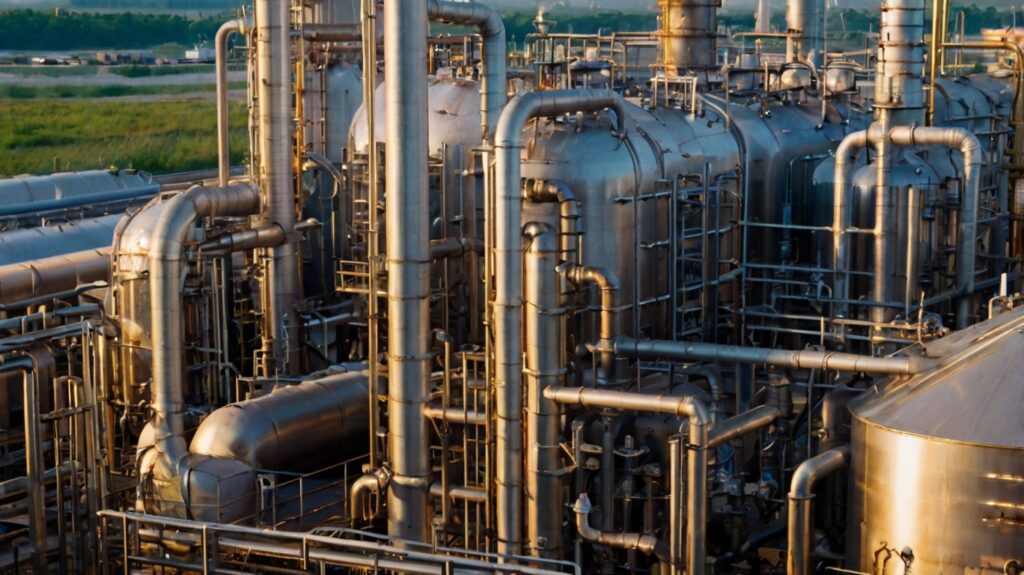
Definition: A chemical plant is a facility where chemical processes are carried out on an industrial scale to produce a variety of chemical products. These plants involve the reproduction of chemical reactions, similar to those in laboratory settings but on a much larger scale, using equipment such as retorts, test tubes, and mixtures.
Key Operations: Chemical plants are operated by skilled personnel, including chemical plant operators, who are responsible for the safe and efficient operation of the plant equipment. This includes monitoring chemical reactions, operating and maintaining equipment, transporting chemical materials, and ensuring strict adherence to safety protocols to prevent emergencies and maintain a stable process environment.
Equipment and Safety: The operation of a chemical plant involves the use of sophisticated equipment such as flowmeters, panel lights, and other indicators to monitor the production process. Operators must also inspect equipment and tanks regularly to ensure they are in good working condition and take immediate action in case of emergencies, such as shutting down the system under the direction of supervisors.
Impact of Technology: Advances in technology have significantly impacted the operation of chemical plants. Modern plants often rely on computer-operated machines, which have increased efficiency but also led to a reduction in the number of jobs for chemical plant operators. This shift towards automation is part of the broader trend in the industry to reduce costs and become more environmentally friendly.
Examples in Action: Chemical plants are essential in various industries, including the production of chemicals for manufacturing, pharmaceuticals, and agricultural products. For instance, petrochemical plants produce chemicals derived from petroleum, while other plants may specialize in the production of specialty chemicals used in various consumer products.
Fun Fact: The evolution of chemical plant operations has led to a more intellectual and less physically demanding work environment for operators. Today, many operators work from control rooms, managing large facilities through complex systems, highlighting the transformation from manual labor to more technologically driven processes.
Key Takeaways:
- Understanding and integrating core chemical processes, such as reactions and distillation, are essential for maintaining safe and efficient operations within chemical plants.
- Safety protocols, including engineering, administrative controls, and PPE, are vital to protect workers and mitigate risks associated with volatile chemicals.
- Lessons learned from past chemical plant disasters underscore the importance of stringent safety measures and continuous improvement to prevent future incidents.
Introduction to Chemical Plant Operations
A chemical plant is a meticulous and complex facility designed for the production and processing of chemicals on a large scale. These plants play a pivotal role in the global economy, transforming raw materials into valuable products used across a myriad of industries, including pharmaceuticals, oil and gas, and consumer goods, among others. Understanding the operations within a chemical plant is crucial for those involved in ensuring the safety and efficiency of these processes.
Core Processes
At the heart of a chemical plant’s operation are its core processes, which include chemical reactions, separation, and purification methods. These processes are designed to be carried out in a controlled and safe manner, using reactors, distillation columns, and filters to convert and refine raw materials. The ultimate goal is to produce high-quality end products that meet stringent industry standards and customer expectations.
Safety and Efficiency
Safety is paramount in a chemical plant. Given the potential hazards associated with handling chemicals, rigorous safety protocols and systems are in place to protect workers and the environment. This includes the use of explosion-proof and intrinsically safe equipment to prevent accidents, continuous monitoring of operational parameters, and adherence to strict regulatory standards.
Efficiency is another critical aspect of chemical plant operations. With the adoption of automation technologies and process optimization strategies, plants strive to maximize output while minimizing waste and energy consumption. This not only contributes to the plant’s economic performance but also supports environmental sustainability.
Support and Customer Satisfaction
For professionals working within these hazardous environments and are responsible for procurement, engineering, and safety management, the importance of reliable support and quality equipment cannot be overstated. The Intrinsically Safe Store stands as a trusted partner in this regard, offering a comprehensive selection of intrinsically safe and hazardous area products tailored for the chemical industry. Our commitment to operational excellence and customer satisfaction ensures that you receive the expert support you need for inquiries and purchases, aligning with our mission to facilitate a safer, more efficient chemical plant operation.
Understanding the fundamentals and the operational intricacies of a chemical plant is essential for those tasked with maintaining its safety and efficiency. By integrating state-of-the-art safety equipment and adhering to operational best practices, chemical plants can achieve the high standards required in today’s competitive and regulatory landscape.
Ensure Your Chemical Plant’s Safety and Efficiency with Our Expert Solutions
In the demanding and potentially hazardous world of chemical plant operations, ensuring safety and efficiency is not just an objective—it’s a necessity. The Intrinsically Safe Store stands at the forefront of providing tailored safety solutions that meet the intricate requirements of the chemical, oil & gas, and pharmaceutical industries, among others. Our commitment to operational excellence and customer satisfaction drives us to offer an unparalleled selection of safety products and services designed for high-risk environments. Take the proactive step towards enhancing your facility’s safety protocols by considering our offerings:
- Explore Our Wide Range of Intrinsically Safe and Explosion-Proof Equipment: From specialized cases for iPhones, iPads, and Android devices to comprehensive hazardous area products including lighting and handheld scanners, we have everything your chemical plant needs to maintain safety and compliance.
- Benefit from Our Industry Expertise: Our team is not just about selling products; we aim to be a partner in your safety journey. With expert support available for any inquiries or past purchases, we’re here to assist you in selecting the perfect equipment tailored to your specific industry requirements.
- Achieve Operational Excellence: Embrace the principles of operational excellence with safety solutions that promote an open, organized, and clearly communicated work environment. Our commitment to anti-bureaucratic and anti-toxic practices ensures that we focus on what truly matters—your safety and satisfaction.
Don’t compromise on safety within your chemical plant. Contact us today to discover how our intrinsically safe solutions can help protect your team and enhance operational efficiency.
The Core Chemical Processes
In-depth understanding of the core chemical processes is essential for comprehending the vast ecosystem of a chemical plant. These processes are the heart of production, where raw materials undergo various transformations to become the chemicals and substances pivotal to modern life. Below, we delve into several critical processes, their roles within the chemical manufacturing chain, and how safety and efficiency are interwoven into each step, aligning with the values and expertise provided by The Intrinsically Safe Store.
Chemical Reactions
Chemical reactions are at the forefront of industrial processes in a chemical plant. These reactions involve the transformation of substances through the breaking and forming of chemical bonds. Types of reactions include polymerization, wherein smaller molecules combine to form polymers, and cracking, where larger molecules are broken down into smaller ones. Safety in these reactions is paramount, as they can release or absorb significant amounts of energy, necessitating the use of intrinsically safe and explosion-proof equipment.
Distillation
Distillation is a purification process used to separate mixtures based on differences in volatilities. In a chemical plant, it can be found in operations ranging from the refining of crude oil to the production of alcohols. Efficient distillation processes contribute significantly to the plant’s overall effectiveness, reducing energy inputs and improving yield quality. The safety measures in place, such as intrinsically safe controls, prevent the risk of explosions and ensure a safe environment for the workforce.
Extraction
Extraction processes are used to isolate specific compounds from a mixture. This could involve the separation of a product from waste materials or the removal of contaminants. Liquid-liquid extraction is frequently employed in pharmaceutical manufacturing, an area where The Intrinsically Safe Store specializes by providing safety solutions. Ensuring the use of compatible and safe equipment is crucial to prevent chemical reactions that could compromise product quality or worker safety.
Reactor Operations
Reactor operations are fundamental to the chemical industry, involving controlled conditions to facilitate chemical reactions. Types of reactors vary widely, from simple batch reactors to complex continuous flow reactors. Managing these operations efficiently requires precise control and monitoring of temperature, pressure, and chemical feeds. The adoption of intrinsically safe equipment ensures these parameters are maintained within safe limits, preventing any potential hazardous scenarios.
Safety and efficiency in these core chemical processes are not mutually exclusive; they are\ interdependent. The Intrinsically Safe Store understands the importance of both, offering products and services that ensure processes not only meet but exceed industry safety standards. Our commitment to operational excellence and customer satisfaction ensures that professionals in the field have access to expert support and the right equipment to maintain these standards, aligning with our dedication to creating safer working environments across hazardous industries.
Key Components of a Chemical Plant
A chemical plant is a complex ensemble of structures, machinery, and equipment designed for efficient and safe production processes. Understanding the fundamental components of a chemical plant is crucial for professionals involved in safety, procurement, engineering, and management in hazardous environments. Here, we identify and explain some of the key components that are vital for the operation of a chemical plant, with an emphasis on safety and efficiency.
Reactors
Reactors are at the heart of a chemical plant. They are the chambers where raw materials are transformed into desired chemical products through controlled chemical reactions. Safety is paramount in reactor design to handle extreme temperatures, pressures, and potentially hazardous chemical reactions. Intrinsically safe monitoring and control systems ensure reactors operate within safe parameters, minimizing the risk of accidents.
Distillation Columns
Distillation columns are critical for separating the components of a chemical mixture based on their boiling points. This separation process is fundamental in producing pure chemical compounds necessary for various industrial applications. The efficiency and safety of distillation columns directly impact the overall productivity and safety of a chemical plant.
Heat Exchangers
Heat exchangers are used to transfer heat between two or more fluids, crucial for precise temperature control in chemical reactions and processes. They contribute to a plant’s efficiency by conserving energy and enabling the reuse of heat, thereby reducing operational costs and the environmental footprint.
Storage Tanks
Storage tanks hold raw materials, intermediates, and finished products. These are designed with safety features to contain hazardous chemicals, prevent contamination, and control emissions. Proper labeling and monitoring are essential to ensure safe handling and storage conditions.
Piping Systems
Piping systems interconnect the various components of a chemical plant, providing pathways for raw materials, intermediates, and final products to move through the production process. The selection of materials and design of the piping system are critical to withstand the chemicals they transport and the conditions under which they operate.
Control Systems
Modern chemical plants rely on advanced control systems for efficient, safe operations. These systems monitor process variables, such as temperature, pressure, and flow rates, in real-time. Automated controls and safety interlocks help to prevent accidents by ensuring processes stay within safe operating limits.
Safety and Emergency Equipment
Safety is the cornerstone of operations in a chemical plant. Emergency equipment, including fire suppression systems, gas detectors, and spill containment solutions, are indispensable. The Intrinsically Safe Store provides industry-leading safety and emergency equipment tailored to meet the stringent requirements of chemical manufacturing and other hazardous environments. Our range of intrinsically safe and explosion-proof equipment ensures that professionals have access to the products necessary to maintain a safe work environment.
Remember, the efficiency, productivity, and safety of a chemical plant significantly depend on these key components working harmoniously together. Ensuring that each part operates efficiently and safely is crucial for the overall success of a chemical manufacturing operation.
Safety Protocols in Chemical Manufacturing
In the realm of chemical manufacturing, safety is not merely a policy but a core foundation of operational integrity. Well-established safety protocols are indispensable to ensure the well-being of workers and the surrounding environment. The nature of working with potentially hazardous substances demands rigorous adherence to safety measures to mitigate risks, prevent accidents, and maintain efficiency.
Identifying Hazardous Conditions
The first step in safeguarding any chemical plant is the accurate identification of potential hazards. This involves conducting thorough risk assessments to evaluate the properties of the chemicals used, their interactions, and possible outcomes of mishandling. Materials Safety Data Sheets (MSDS) provide vital information on handling, storage, and emergency measures, serving as a cornerstone for training personnel in hazard awareness.
Engineering Controls
Engineering controls play a pivotal role in minimizing exposure to hazardous chemicals. This includes the design and implementation of closed systems and ventilation systems to contain or dilute harmful emissions. Safety barriers, interlock systems, and explosion-proof enclosures ensure mechanical safety. Our range at The Intrinsically Safe Store includes intrinsically safe cases and explosion-proof equipment designed to provide robust protection in hazardous areas.
Administrative Controls
Effective safety management extends beyond physical measures. Administrative controls encompass the establishment of standard operating procedures (SOPs), safety training programs, and emergency response plans. Ensuring that all personnel are well-versed in these protocols is crucial. Regular safety drills and refresher training help reinforce safe practices and prepare teams for potential emergency situations.
Personal Protective Equipment (PPE)
Equipping workers with the appropriate personal protective equipment (PPE) is the last line of defense against exposure to hazardous chemicals. PPE selection varies based on the specific chemicals handled and the nature of the work performed, including respirators, gloves, chemical suits, and eye protection. We at The Intrinsically Safe Store offer a wide array of PPE designed to meet the highest standards of safety and compliance, supporting a culture of safety across all operations in hazardous environments.
In conclusion, maintaining safety in chemical manufacturing requires a multifaceted approach, integrating engineering solutions, administrative controls, personal protective gear, and continuous training. These protocols ensure not only the protection of staff and assets but also contribute to operational efficiency and productivity.
Risks and Challenges in Chemical Production
In the intricate ecosystem of chemical production, where the transformation of raw materials into invaluable outputs occurs, a myriad of risks and challenges inherently exists. Understanding these elements is crucial for professionals operating within hazardous environments, ensuring both safety and efficiency are steadfastly maintained.
One of the primary concerns lies in the volatility of the chemicals being handled. Chemical reactions, if not meticulously controlled, can lead to explosions or fires, posing significant threats to both human life and infrastructure. The complexity of these processes requires not only specialized knowledge but also the right equipment to ensure safety. At The Intrinsically Safe Store, we recognize the paramount importance of using intrinsically safe and explosion-proof equipment, which is why we offer a range of products designed to mitigate these risks.
Exposure to hazardous chemicals can also have severe health implications for workers, from acute effects such as burns or poisoning to chronic impacts like respiratory diseases or cancer. Ensuring the wellbeing of employees necessitates the adoption of comprehensive safety measures, including the use of personal protective equipment (PPE), which forms an integral part of our product offering.
Operational challenges also emerge from the need to comply with rigorous international standards and regulations aimed at safeguarding both the environment and public health. Navigating this regulatory landscape, while maintaining productivity and profitability, highlights the need for expertise and support in selecting the right safety solutions. Our commitment at The Intrinsically Safe Store extends beyond providing exceptional products; we aim to be a partner in compliance, helping our customers understand and meet these standards.
Moreover, the chemical industry is one of continuous innovation and adaptation, driven by evolving market demands, technological advancements, and sustainability goals. Staying competitive requires not only optimizing current operations but also anticipating future safety and operational needs. This adaptive approach permeates our ethos, ensuring our product range and expertise remain at the industry’s forefront, thereby supporting our customers through the challenges of today and tomorrow.
In conclusion, navigating the risks and challenges in chemical production demands a comprehensive approach to safety and efficiency. By leveraging the right expertise and equipment, companies can protect their workforce, comply with regulations, and sustainably grow. At The Intrinsically Safe Store, we are dedicated to supporting our customers in these endeavors, embodying our commitment to operational excellence and customer satisfaction.
Chemical Plant Disasters: Lessons Learned
The history of the chemical industry is not without its dark chapters. Some of the most significant lessons in safety and efficiency stem from the aftermath of chemical plant disasters. These tragic events underscore the critical importance of stringent safety protocols and a culture of continuous improvement within hazardous environments.
One stark reminder is the Bhopal Gas Tragedy of 1984, which is considered among the world’s worst industrial disasters. A gas leak at a pesticide plant in Bhopal, India, resulted in thousands of deaths and countless injuries. This disaster highlighted the catastrophic consequences of inadequate safety measures and emergency preparedness. The lessons learned from Bhopal have led to the implementation of more rigorous international safety standards and practices, such as the Process Safety Management (PSM) standard.
Another significant incident occurred in 1989, at the Phillips 66 Houston Chemical Complex in Pasadena, Texas, where a series of explosions caused numerous fatalities and injuries. The investigation into this disaster led to a greater emphasis on process safety information, hazard analysis, and the necessity for effective communication systems within chemical facilities. It also shed light on the importance of engineering controls and the need for continuous safety training for all plant personnel.
These incidents, among others, serve as somber reminders of what can go wrong when safety is not prioritized. They have propelled the industry forward, driving innovations in safety technologies and practices. Today, there is an unyielding focus on preventing such tragedies through advanced risk management, the integration of safety protocols from the design phase, and fostering a culture of safety across all levels of an organization.
The Intrinsically Safe Store underscores the significance of these lessons by offering products and services designed to prevent accidents in hazardous environments. Our range of intrinsically safe and explosion-proof equipment is essential for enhancing safety measures in chemical plants, ensuring both the protection of workers and operational efficiency. By prioritizing customer support and satisfaction, we offer more than just products; we provide peace of mind, knowing that every precaution is being taken to avoid potential disasters.
In conclusion, the chemical industry has learned many hard lessons from its past. Today, safety is not just a regulation; it’s a fundamental component of a chemical plant’s DNA. Embracing this ethos, The Intrinsically Safe Store remains committed to supporting chemical plants in their mission to operate safely and efficiently, honoring our paramount concern for the well-being of those working in hazardous conditions.
FAQs: Navigating the Complex World of Chemical Plants
What is process control in a chemical plant?
Process control in a chemical plant involves the use of technologies and methods to monitor, adjust, and optimize the manufacturing processes. It ensures that chemical reactions and processes are carried out safely, efficiently, and at the optimal rate, to produce the desired end products. Effective process control is vital for maintaining product quality, reducing waste, ensuring safety, and maximizing profitability.
How do chemical reactors work?
Chemical reactors are the heart of a chemical plant, where raw materials undergo chemical reactions to form new substances. The functioning of a reactor depends on the type of reaction and the desired outcome. In its basic form, a reactor facilitates the mixing of reactants, controls temperature and pressure, and ensures that the reaction proceeds at the intended rate. Reactors can vary greatly in design, from simple batch reactors to complex continuous or semi-continuous systems, depending on the production needs.
What is the role of a chemical engineer in a plant?
A chemical engineer plays a crucial role in a chemical plant by designing, implementing, and optimizing the processes involved in chemical manufacturing. They apply principles of chemistry, physics, mathematics, and engineering to solve problems related to production, transformation, and use of chemicals, materials, and energy. Additionally, chemical engineers are responsible for ensuring that the plant operates safely, efficiently, and in compliance with environmental and safety regulations.
What types of chemicals are produced in a chemical plant?
A chemical plant can produce a wide variety of chemicals, which can be broadly categorized into basic chemicals, specialty chemicals, and consumer chemicals. Basic chemicals, such as petrochemicals and polymers, serve as raw materials for other industries. Specialty chemicals, including dyes, pigments, and coatings, have specific applications and performance characteristics. Consumer chemicals are directly sold to the public, like cleaning agents and personal care products.
How is quality assurance maintained in a chemical plant?
Quality assurance in a chemical plant is maintained through a combination of stringent process control, regular monitoring, and testing of products at various stages of production. It involves setting clear quality standards, conducting inspections, and implementing quality management systems compliant with international standards. Detailed records of production processes and quality tests ensure traceability and accountability, allowing for continuous improvement and adherence to safety and environmental regulations.