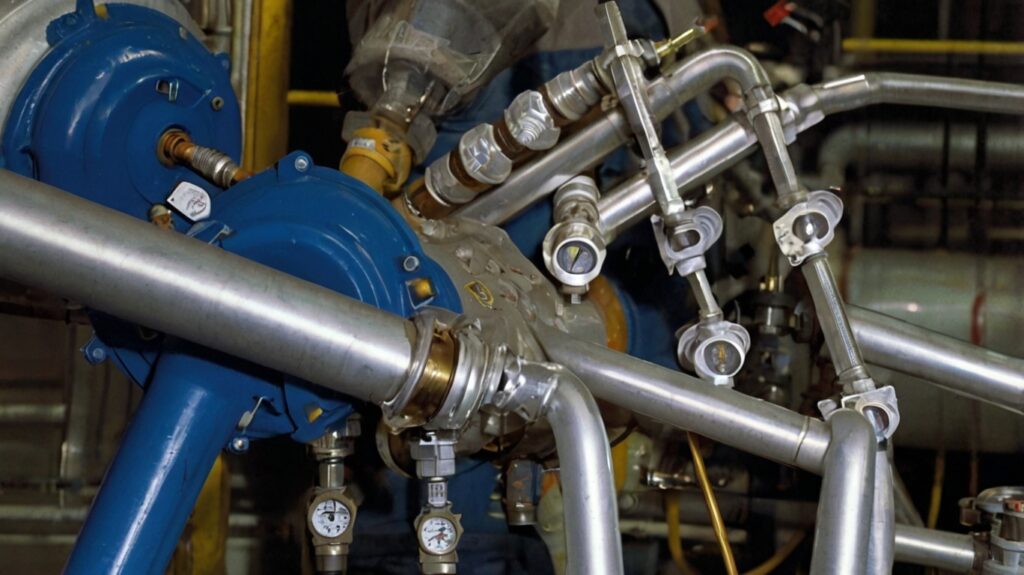
- Equipment operated by pressurized fluids, including hydraulic and pneumatic systems, is essential for versatility and precise control in various industrial applications, ensuring safety and efficiency.
- Both hydraulic systems (using liquids) and pneumatic systems (using gases) offer unique advantages, with hydraulics favored for high power applications and pneumatics preferred for rapid, less forceful tasks.
- Despite their benefits, pressurized fluid systems face challenges like maintenance demands, environmental impact on performance, and inherent safety risks, highlighting the need for certified, intrinsically safe solutions in hazardous settings.
Equipment Operated by Pressurized Fluids: Types and Uses
In the industrious world of today, where safety and efficiency are paramount, understanding the equipment and technology that keep operations running smoothly is essential. Among the myriad of tools and machinery employed across industries, equipment operated by pressurized fluids, such as water or oil, stands out for its versatility and wide-ranging applications. These systems, known as hydraulic and pneumatic devices, leverage the power of fluids under pressure to perform work, offering precise control and significant force within compact and durable designs.
At the Intrinsically Safe Store, our commitment to enhancing workplace safety across hazardous environments drives us to explore and provide technology that not only meets but exceeds global safety standards. For industries like oil and gas, mining, and pharmaceuticals, where the margin for error is minimal, understanding the types and uses of equipment operated by pressurized fluids is not just a matter of efficiency; it’s a critical component of maintaining the highest safety protocols.
This article aims to dive deep into the realm of pressurized fluid-operated equipment, shedding light on their types, uses, and the integral role they play in ensuring safe and effective operations in hazardous environments. From the basic principles that govern their operation to the advanced applications that make them indispensable, we cover the essential information you need to stay informed and safe. Whether you’re an industry veteran or new to the field of safety equipment, join us as we navigate the expansive world of hydraulic and pneumatic systems.
Introduction to Pressurized Fluid Equipment
The use of equipment operated by pressurized fluid, encompassing both water and oil, plays a crucial role in various industrial applications. This technology harnesses the power of liquids under high pressure to perform mechanical work, which is indispensable in environments that demand high reliability and efficiency. Pressurized fluid equipment spans a broad range of machinery, from hydraulic systems that power construction equipment to pneumatics used in automation and manufacturing processes.
Understanding the nuances of how these tools operate sheds light on their indispensability across sectors. At the core of pressurized fluid equipment is the principle of fluid dynamics. In its essence, fluid (either oil or water) is pressurized in an enclosed system; this pressurized fluid then transmits energy to an operating component of the equipment, causing it to move or change its mechanical state. The choice between water and oil as the pressurizing fluid heavily depends on the application, with water being favored for its non-compressibility in high-power applications, and oil preferred for its lubricating properties and wider temperature operating range.
One common example of pressurized fluid equipment is the hydraulic press, used extensively in manufacturing for molding, forging, and lifting. Similarly, hydraulic excavators in construction sites leverage pressurized oil to enable smooth and powerful movements of the arm and bucket, showcasing the heavy-duty capabilities of this technology. On the other hand, pneumatic systems, which typically use air as the pressurizing fluid, find their utility in various tools and automation systems, offering lighter, cleaner, and simpler solutions where explosive power or heavy lifting isn’t a primary requirement.
In hazardous environments, the safety, reliability, and efficiency of equipment are paramount. This is where the Intrinsically Safe Store’s mission aligns, offering products that meet stringent safety standards required in high-risk sectors like oil and gas, mining, and pharmaceuticals. Pressurized fluid equipment in such settings must not only perform under extreme conditions but also comply with safety regulations to protect personnel and property.
By integrating advanced safety features and ensuring compliance with international safety standards, the equipment we offer at the Intrinsically Safe Store is designed to mitigate risks in hazardous environments. This commitment to safety, combined with the operational advantages of pressurized fluid equipment, underscores the importance of selecting the right tools for challenging industrial tasks. As we delve deeper into the types and uses of these critical pieces of equipment, it becomes clear why they are foundational to the industries we serve.
Ready to Enhance Your Safety Protocols?
Navigating safety in hazardous environments requires not just knowledge but the right equipment. At the Intrinsically Safe Store, we provide comprehensive, certified, and intrinsically safe solutions designed to mitigate risks and protect lives. Whether your industry is in oil and gas, mining, pharmaceuticals, or any other sector where the margin for error is zero, we have the products and expertise to secure your operations.
Take proactive steps today to safeguard your work environment:
- Explore Our Catalog: Dive into our extensive collection of devices, from communication tools to lighting and monitoring systems, all crafted to meet the highest international safety standards.
- Get Expert Guidance: Unsure about what equipment best suits your needs? Our team of experts is here to help, offering personalized advice to match your industry’s specific challenges.
- Connect With Safety: Every minute matters in achieving a safer work environment. Join the thousands of clients who trust us to deliver safety solutions that make a difference.
Don’t leave safety to chance. Discover how our certified products can make your workplace safer.
- Contact Us to unlock a world of certified safe solutions.
- Browse Products that can transform your approach to safety in hazardous environments.
At the Intrinsically Safe Store, every product is a step towards a safer, more secure tomorrow. Join us in our mission to protect lives, one certified solution at a time.
Understanding the Mechanics of Hydraulics and Pneumatics
In the realms of industrial and safety equipment, identifying what type of equipment is operated by pressurized fluid, such as water or oil, unfolds the vast world of hydraulics and pneumatics. These systems are fundamental to operating a myriad of devices in hazardous environments, environments where the Intrinsically Safe Store provides indispensable safety solutions.
Hydraulics, at its core, relies on the pressurization of liquids, typically oil, to generate power or motion. This mechanism is harnessed in equipment where strong, precise movements are required. The principle of hydraulics is based on Pascal’s law, stating that when pressure is applied to a confined fluid, the pressure change occurs throughout the entire fluid. Such a principle allows hydraulic systems to amplify force, making them ideal for heavy-duty applications in industries such as construction, mining, and manufacturing. Hydraulic pumps, cylinders, motors, and valves constitute the essential components of these systems, enabling the control and transmission of hydraulic power.
Pneumatics, on the other hand, operates on a similar premise but utilizes compressed air or other gases instead of liquids. Pneumatic systems are prized for their quick, clean, and efficient movement with applications ranging from factory automation to the operation of pneumatic tools such as drills and hammers. The advantage of pneumatics lies in its simplicity, safety, and reliability—attributes critically important in hazardous environments. The basic components of pneumatic systems, including compressors, actuators, valves, and fittings, collaborate to convert pressurized gas into mechanical work.
Both hydraulic and pneumatic systems offer unique advantages for operating equipment in challenging conditions. Hydraulics is favoured for its high power density and precision control, making it suitable for equipment demanding substantial force and meticulous manipulation. Pneumatics, characterized by its rapid movement and inherent explosion safety due to using air, is frequently selected for applications requiring speed and a high cycling rate, as well as environments where fire hazards must be strictly managed.
By integrating these systems into equipment, the Intrinsically Safe Store ensures that industries operating in hazardous conditions are equipped with tools that are not only powerful and precise but also intrinsically safe. Understanding the mechanics behind hydraulics and pneumatics is crucial for selecting the appropriate equipment that meets the rigorous demands of safety and efficiency.
Types of Hydraulic Equipment and Their Applications
Hydraulic systems utilize pressurized fluid, such as oil or water, to transmit power in various machinery and equipment. This feature is especially critical in hazardous environments where safety cannot be compromised. Understanding the types of hydraulic equipment and their applications can help industries select the appropriate devices to ensure operational safety and efficiency.
Hydraulic Pumps
Applications: Mining, Manufacturing, Construction
Hydraulic pumps are the heart of hydraulic systems, converting mechanical energy into hydraulic energy by moving the pressurized fluid into the hydraulic circuit. This is essential for the operation of hydraulic machinery in industries like mining, manufacturing, and construction, where they power a range of machinery from excavators to conveyor belts.
Hydraulic Cylinders
Applications: Material Handling, Aerospace, Agriculture
Hydraulic cylinders deliver unidirectional force through unidirectional stroke, making them vital in material handling equipment, agricultural machinery, and aerospace applications. These devices enable heavy lifting, precise movement, and can withstand harsh, potentially explosive environments when properly certified.
Hydraulic Valves
Applications: Oil and Gas, Pharmaceutical, Chemical Processing
In controlling the flow and pressure of the hydraulic fluid, valves play a crucial role in managing the operation of hydraulic systems. Their precision and reliability are paramount in sectors like oil and gas, pharmaceuticals, and chemical processing, where controlling fluid dynamics under high pressure is necessary for safety and efficiency.
Hydraulic Accumulators
Applications: Energy Storage, Shock Absorption, Emergency Operations
Hydraulic accumulators store pressurized hydraulic fluids, releasing them when needed to absorb shock or provide additional power. This function is critical for energy storage, emergency operations, and counterbalancing shocks and vibrations in heavy machinery, ensuring equipment longevity and personnel safety in hazardous environments.
Hydraulic Motors
Applications: Marine, Industrial Drives, Renewable Energy
Converting hydraulic energy back into mechanical form, hydraulic motors are key in applications requiring substantial rotational force, such as industrial drives, marine applications, and even renewable energy projects. Their robust design allows operation in challenging environmental conditions, aligning with the need for intrinsically safe solutions in such settings.
For organizations operating in hazardous environments, selecting the right type of hydraulic equipment is more than an operational decision—it’s a safety imperative. At the Intrinsically Safe Store, our expertise and catalog of certified safe products ensure that safety is never compromised, aligning with the most stringent international standards and our commitment to making industries safer, one certified solution at a time.
Advantages of Using Pressurized Fluid Systems
The utilization of pressurized fluid systems in equipment offers numerous advantages, especially in environments that demand the utmost safety and reliability. These systems, which can be powered by water, oil, or other fluids under high pressure, are pivotal in various industrial applications. Here’s a closer look at the key benefits of using pressurized fluid systems in equipment, aligning with the stringent safety requirements that organizations like the Intrinsically Safe Store advocate for.
Enhanced Safety
Pressurized fluid systems are inherently safer compared to their electrical counterparts, especially in hazardous environments prone to fires or explosions. Since these systems operate without sparking or generating high heat levels, they significantly reduce the risk of igniting flammable substances, thus ensuring the safety of operations in industries such as oil and gas, mining, and pharmaceuticals. This intrinsic safety feature aligns perfectly with our mission to provide solutions that protect lives in such environments.
High Power Density
One of the most compelling advantages of using pressurized fluid systems is their high power density. These systems can transmit a substantial amount of power using relatively small and compact components. This efficiency is crucial in heavy machinery and equipment, where space might be at a premium and the need for powerful yet compact solutions is paramount.
Reliability and Durability
Equipment powered by pressurized fluids exhibits high levels of reliability and durability, even under the strenuous conditions found in hazardous environments. Pressurized fluid systems have fewer moving parts compared to mechanical systems, which reduces the likelihood of failure and extends the equipment’s operational life. This durability is essential for ensuring the continuous, safe functioning of critical equipment, minimizing downtime, and reducing maintenance costs over time.
Precision Control
Another notable benefit of pressurized fluid systems is the precision control they offer. Whether it’s the gentle movement of a robot arm in a manufacturing plant or the robust operation of a hydraulic jack in a construction site, pressurized fluids allow for smooth, precise control over the equipment’s movements. This level of control is invaluable in many industrial applications, where precision is essential for quality, safety, and efficiency.
Environmental Resistance
Equipment that operates on pressurized fluid systems boasts superior resistance to harsh environmental conditions, including dust, moisture, and extreme temperatures. This resilience makes such equipment ideal for demanding environments, ensuring that critical operations can continue unimpeded, regardless of external conditions. Our catalog at the Intrinsically Safe Store features devices designed to withstand these tough conditions, embodying our dedication to offering reliable, safe, and efficient solutions.
In summary, pressurized fluid systems in equipment present unmatched advantages that are crucial for the safe and efficient operation of machinery in hazardous environments. These systems embody the principles of safety, reliability, and performance that are central to our offerings at the Intrinsically Safe Store. As we navigate the complexities of hazardous industries, the importance of utilizing equipment that leverages the benefits of pressurized fluids cannot be overstated.
Pneumatics vs. Hydraulics: Comparing Performance and Use
Understanding the differences between pneumatics and hydraulics is critical in identifying which type of pressurized fluid equipment is suitable for a specific application, especially in hazardous environments. Both systems use fluid to transmit power, but the type of fluid—air or gas in pneumatics and liquid (such as oil or water) in hydraulics—fundamentally alters their performance, applications, and suitability for use in various settings.
Pneumatics:
Pneumatic systems operate using compressed air or gas. These systems are known for their fast-moving capabilities, making them an ideal choice for applications requiring rapid movement and lighter forces. Pneumatics are frequently used in factory automation, where they power devices such as air brakes, pneumatic actuators, and various tools used in assembly lines. The primary advantages of pneumatics include simplicity, clean operation due to air being the fluid, and quick response times.
However, pneumatics generally have less force than hydraulics, making them unsuitable for applications requiring heavy lifting or high force applications. Also, because air can compress, pneumatic systems can be slightly less consistent in terms of force application, which is a critical consideration in precision operations.
Hydraulics:
Hydraulic systems, on the other hand, use pressurized liquid to perform work. The incompressible nature of liquids allows hydraulic systems to exert tremendous force, far exceeding the capabilities of pneumatics. This high-force output makes hydraulics the go-to choice for heavy machinery and equipment, such as construction machinery, elevators, and hydraulic jacks in hazardous environments. Hydraulics are highly valued for their power and precision, as well as their ability to maintain constant force and speed.
Despite their strength, hydraulic systems have drawbacks, including potential for fluid leaks, which can be a significant safety concern, particularly in environments that are sensitive to contamination or fire hazards. Additionally, hydraulic equipment usually requires more maintenance than pneumatic counterparts and can be more complex to operate and repair.
Performance and Use in Hazardous Environments:
When selecting equipment for hazardous environments, safety is paramount. Pneumatic systems are often preferred in environments where there’s a risk of fire or explosion, as they are less likely to generate heat and use air, which is less likely to cause contamination compared to hydraulic oil. In contrast, hydraulic systems offer unmatched power and precision, making them indispensable in environments where heavy lifting and precision are required, provided that measures are taken to mitigate leak and contamination risks.
Intrinsically safe devices and equipment, whether operated by pneumatics or hydraulics, must adhere to rigorous safety standards to ensure they do not become a source of ignition in hazardous environments. At the Intrinsically Safe Store, understanding these differences helps us recommend the most appropriate, certified safe products for our clients’ specific needs, whether they’re involved in the oil and gas, mining, or pharmaceutical industries. Our aim is to ensure that the equipment not only meets the functional requirements of the task at hand but also upholds the highest safety standards to protect lives in hazardous conditions.
Challenges and Limitations of Pressurized Fluid Equipment
Pressurized fluid equipment, despite its extensive applications and advantages, encounters several challenges and limitations that organizations and individuals in hazardous environments need to consider. Understanding these hurdles is crucial for ensuring the safety and efficiency of operations, especially in sectors like oil and gas, mining, and pharmaceuticals, where safety cannot be compromised.
Maintenance and Inspection Requirements
One significant challenge of using equipment operated by pressurized fluids, such as water or oil, is the maintenance and inspection requirements. These systems necessitate regular checks to prevent leaks, corrosion, and wear and tear that could lead to equipment failure or hazardous situations. In environments where safety is paramount, ensuring that these checks are conducted meticulously and systematically becomes even more critical.
Environmental and Operational Conditions
The performance of pressurized fluid equipment can be heavily influenced by environmental and operational conditions. Extreme temperatures, for example, can affect the viscosity of the operating fluid, thereby impacting the efficiency and safety of the equipment. Similarly, the presence of dust, debris, or corrosive materials in the operating environment can lead to premature failure of components. These conditions require specialized solutions that can withstand such challenges without compromising functionality.
Complexity and Cost
The complexity of pressurized fluid systems presents another challenge. Designing, installing, and operating these systems requires a high level of expertise and knowledge, making it essential for organizations to have access to skilled professionals. Furthermore, the cost associated with the installation, maintenance, and potential downtime due to equipment failure can be significant. It is crucial for organizations to weigh these costs against the benefits pressurized fluid equipment brings to their operations.
Safety Risks
Lastly, the inherent safety risks associated with pressurized fluid systems cannot be overlooked. The possibility of leaks, bursts, or failures poses a significant threat in hazardous environments. This underscores the importance of utilizing certified safe products and systems that meet international safety standards. At the Intrinsically Safe Store, our focus on providing products that ensure the highest levels of safety is driven by the understanding of these risks. Our selection of intrinsically safe devices is designed to mitigate the challenges posed by pressurized fluid equipment, ensuring that organizations can maintain safety while benefiting from the capabilities of these systems.
In conclusion, while pressurized fluid equipment plays a crucial role in various industrial applications, addressing the challenges and limitations is essential for maximizing their benefits and maintaining safety in hazardous environments.
Conclusion
In the realm of hazardous environments, understanding and utilizing equipment operated by pressurized fluids such as water or oil is critical to maintaining operational safety and efficiency. From hydraulic systems powering heavy machinery in the oil and gas industry to the water-based suppression systems safeguarding the pharmaceutical sector, this technology is at the heart of a myriad of safety-critical applications. At the Intrinsically Safe Store, our commitment is to ensure that every organization operating in these high-risk areas is equipped with not just the right tools but with the assurance that their equipment meets the highest standards of safety and reliability. By offering a comprehensive selection of certified intrinsically safe products, we not only bolster the safety of these workplaces but also contribute toward a safer, more secure future in hazardous industries. Remember, whether it’s through the precision of hydraulic machinery or the reliability of fluid-based monitoring devices, pressurized fluid equipment plays a pivotal role in safeguarding both lives and assets. Let’s collaborate to make every environment where such technology is utilized, a safer place for everyone involved.
FAQs: Understanding Equipment Operated by Pressurized Fluids
What are some common types of equipment that use hydraulic systems?
Hydraulic systems leverage pressurized fluid to power various types of equipment across many industries. Common examples include hydraulic presses, which are used for forging, molding, and punching materials. Excavators and backhoes, which are staples in construction, depend on hydraulic systems for their digging and lifting capabilities. Other examples include aircraft controls, where hydraulic systems are employed to operate flaps and landing gear, and in manufacturing, where they power assembly line machinery.
What industries frequently use pneumatically operated equipment?
Pneumatically operated equipment, which utilizes compressed air or gas, finds widespread use in numerous sectors. The manufacturing industry employs pneumatic tools for assembly operations due to their reliability and ease of maintenance. The automotive sector uses pneumatics in painting and welding robots. Additionally, the pharmaceutical industry utilizes pneumatic systems to handle delicate products and in cleanroom operations where hygiene and cleanliness are paramount. The construction and mining industries also benefit from the robustness of pneumatic tools in their high-demand environments.
How do you maintain hydraulic equipment to ensure safe operation?
Maintaining hydraulic equipment is crucial for ensuring its safe operation, especially in hazardous environments. Regular maintenance routines should include checking for leaks in the hydraulic fluid, which could lead to loss of pressure and contamination of the workplace. Monitoring the hydraulic fluid’s level and quality is essential, as contaminants can degrade system performance and safety. Replacing worn hoses and fittings before they fail can prevent dangerous fluid ejections. Lastly, adherence to a regular maintenance schedule and immediate repairs of any malfunctions are vital practices for sustaining the hydraulic system’s integrity.
What is the role of a compressor in equipment that operates with pressurized fluids?
A compressor plays a critical role in equipment that operates with pressurized fluids by converting the power from an external source (like an electric motor or gasoline engine) into stored energy in the form of compressed air or pressurized fluid. This pressurized fluid can then be released to power various tools and machinery. In pneumatic systems, compressors provide the air flow necessary for tool operation. In hydraulic systems, though the principle is slightly different, the function of generating pressure is comparable.
How are pressurized fluids controlled in equipment operation?
In equipment operation, controlling pressurized fluids is managed through a combination of valves, pumps, and actuators. Valves regulate the flow and direction of the fluid, ensuring it moves in the correct path and at the right pressure. Pumps generate the necessary pressure within the system, driving the fluid to where it is needed. Actuators, which can be hydraulic cylinders or pneumatic pistons, convert the fluid pressure into mechanical force, allowing for movement and control of the equipment. Sophisticated control systems, often computerized, can coordinate these components for precise and efficient operation.