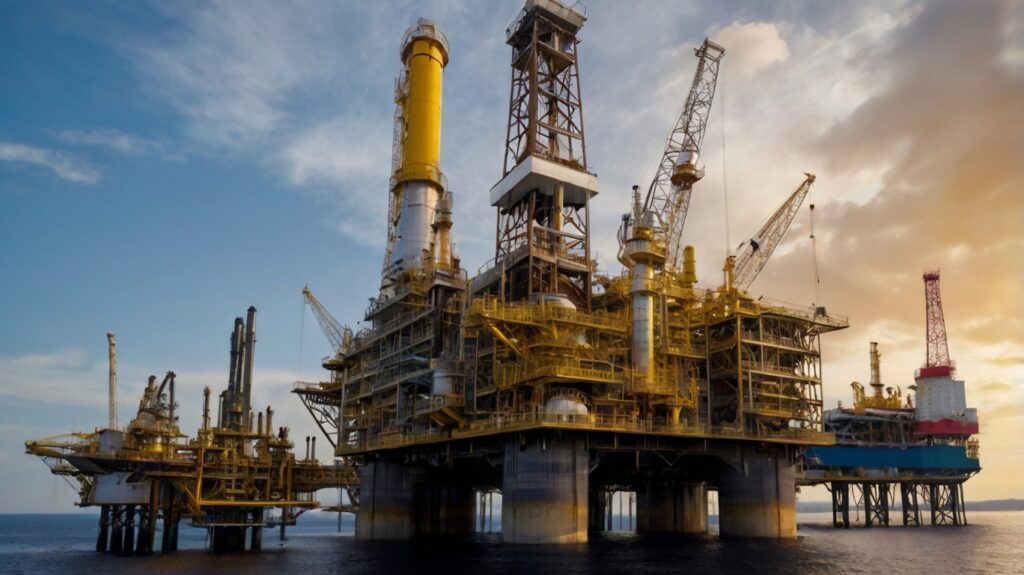
- Risk Mitigation and Compliance: ATEX-certified equipment is crucial in reducing risks and ensuring compliance with safety regulations in hazardous industries, preventing accidents and legal penalties.
- Financial and Brand Advantages: Investing in ATEX-certified equipment can lead to long-term financial savings and enhance brand reputation by demonstrating a commitment to safety and regulatory adherence.
- Understanding Hazard Categories and Zones: Proper identification of explosive atmospheres, whether gas or dust, guides the selection of ATEX-certified equipment, crucial for maintaining safety and compliance in specific industry environments.
The Importance of ATEX Certified Equipment for Hazardous Areas
When operating in hazardous environments, the importance of using ATEX-certified equipment cannot be overstated. ATEX certification is an essential endorsement for products designed to be used in explosive atmospheres. This certification ensures that the equipment, ranging from electrical fixtures to mechanical parts, has been rigorously tested and meets stringent European Union standards for safety.
Risk Mitigation: One of the paramount benefits of ATEX-certified equipment is its role in risk mitigation. Industries such as oil and gas, chemical manufacturing, and others involving explosive substances or atmospheres are inherently risky. Using ATEX-certified equipment drastically reduces the likelihood of accidents, protecting not just the workforce but also the environment from potentially catastrophic incidents.
Compliance and Safety: Beyond the practical dimension of risk reduction, ATEX certification is synonymous with compliance with safety regulations. In many jurisdictions, employing ATEX-certified equipment in applicable sectors is not just a best practice but a legal requirement. Compliance with these standards not only helps prevent financial penalties but also underscores a company’s dedication to maintaining safety as a core value.
Financial Efficiency: While the initial investment in ATEX-certified equipment may appear substantial, the long-term savings are significant. The durability and reliability of certified equipment mean fewer replacements, less downtime, and reduced risk of expensive accidents. These savings, in turn, can be allocated to other critical areas of operation, enhancing overall business efficiency.
Brand Reputation: Employing ATEX-certified equipment positively reflects on a company’s brand reputation. It demonstrates a commitment to high safety standards and regulatory compliance, which can significantly influence clients’ and investors’ perceptions. In an era where corporate responsibility is under the microscope, showcasing a commitment to safety can set a company apart.
Intrinsically Safe Store understands the criticality of adhering to ATEX standards and supplies a comprehensive range of certified safe solutions tailored to industries operating in hazardous areas. From intrinsically safe iPad cases to advanced natural gas detectors, our products are designed to ensure both compliance and peace of mind. Our enduring mission to “connect people with a billion certified safe solutions to improve our world” emphasizes our dedication to enhancing safety across global industries, affirming our role as leaders in the provision of intrinsically safe equipment.
Elevate Your Safety Standards with ATEX Certification Equipment
In an environment where safety cannot be compromised, ensuring that your equipment meets the highest standards is not just an option—it’s a necessity. At Intrinsically Safe Store, we understand the critical nature of operating in hazardous environments. Our range of ATEX Certification Equipment is designed to offer peace of mind, assuring that your operations not only comply with stringent safety regulations but also safeguard your most valuable asset: your people.
Why choose ATEX Certified Equipment from Intrinsically Safe Store?
- Comprehensive Safety Solutions: Our selection goes beyond just meeting the basics; it’s about enhancing your safety protocols with certified, reliable equipment.
- Industry Expertise: Leverage our experience in serving sectors like oil and gas and chemical plants to find equipment ideally suited to your specific safety challenges.
- Global Compliance: With ATEX Certification, you’re not just meeting local safety standards; you’re aligning with globally recognized practices to ensure safety and efficiency.
Don’t wait for an incident to reveal the importance of certified safety equipment. Explore our ATEX Certified solutions today and take a significant step toward a safer and more compliant future.
Discover Our ATEX Certified Equipment →
Connect with certified safe solutions and improve our world with Intrinsically Safe Store.
Types of Hazards: Gas Vs. Dust Explosive Environments
When discussing the necessity for ATEX certification equipment, it’s crucial to understand the distinct types of hazards that necessitate such specialized safety measures. Industries operating in hazardous environments are primarily dealing with two types of explosive atmospheres: gas and dust. Both environments present unique challenges that demand the use of appropriately certified equipment to ensure safety and compliance.
Gas Explosive Environments
Gas explosive environments are characterized by the presence of flammable gases or vapors. These atmospheres are common in industries such as oil and gas, petrochemicals, and pharmaceuticals. In such environments, a small spark can trigger an explosion if the concentration of gas or vapor in the air reaches a certain level. Equipment used in these settings must be designed to prevent the ignition of these gases, even under fault conditions. ATEX certified equipment for gas explosive environments is categorized under zones 0, 1, and 2, with zone 0 being an area where hazardous explosive atmosphere is present continuously or for long periods.
Dust Explosive Environments
On the other hand, dust explosive environments are found in industries like agriculture, food processing, and metalworking, where fine particles suspended in the air can become combustible under certain conditions. Unlike gas explosions, dust explosions can occur when there is a sufficient concentration of dust, an ignition source, and oxygen. The combustible dust can include substances like flour, sugar, grain, coal, or metal powders. ATEX certified equipment for dust explosive environments is categorized under zones 20, 21, and 22, with zone 20 being an area where an explosive atmosphere in the form of a cloud of combustible dust in the air is present continuously or for long periods.
The selection of ATEX certification equipment must be guided by a thorough understanding of the specific hazards present in each unique environment. Intrinsically Safe Store offers a broad range of products designed to meet the stringent requirements of both gas and dust explosive environments. From intrinsically safe iPad cases to handheld scanners and natural gas detectors, our equipment is engineered to offer reliability and performance while ensuring the safety of personnel and compliance with the most rigorous safety standards.
Whether you operate in a gas or dust explosive environment, the key to mitigating risks is the effective identification of hazards and the implementation of the correct safety measures, including the use of ATEX certified equipment. By recognizing the distinct nature of gas and dust explosive environments, industries can better prepare and equip themselves to maintain safety and compliance in these high-risk conditions.
The ATEX Equipment Directive Explained
Operating in hazardous environments demands strict compliance with safety standards to protect both personnel and equipment. The ATEX Equipment Directive is a critical component of these safety requirements, especially within industries like oil and gas, chemical processing, and others that face explosive risks. ATEX, derived from the French phrase “Atmosphères Explosibles”, pertains to equipment intended for use in potentially explosive atmospheres. Understanding this directive is paramount for industries committed to maintaining safety and compliance in perilous conditions.
The ATEX Equipment Directive, officially known as Directive 2014/34/EU, outlines the requirements that equipment must meet to be deemed safe for use in explosive atmospheres. This encompasses a broad range of equipment, including electrical and non-electrical devices, safety protection systems, and components. The directive categorizes explosive atmospheres as those filled with flammable gases, mists, vapors, or combustible dusts, where a spark or high surface temperature could ignite an explosion.
For equipment to receive ATEX certification, it must undergo rigorous testing and evaluation to ensure it can safely operate within these environments without igniting an explosive atmosphere. This involves assessing the equipment’s design, manufacturing processes, and its potential to generate sparks or reach temperatures that could trigger an explosion. Only after successfully passing these evaluations can equipment bear the ATEX marking, signifying its compliance with the directive.
Manufacturers and suppliers, such as Intrinsically Safe Store, play a pivotal role in offering ATEX certified equipment, ensuring that industries operating in hazardous environments have access to products that meet these stringent standards. From intrinsically safe iPad cases to handheld scanners and natural gas detectors, the availability of certified equipment facilitates safer operations across various sectors, adhering to the directive’s objective of minimizing the risk of explosions.
Compliance with the ATEX Equipment Directive not only enhances safety but also underlines an organization’s commitment to upholding global safety standards. It’s a testament to proactive risk management, safeguarding both human lives and infrastructure against the inherent dangers of explosive atmospheres. For companies like Intrinsically Safe Store, aligning with such directives is at the core of their mission to connect industries with certified safe solutions, driving forward the ultimate goal of improving safety worldwide in high-risk environments.
Classification of ATEX Equipment Zones
Understanding the classification of ATEX equipment zones is critical for industries operating in hazardous environments. These classifications are designed to ensure that the right level of protection is provided in areas where the presence of flammable gases, vapors, or combustible dust might pose a risk of explosion. The ATEX directive divides areas into zones based on the frequency and duration of the presence of explosive atmospheres.
Zones for Gas, Vapors, and Mists
- Zone 0 (Category 1G): An area in which an explosive atmosphere consisting of a mixture with air of dangerous substances in the form of gas, vapor, or mist is present continuously or for long periods or frequently.
- Zone 1 (Category 2G): An area in which an explosive atmosphere consisting of a mixture with air of dangerous substances in the form of gas, vapor, or mist is likely to occur in normal operation occasionally.
- Zone 2 (Category 3G): An area in which an explosive atmosphere consisting of a mixture with air of dangerous substances in the form of gas, vapor, or mist is not likely to occur in normal operation but, if it does occur, will persist for a short period only.
Zones for Dust
- Zone 20 (Category 1D): An area in which an explosive atmosphere in the form of a cloud of combustible dust in air is present continuously, for long periods or frequently.
- Zone 21 (Category 2D): An area in which an explosive atmosphere in the form of a cloud of combustible dust in air is likely to occur in normal operation occasionally.
- Zone 22 (Category 3D): An area in which an explosive atmosphere in the form of a cloud of combustible dust in air is not likely to occur in normal operation but, if it does occur, will persist for a short period only.
The selection of ATEX Certified Equipment must align with the specific zone classification to ensure optimal safety and compliance. Intrinsically Safe Store, understanding the paramount importance of this alignment, offers a wide range of products specifically designed to meet the rigorous requirements of the ATEX directive. Whether your operations fall within the gas-based zones or dust-based environments, our inventory includes intrinsically safe iPad cases, handheld scanners like the BCS 3600 series, and natural gas detectors that are certified for use in these hazardous conditions.
By utilizing ATEX Certified Equipment tailored for the specific classified zone, industries can markedly reduce the risk of incidents arising from explosions, thereby ensuring the safety of their operations and compliance with safety standards. Intrinsically Safe Store is committed to providing certified safe solutions that fulfill this need, supporting industries to navigate the complexities of operating safely in hazardous environments.
Guidelines for Installation and Maintenance of ATEX Equipment
Ensuring the safety and compliance of workplaces in hazardous environments begins with proper installation and rigorous maintenance of ATEX-certified equipment. ATEX certification signifies that equipment is safe to use in explosive atmospheres, but this safety can only be maintained with the correct handling. Here’s a comprehensive set of guidelines to help you secure the safe installation and maintenance of ATEX-certified equipment.
Installation Guidelines
- Understand the Classification: Before installation, it’s crucial to understand the zone classification of your environment. ATEX covers zones 0, 1, and 2 for gases, vapors, and mists, and zones 20, 21, and 22 for dusts. Each zone has specific requirements for equipment usage.
- Use Qualified Personnel: Only technicians with ATEX compliance training should install this equipment. Their understanding of the complexities associated with hazardous areas ensures that equipment is installed safely and correctly.
- Follow Manufacturer Instructions: Always adhere to the detailed installation guidelines provided by the equipment manufacturer. These instructions are often specific to the hazardous environment the equipment is designed for.
- Grounding and Bonding: Proper grounding and bonding are essential to prevent static electricity, which can ignite explosive atmospheres. Ensure that all equipment and conducting parts are correctly grounded.
Maintenance Guidelines
- Regular Inspections: Schedule regular inspections to ensure that ATEX equipment is functioning correctly and safely. Look for physical damages, worn-out parts, or any other sign that could compromise safety.
- Documentation: Keep detailed records of all maintenance activities. Documentation should include inspection dates, findings, actions taken, and the name of the person performing the maintenance. This provides a safety audit trail and helps with regulatory compliance.
- Training: Maintenance personnel must be trained not just in general maintenance practices but specifically in the maintenance of ATEX-certified equipment. Furthermore, they should be aware of the hazards specific to the environment in which the equipment operates.
- Replacement Parts: Only use replacement parts that are certified for use in hazardous environments. Non-certified parts might fit physically, but they can fail under operating conditions and compromise safety.
- Cleaning Procedures: Dust and other residues can alter the thermal or ignition resistance properties of equipment. Implement and follow strict cleaning procedures to prevent the build-up of potentially explosive materials.
By adhering to these guidelines, industries operating in hazardous environments can ensure the safety and longevity of their ATEX-certified equipment. Remember, the goal is not just compliance, but creating a workplace where safety is paramount, aligning with Intrinsically Safe Store’s mission to connect people with certified safe solutions to improve safety globally.
With a comprehensive understanding of installation and maintenance guidelines, companies can significantly mitigate risks associated with explosive atmospheres, ensuring a safer and efficient operational environment for all involved.
Challenges and Solutions in ATEX Compliance
Ensuring the safety of equipment used in hazardous environments presents a myriad of challenges, but with the right knowledge and solutions, compliance with ATEX certification can be effectively managed. Below, we delve into some of the common challenges industries face regarding ATEX compliance and how they can navigate these hurdles.
Understanding the Complex Requirements
Challenge: The first significant hurdle is the complexity of ATEX directives themselves. With detailed classifications for different types of hazardous environments, understanding the specific requirements for equipment certification can be daunting.
Solution: Staying informed about ATEX directives is crucial. Utilizing resources such as the official ATEX guidelines and participating in relevant training sessions can be invaluable. Intrinsically Safe Store, with its expertise in certified intrinsically safe products, provides consultation and products that meet these stringent requirements, thereby simplifying the compliance process for businesses.
Choosing the Right Equipment
Challenge: Selecting equipment that is certified for the exact classification of hazardous area in which it will be used can be challenging. The risk of choosing incorrectly categorized equipment can lead to non-compliance and safety hazards.
Solution: Working with specialized vendors like Intrinsically Safe Store, which offers a wide range of ATEX-certified equipment, ensures that businesses procure the appropriate tools for their specific needs. Their product ranges, including intrinsically safe iPad cases and natural gas detectors, are tailored for use in various hazardous environments, ensuring compliance and safety.
Maintaining Equipment to ATEX Standards
Challenge: Keeping equipment compliant over time poses another challenge. The harsh conditions in hazardous areas can degrade equipment faster than in standard environments, potentially compromising its ATEX certification status.
Solution: Regular maintenance and inspections are key to ensuring long-term compliance. Intrinsically Safe Store not only supplies ATEX-certified equipment but also provides guidance on maintaining these standards. This involves routine checks and understanding when equipment needs to be replaced or upgraded to maintain safety and compliance.
Training Staff on ATEX Compliance
Challenge: Ensuring all personnel are adequately trained on the importance of ATEX compliance and how to correctly use certified equipment could be a hurdle, especially in industries with high turnover rates.
Solution: Implementing ongoing training programs is essential. Intrinsically Safe Store supports industries by offering insights and resources for training staff. By fostering a culture of safety and compliance, businesses can mitigate risks associated with human error and ensure their operations remain within ATEX directives.
Navigating the complexities of ATEX compliance is surely challenging, but with a comprehensive understanding of the requirements and the support of experienced partners like Intrinsically Safe Store, industries can confidently operate safely and efficiently in hazardous environments.
FAQs on ATEX Certified Equipment
What are the primary goals of ATEX legislation?
The primary goals of the ATEX (ATmosphères EXplosibles) legislation are to ensure the safety and health of workers and the protection of property by preventing explosions in areas with an explosive atmosphere. ATEX legislation sets requirements for equipment and protective systems intended for use in potentially explosive atmospheres. These rules apply to manufacturers, suppliers, and users of equipment in the EU and EEA countries, aiming to mitigate the effects of explosions and enhance workplace safety in hazardous environments.
Which countries require ATEX certification?
ATEX certification is mandatory within the European Union (EU) and the European Economic Area (EEA). It applies to all member states, ensuring a harmonized level of protection for workers and environments at risk of explosions. Countries outside the EU and EEA, such as Switzerland, often adopt similar regulations to facilitate trade and maintain safety standards, although they are not legally bound by the ATEX directives. Manufacturers exporting to the EU from countries like the USA, Canada, and others need to comply with ATEX standards for equipment used in explosive atmospheres.
What does ATEX Ex marking signify?
ATEX Ex marking on equipment signifies that the product complies with the ATEX directives and is safe for use in explosive atmospheres. The Ex mark is followed by additional information that provides insights into the product’s suitability for particular hazardous areas, such as the type of protection it offers, the gas or dust group it is designed for, and its temperature class. This marking is crucial for industries operating in hazardous environments as it helps in selecting the appropriate equipment for specific zones, ensuring safety and compliance.
Can North American equipment be ATEX certified?
Yes, North American equipment can be ATEX certified. Manufacturers from North America can obtain ATEX certification for their products by ensuring they meet the essential health and safety requirements specified in the ATEX directives. This often involves adjustments in design and testing to comply with European standards. Manufacturers must work with a notified body, an organization designated by EU countries to assess the conformity of products before entering the EU market. Obtaining ATEX certification allows North American manufacturers to export their intrinsically safe equipment to the EU and EEA countries.
What are the costs involved in obtaining ATEX certification?
The costs involved in obtaining ATEX certification can vary significantly depending on several factors, such as the complexity of the equipment, the level of redesign needed to meet compliance, testing, and documentation requirements. Initial costs may include compliance testing, certification fees from a notified body, and possible engineering modifications. Manufacturers must also consider ongoing costs related to maintaining certification, such as periodic surveillance audits and updates to documentation or product design to comply with any changes in ATEX directives. These investments, however, are essential for accessing markets within the EU and EEA, ensuring safety, and complying with legal requirements.