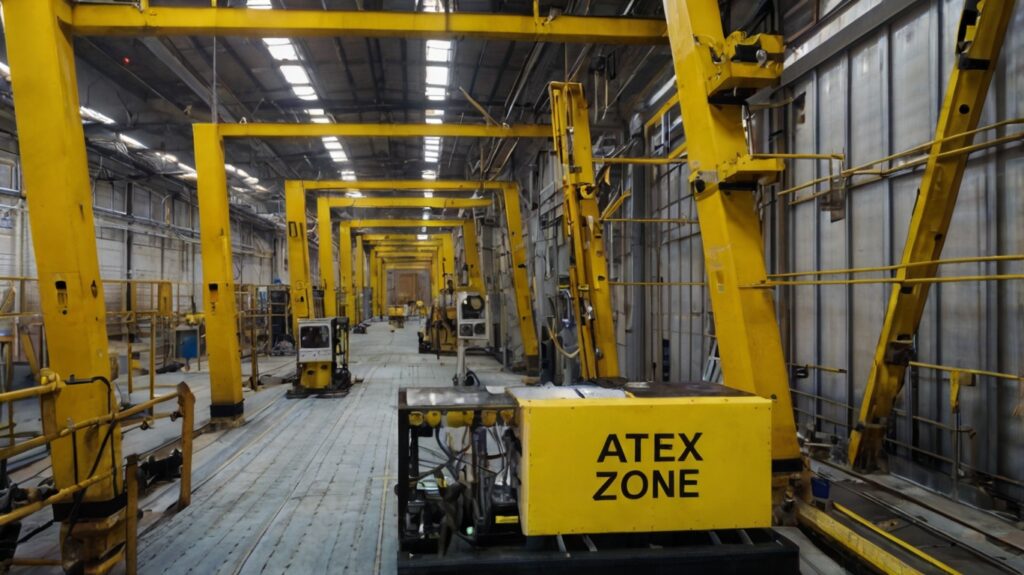
Definition: ATEX Zone 1 and Zone 2 certifications are standards defined by the European Union’s ATEX (ATmosphères EXplosibles) directives to ensure the safe operation of equipment in potentially explosive atmospheres.
ATEX Zone 1
- Definition: ATEX Zone 1 refers to areas where an explosive atmosphere, consisting of a mixture with air of flammable substances in the form of gas, vapor, or mist, is likely to occur occasionally in normal operation. This can be due to repair, maintenance operations, or leakage
- Requirements: Equipment must be designed to prevent ignition of the explosive atmosphere, even under fault conditions. This includes intrinsically safe designs and explosion-proof constructions to eliminate any risk of ignition.
ATEX Zone 2
- Definition: ATEX Zone 2 areas are those where an explosive atmosphere is not likely to occur in normal operation but, if it does occur, will persist for a short period only. This zone represents a lower risk compared to Zone 1 but still requires specific safety measures.
- Requirements: Equipment must undergo rigorous testing and evaluation to ensure it can operate safely without igniting any potential explosive air mixtures. This includes selecting products specifically marked for ATEX Zone 2 use and adhering to strict installation and maintenance standards.
Science Behind It: The ATEX directives (2014/34/EU for equipment and 1999/92/EC for workplace safety) set strict guidelines to ensure that equipment does not ignite flammable substances. The certification process involves designing equipment to be intrinsically safe, preventing electrical or thermal ignition sources, and ensuring compliance with specific safety standards through rigorous testing and evaluation.
- Understanding ATEX Zones: The classification of hazardous areas into ATEX Zone 1 and Zone 2 is crucial for selecting the appropriate safety equipment, as it dictates different safety requirements and equipment certifications based on the likelihood and duration of explosive atmospheres.
- Key Differences: ATEX Zone 1 is characterized by the potential for explosive atmospheres to occur occasionally during normal operations, necessitating more stringent equipment requirements, while Zone 2 is where such atmospheres are unlikely during normal operations but may appear briefly, allowing for less stringent protective measures.
- Compliance Costs: Ensuring compliance with safety standards for Zone 1 typically incurs higher certification and ongoing maintenance costs due to stringent safety measures, whereas Zone 2 involves lower costs but still requires adherence to safety protocols to mitigate risks associated with explosive atmospheres.
Defining ATEX Zones: Zone 1 and Zone 2
Understanding the classification of hazardous areas is crucial for selecting the appropriate safety equipment for environments where explosive atmospheres may exist. The ATEX directive, a key regulatory framework in the European Union, categorizes environments into zones based on the frequency and duration of the occurrence of an explosive atmosphere. Among these, Zone 1 and Zone 2 are significant classifications for areas where flammable gases, vapors, or mist can be present.
ATEX Zone 1 is defined as an area in which an explosive atmosphere consisting of a mixture with air of dangerous substances in the form of gas, vapor, or mist is likely to occur in normal operation occasionally. The key term here is “likely to occur in normal operation occasionally.” It implies that the design of equipment for these areas must ensure a high level of protection, as the exposure to the explosive atmosphere is not constant but can be expected during the normal operation of the facility.
ATEX Zone 2, on the other hand, is characterized as an area where an explosive atmosphere is not likely to occur in normal operation but, if it does occur, will persist for a short period only. This classification acknowledges that while the occurrence of an explosive atmosphere is less likely than in Zone 1, the presence of flammable substances and the possibility of their ignition cannot be entirely ruled out. Therefore, equipment certification for use in Zone 2 focuses on ensuring safety in instances where an explosive atmosphere could unexpectedly arise.
The distinctions between ATEX Zone 1 and Zone 2 primarily lie in the frequency and duration of the explosive atmosphere’s presence. These classifications significantly influence the selection of equipment and safety measures implemented within these zones. Equipment destined for Zone 1 areas typically requires more stringent protection features compared to Zone 2, given the higher probability and frequency of encountering an explosive atmosphere.
For professionals and organizations operating in hazardous areas, understanding these distinctions is integral to ensuring the correct and safe selection of equipment, including intrinsically safe devices and explosion-proof equipment. The Intrinsically Safe Store, with its expertise in offering high-quality, certified equipment, provides solutions that meet the rigorous standards set forth by ATEX Zone 1 and Zone 2 certifications. Whether the need is for LED work lights, cameras, or robust casing for electronics, ensuring the right certification is critical in preventing explosions and safeguarding the safety of personnel in hazardous environments.
Ensure Safety with Certified Equipment
In hazardous environments, the right equipment is not just a requirement; it’s a necessity to ensure safety and compliance. At the Intrinsically Safe Store, we specialize in providing industry professionals with high-quality and rigorously tested safety equipment certified for ATEX Zone 1 and Zone 2 environments. Our selection of products is designed to meet the unique needs of industries operating within explosive atmospheres, such as petrochemical and mining sectors.
Here’s why you should choose us for your safety equipment needs:
- Certified Safety: All our products are ATEX certified, ensuring they meet the stringent requirements for safe operation in explosive environments.
- Extensive Range: From intrinsically safe cameras to LED work lights and smartphone cases, we have a wide variety of equipment to suit your specific needs.
- Prevention Focus: Our explosion-proof and intrinsically safe devices are designed to prevent the ignition of flammable gases or vapors, thereby ensuring the safety of your personnel and facilities.
Don’t compromise on safety. Explore our range of certified ATEX Zone 1 and Zone 2 compliant equipment today and uphold the highest standards of safety and compliance within your operations. Ensure the safety of your team and operation—visit the Intrinsically Safe Store now.
Key Differences between ATEX Zone 1 and Zone 2
When it comes to working in hazardous environments, understanding the distinctions between ATEX Zone 1 and Zone 2 is crucial for selecting the appropriate safety equipment and ensuring compliance with regulations. ATEX certification plays a vital role in protecting both personnel and facilities by categorizing areas where explosive atmospheres may occur and specifying the requirements for the equipment used in these areas.
Nature of Explosive Atmospheres
ATEX Zone 1 is defined as an area in which an explosive atmosphere consisting of a mixture with air of flammable substances in the form of gas, vapor, or mist is likely to occur in normal operation occasionally. This categorization necessitates that equipment must be designed to prevent ignition sources under regular operating conditions and even some fault conditions.
Conversely, ATEX Zone 2 is characterized as a place where an explosive atmosphere is not likely to occur in normal operation, but if it does occur, it will persist for a short period only. For Zone 2, the prevention strategies are focused on normal operation and are less stringent compared to Zone 1, reflecting the lower risk of explosive atmosphere formation.
Equipment Certification and Requirements
Equipment meant for use in Zone 1 must be designed to ensure a high level of protection. It often incorporates measures to guarantee it can operate safely even when exposed to explosive atmospheres for extended periods. This includes utilizing intrinsically safe design principles that limit the energy available for ignition, alongside other protective measures.
For Zone 2, the equipment certification focuses on ensuring that devices do not generate sparks or reach temperatures that could ignite an explosive atmosphere during typical operation. The designs might not require as rigorous protective features as Zone 1, reflecting the reduced likelihood and duration of encountering an explosive atmosphere.
Impact on Equipment Selection
Selecting the appropriate ATEX-certified equipment for either Zone 1 or Zone 2 requires understanding the specific risks associated with each zone. For Zone 1 environments, where the presence of explosive gases or vapors is more common, equipment must adhere to stricter safety standards and often employs advanced safety features. This might include intrinsically safe cameras, LED work lights, and communication devices specifically designed to operate safely in such conditions without causing ignition.
In Zone 2 areas, where explosive atmospheres occur less frequently and for shorter durations, the selection of certified equipment might allow for devices that, while still safe and compliant, are designed for less frequent exposure to hazardous conditions. This can include a range of explosion-proof and intrinsically safe tools and equipment that are engineered to prevent ignition in the case of accidental exposure to an explosive atmosphere.
Understanding these key differences between ATEX Zone 1 and Zone 2 is essential for professionals and organizations operating in hazardous environments. It ensures not only compliance with safety regulations but also the protection of workers and facilities in industries such as petrochemical, mining, and others faced with the risk of explosive atmospheres. The Intrinsically Safe Store provides a wide array of certified and compliant products tailored to meet the stringent requirements of both zones, embodying their commitment to preventing explosions and ensuring safety in hazardous environments.
Criteria for Classification into Zone 1 or Zone 2
The classification of an area into ATEX Zone 1 or Zone 2 is a critical step in ensuring the appropriate level of safety and compliance with regulations for workplaces operating in hazardous environments. This classification determines the specific requirements for equipment and safety protocols to prevent explosions and protect workers. Understanding the criteria for classification is essential for professionals and organizations operating in sectors such as petrochemical, mining, and others where explosive atmospheres pose a significant risk.
Presence and Frequency of Explosive Atmospheres
- Zone 1: This classification applies to areas where explosive atmospheres, consisting of a mixture of air and flammable substances in the form of gas, vapor, or mist, are likely to occur in normal operation. The key criterion for Zone 1 is the regular presence of an explosive atmosphere during routine operations or maintenance tasks.
- Zone 2: In contrast, Zone 2 areas are those where an explosive atmosphere is not likely to occur in normal operation. If it occurs, it will only exist for a short period. This classification is for spaces where the presence of hazardous materials is less frequent and the risk of explosion is lower compared to Zone 1 areas.
Nature and Source of Hazardous Material
The specific nature and source of the flammable substances present in the environment play a significant role in the classification process. The substances can range from gases and vapors to mists and dusts, each with its own properties and explosive potentials. The volatility, concentration, and potential energy release of these substances are carefully evaluated to assess the overall risk they pose in the workplace.
Industry-Specific Considerations
Different industries may face varying levels of risk based on the materials they handle and their operational processes. For instance, the petrochemical sector typically involves higher concentrations of flammable gases and liquids, increasing the likelihood of encountering Zone 1 areas within facilities. Conversely, in sectors where explosive materials are handled less frequently or in lower quantities, Zone 2 classifications may be more common.
The classification into Zone 1 or Zone 2 directly impacts the selection and certification of equipment used in these areas. For the Intrinsically Safe Store, understanding these classifications ensures that we offer the right products that meet the stringent safety requirements for each zone. Our range of intrinsically safe and explosion-proof equipment is designed to provide optimal protection in both Zone 1 and Zone 2 areas, ensuring the safety of personnel and compliance with ATEX Zone 1 and Zone 2 Certifications.
Hazards and Risks in ATEX Zone 1
ATEX Zone 1 represents a hazardous environment where flammable gases, vapors, or mists are likely to occur during normal operation. These areas require stringent controls and safety measures to prevent accidents and ensure the safety of personnel operating within these zones. Understanding the risks and hazards specific to ATEX Zone 1 is crucial for selecting the appropriate equipment and implementing the necessary safety protocols.
Identification of Hazards
The primary risk in ATEX Zone 1 environments stems from the presence of flammable substances in the air, which can ignite if exposed to a spark or high temperatures. The likelihood of such an atmosphere existing means that equipment and electrical installations must be designed to prevent the initiation of an explosion. Flammable gases and vapors, like methane in the petrochemical industry or ethanol vapors in pharmaceuticals, can form explosive mixtures with air, which are highly sensitive to ignition sources.
Types of Risks
The risks in ATEX Zone 1 areas can vary significantly depending on the industry and the specific operations performed. Some common risks include:
- Explosions and Fires: The most significant risk in Zone 1 environments is the potential for explosions and subsequent fires, which can result in severe injury, fatalities, and property damage.
- Toxic Exposure: In some cases, the flammable substances present in the air may also be toxic, posing health risks to workers through inhalation or skin contact.
- Electrical Shock: The use of electrical equipment not designed for hazardous locations can lead to short circuits or sparks, which, aside from igniting flammable atmospheres, may also expose workers to electrical shock.
Safety Measures and Equipment Certification
To mitigate these risks, equipment used in ATEX Zone 1 areas must be specifically certified for use under such conditions. Intrinsically safe and explosion-proof products are designed to ensure that any electrical or thermal energy present is insufficient to ignite the hazardous atmosphere. This certification process involves rigorous testing to ensure that each product meets the strict safety standards required for operation in these environments.
The Intrinsically Safe Store understands the critical importance of using properly certified equipment in hazardous areas. Their selection of products for use in ATEX Zone 1 environments includes intrinsically safe cameras, LED work lights, flashlights, and protective cases, all designed to provide maximum safety and reliability. By choosing equipment that meets ATEX Zone 1 and Zone 2 certifications, organizations can effectively reduce the risk of accidents, protecting both their personnel and infrastructure from the dangers posed by explosive atmospheres.
Adhering to these safety measures and choosing the right certified equipment is not just a regulatory requirement but a fundamental aspect of ensuring workplace safety in hazardous environments. The commitment of The Intrinsically Safe Store to provide high-quality, certified intrinsically safe and explosion-proof products exemplifies the dedication needed to maintain safety standards and protect lives in these critical areas.
Hazards and Risks in ATEX Zone 2
ATEX Zone 2 represents areas where an explosive atmosphere is not likely to occur in normal operation, but if it does occur, it will persist for a short period only. Understanding the hazards and risks associated with work in ATEX Zone 2 is crucial for selecting the right safety equipment and for maintaining a safe work environment in industries like petrochemical and mining, where the presence of flammable gases, vapors, or mists can’t be entirely ruled out.
In contrast to Zone 1, where the presence of explosive atmospheres is expected as a regular part of operations, Zone 2 areas are typically characterized by their lower risk level. However, low risk does not mean no risk. The sporadic occurrence of an explosive atmosphere in Zone 2, if ignited, could lead to disastrous consequences, including significant harm to personnel and property. This makes the mitigation of ignition sources—be it electrical equipment, hot surfaces, or operational sparks—a primary concern for safety protocols in such areas.
The types of hazards present in Zone 2 may vary significantly depending on the specific industry and operation being conducted. Common sources include the processing, storage, and transport of flammable materials, which, under abnormal conditions, could leak or release into the atmosphere forming a hazardous environment. Equipment failure, operational errors, or accidental releases are typical scenarios that might lead to the formation of an explosive atmosphere in these areas.
To address these risks, it is imperative for organizations operating in such zones to equip their workforce with ATEX Zone 2 certified equipment. This certification ensures that the devices, whether they are LED work lights, flashlights, cameras, or any other intrinsically safe devices, are designed to prevent ignition of flammable materials in the atmosphere under normal operating conditions. The design of these devices ensures that they do not store enough energy to cause ignition, whether through electrical or thermal sources.
In addition, organizations must implement stringent safety protocols, including regular monitoring of atmospheric conditions, thorough risk assessments, and personnel training focused on the identification and prevention of hazards specific to ATEX Zone 2. Ensuring the use of equipment certified for Zone 2, alongside robust safety measures, significantly contributes to reducing the risks associated with working in environments where explosive atmospheres can occur under abnormal conditions.
Comparing Compliance Costs for Zone 1 and Zone 2 Equipment
Understanding the financial impact of compliance for equipment in ATEX Zone 1 and Zone 2 environments is crucial for businesses operating within hazardous areas. The cost of ensuring that safety equipment meets the stringent requirements of these zones varies significantly and can affect the overall operational budget and safety investment strategy of a company.
Initial Certification and Testing
The initial cost of certifying and testing equipment for use in Zone 1 areas is typically higher than for Zone 2. This is due to the more demanding environment in Zone 1, where the presence of explosive atmospheres is considered to be a regular occurrence. Equipment used in these areas must undergo rigorous testing to ensure it can safely operate without triggering an ignition. The complexity and thoroughness of these tests contribute to the higher cost of Zone 1 certification. However, this investment is crucial for maintaining the highest safety standards in potentially explosive environments.
In contrast, Zone 2, characterized by the occasional presence of dangerous substances, requires less stringent protection measures. Although safety remains a paramount concern, the equipment designated for Zone 2 areas undergoes a slightly less rigorous testing procedure, resulting in lower certification costs compared to Zone 1 equipment.
Maintenance and Inspection
Maintaining compliance doesn’t end with the initial certification. Equipment in both zones requires regular inspection and maintenance to ensure ongoing safety and compliance. However, Zone 1 equipment typically incurs higher ongoing costs due to the need for more frequent inspections and the potential for more complex maintenance procedures. These are necessary to mitigate the greater risk of exposure to explosive atmospheres.
Zone 2 equipment, while still requiring regular maintenance checks, often has lower associated costs for these activities. The less severe environmental conditions mean that equipment can typically be inspected less frequently and may have a longer lifespan, reducing the overall maintenance expense.
Cost of Non-Compliance
It is also important to consider the cost of non-compliance. Failing to meet the requirements for equipment certification in either Zone 1 or Zone 2 can result in severe penalties, including fines and operational shutdowns. Furthermore, the risk of accidents and explosions due to non-compliant equipment can lead to significant costs associated with damage repair, legal liabilities, and loss of reputation. These potential expenses far outweigh the initial and ongoing costs of ensuring compliance.
Conclusion
Navigating the compliance costs for ATEX Zone 1 and Zone 2 certified equipment is a critical aspect of managing safety in hazardous environments. While Zone 1 certification and maintenance undoubtedly require a higher financial investment, the cost of non-compliance can be much greater, regardless of the zone. Companies must weigh these costs against the potential risks and liabilities of operating in explosive atmospheres. Investing in high-quality, certified equipment, such as those offered by The Intrinsically Safe Store, not only ensures compliance but also demonstrates a commitment to the highest safety standards and protection of personnel and assets in hazardous environments.
FAQs on ATEX Zone 1 and Zone 2 Certifications
What types of gases or dusts are typical in Zone 1 and Zone 2 areas?
Zone 1 environments are areas where flammable gases, vapors, or liquids can exist under normal operating conditions. This could include places like the production areas in chemical plants or areas around oil refinery processing units. Common gases might include hydrogen, methane, or ethylene. Zone 2 areas are locations where a flammable atmosphere is not likely to occur in normal operation but, if it does occur, will persist for a short period only. This might involve storage areas for volatile liquids or gas bottling plants. In both zones, dusts could include metal powders, coal, grain flour, or wood dust, depending on the industry.
Can Zone 1 certified equipment be used in Zone 2?
Yes, Zone 1 certified equipment can be used in Zone 2 areas because it is designed to offer a higher level of protection. Since Zone 1 certification requires equipment to be safe in environments where explosive atmospheres are likely to occur more frequently than in Zone 2, it naturally meets or exceeds the safety requirements for Zone 2.
Can Zone 2 certified equipment be used in Zone 1?
No, Zone 2 certified equipment cannot be used in Zone 1 areas. The equipment certified for Zone 2 is only designed to withstand environments where explosive atmospheres are present under abnormal conditions. Since Zone 1 environments have a higher probability of encountering an explosive atmosphere, Zone 2 equipment might not offer adequate protection.
How does the frequency of explosive atmosphere occurrence affect ATEX zoning?
ATEX zoning is significantly influenced by the frequency and duration of the presence of an explosive atmosphere. Zone 0 and Zone 1 are designated for areas where explosive gas atmospheres are present continuously, intermittently, or for long periods. Zone 1 specifically relates to places where an explosive atmosphere is likely to occur in normal operation. Conversely, Zone 2 is for areas where an explosive atmosphere is not likely and, if it does occur, it is expected to be present for a short duration only. The categorization into zones helps in the selection of appropriate equipment and protective systems based on their ability to prevent sparks or temperature conditions that could ignite an explosive atmosphere.
What are the common sources of ignition that ATEX certification aims to control?
ATEX certification aims to control several sources of ignition to reduce the risk of explosions in hazardous areas. These sources include electrical sparks, hot surfaces, static electricity, electromagnetic waves, and mechanical sparks. The certification process involves assessing and testing equipment to ensure it does not produce these sources of ignition when used within its designated environment. This includes evaluating components like motors, switches, and other electrical parts, as well as considering the design and construction of the equipment to control temperatures and prevent the accumulation of static electricity.
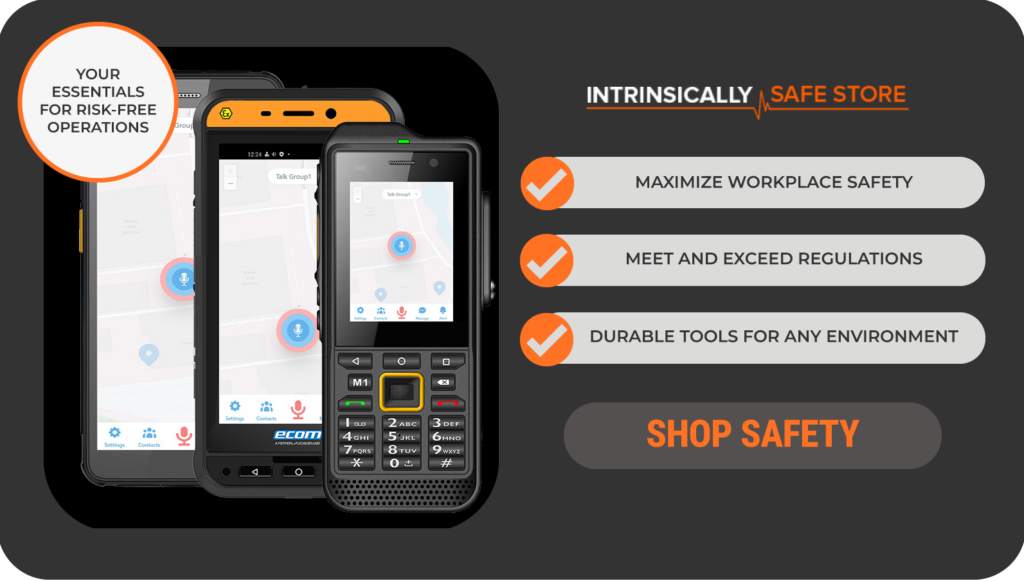