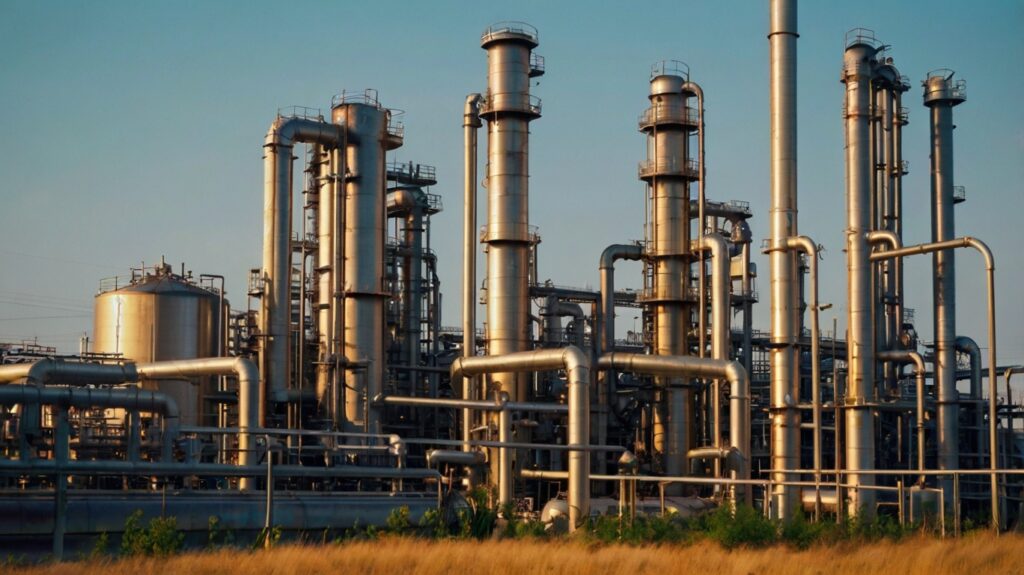
Definition: ATEX Zone 1 devices are designed for use in areas within chemical plants where an explosive atmosphere consisting of a mixture with air or flammable substances in the form of gas, vapour, or mist is likely to occur occasionally during normal operation. These devices are crucial for ensuring the safety of both personnel and equipment in hazardous environments.
Science Behind It: The ATEX (ATmosphères EXplosibles) directive, which is part of the EU’s regulatory framework, mandates that equipment used in these zones must be intrinsically safe. This means the devices must be designed so that they cannot generate enough electrical or thermal energy to ignite the surrounding explosive atmosphere, even in the event of a fault. The certification process involves rigorous testing and compliance with specific standards to ensure the equipment meets the required safety levels.
Examples in Action:
- RealWear Navigator Z1 and HMT-1Z1: These augmented reality (AR) headsets are certified for ATEX Zone 1, making them suitable for inspections, maintenance, and repairs in chemical plants and other potentially explosive areas.
- Industrial Equipment: Various industrial devices such as sensors, pumps, and control systems are designed and certified to meet ATEX Zone 1 standards. These devices are essential for safe operation in hazardous environments within chemical plants.
Key Features:
- Intrinsic Safety: Devices must be designed to prevent ignition of the explosive atmosphere, ensuring they cannot become a source of ignition through electrical or thermal energy.
- Environmental Durability: Equipment must be robust enough to withstand harsh conditions, including water and dust, often indicated by IP66 ratings[5].
- Compliance: Certification involves meeting specific EU norms and standards outlined in the ATEX Directive 2014/34/EU, ensuring ongoing conformity through quality assurance and periodic audits.
Certification Process: The certification process for ATEX Zone 1 equipment includes assembling technical documentation, rigorous testing and evaluation by a certification body, and implementing a quality system to ensure ongoing compliance. This process is essential for verifying that the equipment can operate safely without igniting an explosive atmosphere.
Importance: Using ATEX Zone 1 certified devices in chemical plants is critical for preventing accidents and ensuring compliance with legal requirements. Non-compliant equipment can pose significant risks to lives and result in substantial financial losses due to accidents and penalties.
- Understanding ATEX Zone 1 equipment certification is crucial for ensuring safety in chemical plants, focusing on aspects like temperature classification, protection concepts, and gas groups.
- Intrinsically safe communication devices, such as smartphones, tablets, radios, and headsets, are essential for maintaining effective communication in hazardous chemical plant environments.
- Challenges in maintaining ATEX Zone 1 equipment include adhering to complex technical and regulatory requirements, managing environmental conditions, and ensuring proper documentation.
The Basics of Zone 1 Equipment Certification
To ensure the safety of personnel and facilities in chemical plants, it is crucial to understand the essentials of Zone 1 equipment certification. Zone 1 is classified by the ATEX directive (Atmosphères Explosibles) as an area where an explosive atmosphere consisting of a mixture with air of flammable substances in the form of gas, vapor, or mist is likely to occur in normal operation occasionally. This classification underlines the importance of using specifically designed equipment that can safely operate within such environments.
ATEX Zone 1 devices for chemical plants are rigorously tested and certified to meet stringent safety standards. This certification ensures that the equipment can perform its intended function safely without becoming a source of ignition. The certification process examines several key aspects of the device:
- Temperature Classification: Devices are rated based on their maximum surface temperature. This is critical in preventing the ignition of flammable substances, which can have different auto-ignition temperatures.
- Protection Concepts: For electrical equipment, several protection concepts might be applied, such as ‘Intrinsic Safety (Ex i)’, ‘Flameproof Enclosure (Ex d)’, and ‘Increased Safety (Ex e)’. Each concept has its own criteria and is selected based on the specific needs and risks of the Zone 1 area.
- Gas Groups: Equipment is categorized according to the type of gases or vapors it is designed to be exposed to. These groups are categorized based on the physical properties of the gases, such as the ignition energy or the explosive pressure.
- IP Rating: The Ingress Protection (IP) rating measures the enclosure’s effectiveness against the ingress of dust and liquids. While not specific to explosive atmospheres, a high IP rating is often indicative of the robustness of the design, a critical feature for equipment used in hazardous environments.
To carry the ATEX certification mark, Zone 1 devices undergo rigorous testing by an authorized notified body. This ensures they not only meet the fundamental health and safety requirements but are also capable of withstanding the harsh operational conditions found in chemical plants without compromise to safety.
Understanding the specifics of ATEX Zone 1 certification is essential for selecting the right devices for chemical plants. By ensuring that all equipment meets these critical safety standards, plant operators can significantly reduce the risk of incidents, protect their personnel, and maintain continuous, safe operations in hazardous environments. The Intrinsically Safe Store specializes in providing equipment that meets these stringent standards, offering a wide range of ATEX Zone 1 certified devices to ensure the safety and efficiency of operations in chemical plants.
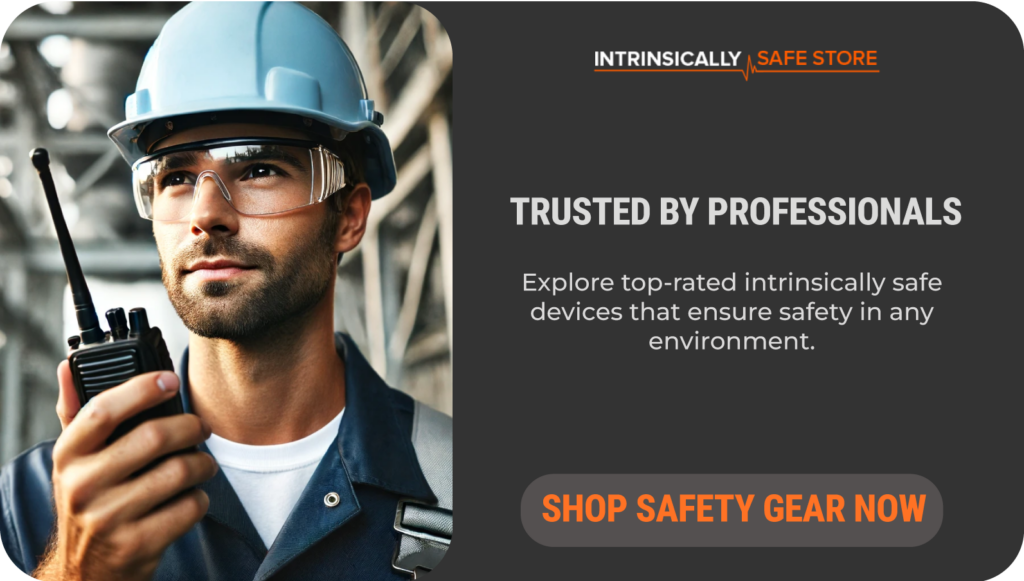
Discover the Right ATEX Zone 1 Devices Today
In the pursuit of maintaining the highest safety standards within hazardous environments, such as chemical plants, it is pivotal to ensure that the machinery and equipment used are not only effective but also compliant with ATEX Zone 1 regulations. At The Intrinsically Safe Store, we specialize in providing a vast inventory of intrinsically safe and explosion-proof devices designed to meet and exceed these rigorous safety requirements.
By choosing us for your safety equipment needs, you benefit from:
- A Wide Selection of ATEX Zone 1 Certified Devices: From intrinsically safe flashlights and gas detectors to explosion-proof cameras and lighting, our products ensure the safety of your operations without compromising on functionality.
- Expert Guidance and Support: Our knowledgeable team is on hand to assist you in selecting the right devices for your specific application, ensuring compliance and safety in your chemical plant.
- Quality and Compliance: All our products comply with international safety standards, giving you peace of mind that you are adequately protected in hazardous environments.
Embark on a journey toward enhanced safety at your facility. Visit The Intrinsically Safe Store today, and equip your team with the leading ATEX Zone 1 Devices for Chemical Plants. Safeguard your operations, protect your personnel, and ensure compliance with industry standards.
Intrinsically Safe Mobile Devices for Communication
In the hazardous atmospheres of chemical plants, maintaining clear and reliable communication is not just essential for operational efficiency but paramount for safety. ATEX Zone 1 devices designed specifically for chemical plants include a variety of intrinsically safe mobile devices that facilitate communication while ensuring the safety of the premises and its occupants.
Intrinsically Safe Smartphones and Tablets: These devices are engineered to operate safely in environments where flammable gases, vapors, or dust may be present. Modern intrinsically safe smartphones and tablets combine the functionality of a standard mobile device with robust safety features. They offer high-speed data transfer, real-time video sharing, and access to cloud-based services, all while adhering to ATEX Zone 1 requirements. This enables staff to communicate effectively, access critical information, and make informed decisions in real-time, without compromising safety.
ATEX-Certified Radios: Two-way radios certified for use in ATEX Zone 1 areas are indispensable for chemical plants. These radios are designed to ensure clear communication even in noisy environments and can be used in the presence of explosive gases and dust. With features like long battery life, robust build, and emergency signaling, they are an essential tool for teams that require constant communication.
Intrinsically Safe Headsets: To complement mobile devices and radios, intrinsically safe headsets are crafted to provide clear audio in the noisiest of environments. These headsets often feature noise cancellation and are designed to be worn comfortably with protective gear over extended periods. They permit hands-free operation, ensuring that workers can communicate effectively while maintaining safety protocols and focusing on their tasks.
For professionals and organizations operating in hazardous environments, such as those found in petrochemical, pharmaceutical, and mining industries, incorporating these intrinsically safe mobile devices into their safety and communication protocols is a significant step toward enhancing operational safety and efficiency. The Intrinsically Safe Store caters specifically to these needs, offering a range of devices that meet the strict ATEX standards for Zone 1 environments, thus ensuring that your team can communicate safely and efficiently, even in the most hazardous conditions.
Gas Detection Systems for Enhanced Safety
In the realm of chemical plant operations, gas detection systems are pivotal in ensuring workplace safety and compliance with occupational health and safety standards. Equipped with ATEX Zone 1 certification, these devices are designed to perform in environments where a high risk of explosion exists due to the presence of flammable gases or vapors. The Intrinsically Safe Store offers a range of gas detection systems that serve as critical tools for continuous monitoring of hazardous gas levels, enabling rapid response to potential threats.
Key Features and Benefits
- Real-Time Monitoring: Our ATEX Zone 1 gas detection systems provide continuous surveillance of gas concentrations, offering real-time data that is essential for maintaining safety. This capability allows for immediate action to be taken before gas levels reach a dangerous threshold.
- Wide Range of Detectable Gases: The variety of gas detectors available through the Intrinsically Safe Store can identify a broad spectrum of flammable and toxic gases commonly found in chemical plants. This versatility ensures that workers are informed of the specific hazards present in their environment.
- Durable and Reliable: Designed to withstand the harsh conditions often present in hazardous areas, these devices are both durable and reliable. Their robust construction ensures that they continue to operate effectively, even in extreme temperatures, high humidity, or the presence of corrosive substances.
- Compliance with Safety Standards: Adherence to ATEX standards in the manufacturing of these gas detection systems guarantees that they meet the rigorous requirements for operation in Zone 1 areas. This compliance not only ensures the safety of personnel but also protects the organization from legal repercussions related to safety violations.
- Ease of Integration: Many of the gas detection systems offered are designed to seamlessly integrate into existing safety and monitoring infrastructure. This integration capability enables a holistic approach to safety management, allowing for centralized control and response strategies.
Implementing ATEX Zone 1 certified gas detection systems from the Intrinsically Safe Store enhances the safety infrastructure of chemical plants by providing reliable and continuous monitoring of hazardous gases. These systems are an essential component of a comprehensive safety strategy, ensuring that personnel can work in the safest possible conditions.
Challenges in Maintaining ATEX Zone 1 Equipment
Maintaining equipment in ATEX Zone 1 environments presents a unique set of challenges that industries in hazardous environments must navigate to ensure safety and compliance. ATEX Zone 1 refers to areas where an explosive atmosphere is likely to occur during normal operation. In such environments, the use of specialized equipment that can prevent ignition sources is crucial. However, the maintenance of these devices requires careful consideration and adherence to stringent regulations.
One of the primary challenges involves the complex nature of ATEX Zone 1 devices. These pieces of equipment are designed to limit the electrical and thermal energy they release, to prevent ignition of the flammable gases or vapors present in the atmosphere. This complexity means that routine maintenance and inspections must be carried out by highly trained personnel who understand the intricacies of the technologies involved.
Another challenge is ensuring that all maintenance activities comply with the latest ATEX directives and standards. These regulations are subject to change, and keeping up-to-date with the most current requirements is vital for maintaining compliance and ensuring the safety of plant personnel. Failure to comply can not only lead to catastrophic safety incidents but also result in significant fines and legal ramifications for the organization.
Environmental conditions in ATEX Zone 1 areas also add to the maintenance challenges. Exposure to aggressive chemicals, extreme temperatures, and the presence of dust and moisture can cause wear and tear on equipment. Regular inspection and replacement of damaged components are necessary to prevent equipment failure. However, the process of replacing parts or repairing equipment in these zones requires special precautions and sometimes necessitates temporary shutdowns of operations, leading to potential productivity losses.
The selection of suitable cleaning and maintenance materials poses yet another hurdle. Chemicals and cleaning agents must be carefully chosen to avoid reactions with the equipment or the atmospheric conditions of Zone 1 areas. The wrong selection can compromise the integrity of the safety devices and, worse still, trigger a hazardous event.
Finally, the challenges of documentation and record-keeping cannot be overstated. Detailed records of maintenance schedules, inspections, and repairs are mandatory under ATEX regulations. This documentation not only ensures compliance but is also essential for internal safety audits and when investigating incidents. It requires a systematic approach and meticulous attention to detail.
In conclusion, maintaining ATEX Zone 1 equipment within chemical plants involves navigating a complex landscape of technical, regulatory, and environmental challenges. Despite these difficulties, the commitment to maintaining these systems is a non-negotiable aspect of ensuring the safety and operational integrity of facilities in hazardous areas.
The Role of Personal Protection Equipment (PPE) in Zone 1
Personal Protection Equipment (PPE) plays a crucial role in maintaining safety within ATEX Zone 1 areas in chemical plants. In environments where the presence of an explosive atmosphere is likely to occur during regular operation, selecting the appropriate PPE is not just a regulatory compliance matter but a critical component of overall safety strategy.
ATEX Zone 1 is defined as an area where an explosive atmosphere, consisting of a mixture with air of dangerous substances in the form of gas, vapor, or mist, is likely to occur in normal operation occasionally. As such, the equipment and protective gear used in these zones must be rigorously tested and certified to ensure they are capable of operating safely without igniting the surrounding atmosphere.
Selection of PPE for ATEX Zone 1 Environments:
- Intrinsically Safe Flashlights and Headlamps: Lighting equipment used in Zone 1 must limit the electrical and thermal energy sufficiently to prevent ignition. Intrinsically safe flashlights and headlamps provide workers with the necessary illumination without compromising on safety.
- Handheld Computers and Communication Devices: Essential for data collection and communication, these devices must be designed to ensure that their operation does not provide a source of ignition. ATEX certified handhelds are critical for personnel who need to perform data logging, product scanning, or remote communication within a Zone 1 area.
- Gas Detectors: Given the high risk of explosive gas presence, having intrinsically safe gas detectors that can accurately and quickly identify hazardous gases is vital. These devices help in proactive safety management by alerting personnel to dangerous conditions before they escalate.
- Protective Clothing and Footwear: While not electronic in nature, clothing and footwear designed for use in explosive atmospheres are also considered part of PPE for ATEX Zone 1. These items are made from materials that reduce static build-up and are designed to provide protection from other industrial hazards, such as chemical splashes.
Each piece of PPE for Zone 1 areas not only fulfills a specific safety function but also adheres to stringent ATEX directives. Ensuring that all personnel are equipped with the right PPE is a responsibility that falls on the shoulders of the company’s safety officers and management. It requires an understanding of the unique hazards of their specific operations and the knowledge to select the equipment that best mitigates these risks.
The integration of certified ATEX Zone 1 devices within PPE strategies is an essential part of upholding safety protocols in chemical plants. These devices are designed to facilitate safe operating conditions, allowing workers to perform their tasks confidently and efficiently, even in the presence of potentially explosive atmospheres.
Case Studies: Success Stories in Chemical Plant Safety
The effectiveness of ATEX Zone 1 Devices in ensuring chemical plant safety is best illustrated through real-world applications. Two case studies highlight how incorporating these devices significantly mitigated risks and enhanced operational safety in hazardous environments.
Case Study 1: Advanced Gas Detection Systems
A leading petrochemical plant, facing challenges with its outdated gas detection system, decided to upgrade to a state-of-the-art ATEX Zone 1 certified gas detector. The previous system lacked the sensitivity required for early detection of hazardous gas leaks, posing a serious risk to plant safety and efficiency. The new gas detectors, equipped with real-time monitoring and higher sensitivity sensors, were installed throughout the plant’s critical areas.
Outcome: The upgrade to ATEX Zone 1 certified gas detectors led to a dramatic improvement in the plant’s ability to detect and respond to gas leaks early. This resulted in a significant reduction in the risk of gas-related incidents, contributing to a safer working environment for the employees and preventing potentially catastrophic outcomes. The plant also saw improvements in operational uptime, as the enhanced safety measures allowed for more consistent production processes.
Case Study 2: Explosion-Proof Lighting in High-Risk Areas
Another success story involves a pharmaceutical manufacturing facility that decided to replace its conventional lighting fixtures with ATEX Zone 1 certified explosion-proof lighting. The facility’s traditional lighting did not provide adequate safety measures for the explosive atmospheres present in certain production zones. Recognizing the need for improved safety and compliance, the facility initiated the upgrade, focusing on areas classified as having the highest risk of explosive gas atmospheres.
Outcome: By installing explosion-proof lighting, the pharmaceutical plant not only enhanced its compliance with safety regulations but also significantly improved visibility in critical working areas. This not only minimized the risk of accidents due to poor lighting but also facilitated safer operation and maintenance activities. Employees reported feeling safer and more confident in their work environment, while the company benefited from the peace of mind that their operations met the highest safety standards.
These case studies underscore the importance of selecting ATEX Zone 1 Devices for Chemical Plants meticulously. By choosing the right equipment, facilities operating in hazardous environments can ensure the safety of their operations and personnel, while also complying with rigorous international safety standards. The success stories presented here serve as a testament to the positive impact that such devices can have on enhancing overall safety in chemical plants.
FAQs: Navigating Safety with ATEX Zone 1 Devices in Chemical Plants
What kind of lighting solutions are available for ATEX Zone 1?
ATEX Zone 1 environments require lighting solutions that are designed to prevent the ignition of flammable gases or vapors. For these conditions, intrinsically safe and explosion-proof lighting options are available, including LED flashlights, headlamps, and fixed lighting systems. These lighting solutions are engineered to limit electrical and thermal energy, ensuring they can safely illuminate hazardous areas without risking a fire or explosion.
How are portable devices managed in ATEX Zone 1 areas?
Portable devices for use in ATEX Zone 1 areas, such as handheld computers, gas detectors, and communication devices, are specifically designed to prevent the ignition of hazardous atmosphere. They are manufactured to reduce the risk of sparking and limit the temperature of the device surfaces. Managing these devices includes regular inspection, maintenance, and adherence to manufacturer guidelines for charging and use within the designated hazardous areas.
What are the costs associated with implementing ATEX Zone 1 devices?
The costs of ATEX Zone 1 devices can vary significantly depending on the type, specifications, and quantity of equipment required. While these devices are typically more expensive than non-rated equipment due to their specialized design and rigorous testing for safety certifications, investing in such equipment is essential for ensuring workplace safety in hazardous environments. Additionally, the long-term benefits of preventing accidents and ensuring compliance with safety regulations often outweigh the initial costs.
How does explosion-proof certification relate to ATEX Zone 1 device selection?
Explosion-proof certification is a critical factor in selecting devices for ATEX Zone 1 areas. This certification ensures that the equipment has been tested and approved to prevent internal sparks or explosions from igniting flammable gases or vapors in the surrounding environment. When selecting devices, it is essential to look for ATEX certification (in Europe) or other relevant standards, which indicate compliance with safety requirements for hazardous areas. Devices should meet or exceed the specific needs of the Zone 1 classification to ensure workplace safety.
What training is required for personnel working with ATEX Zone 1 devices?
Personnel working with ATEX Zone 1 devices must undergo comprehensive training to understand the risks associated with operating in hazardous areas and the safe handling of intrinsically safe and explosion-proof equipment. Training should cover the principles of explosive atmospheres, the correct usage of ATEX Zone 1 devices, emergency procedures, and routine maintenance and inspection protocols. Ensuring that all employees are well-informed and competent in handling these devices is crucial for maintaining a safe working environment in chemical plants and similar hazardous areas.
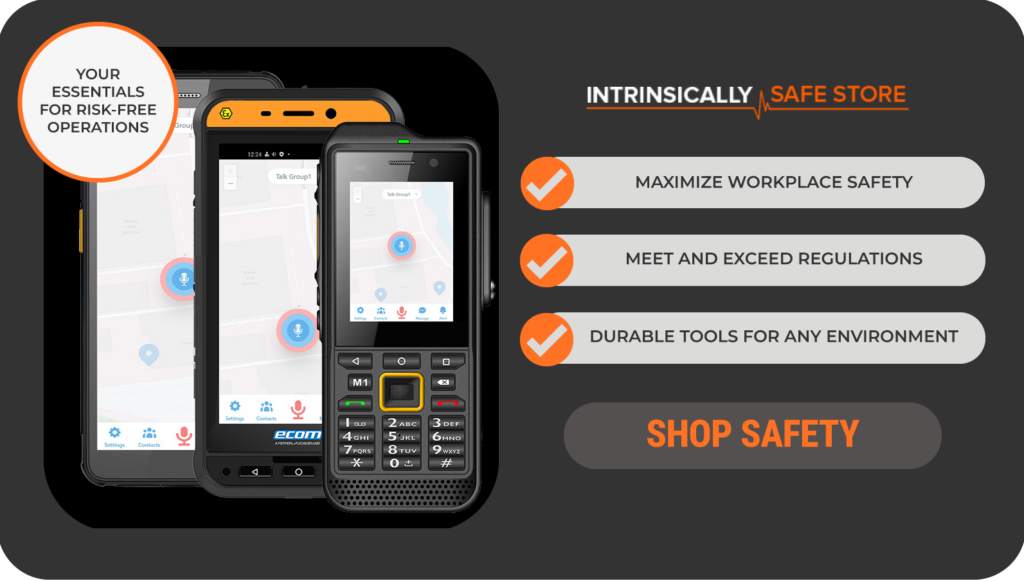