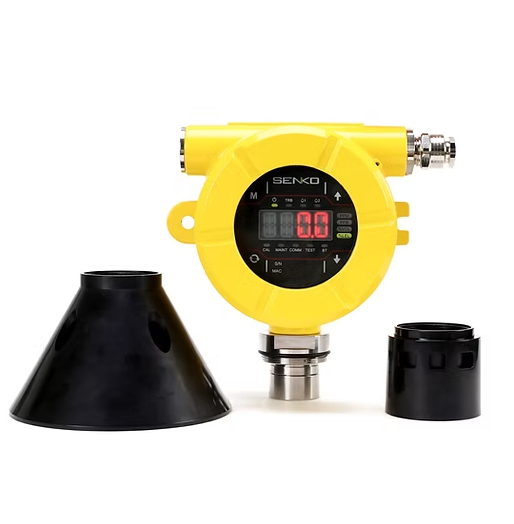
The Importance of Calibrating Intrinsically Safe Gas Detectors
Intrinsically safe gas detectors are critical for monitoring hazardous gases in environments where ignition risks exist. These devices ensure worker safety by detecting dangerous levels of flammable and toxic gases before they become a threat.
However, without regular calibration, even the most advanced gas detectors can produce inaccurate readings, leading to false alarms or missed gas leaks. This article provides a step-by-step guide on how to calibrate your intrinsically safe gas detector to maintain its accuracy and reliability.
Why Calibration is Essential
What Happens If a Gas Detector is Not Calibrated?
Over time, gas detectors experience sensor drift, meaning their readings may deviate from actual gas concentrations. This can happen due to:
- Sensor aging
- Exposure to contaminants (moisture, dirt, chemicals)
- Temperature and humidity changes
- Frequent exposure to high gas concentrations
Failing to calibrate regularly can lead to false positives (causing unnecessary evacuations) or false negatives (missing actual hazards), both of which can be dangerous.
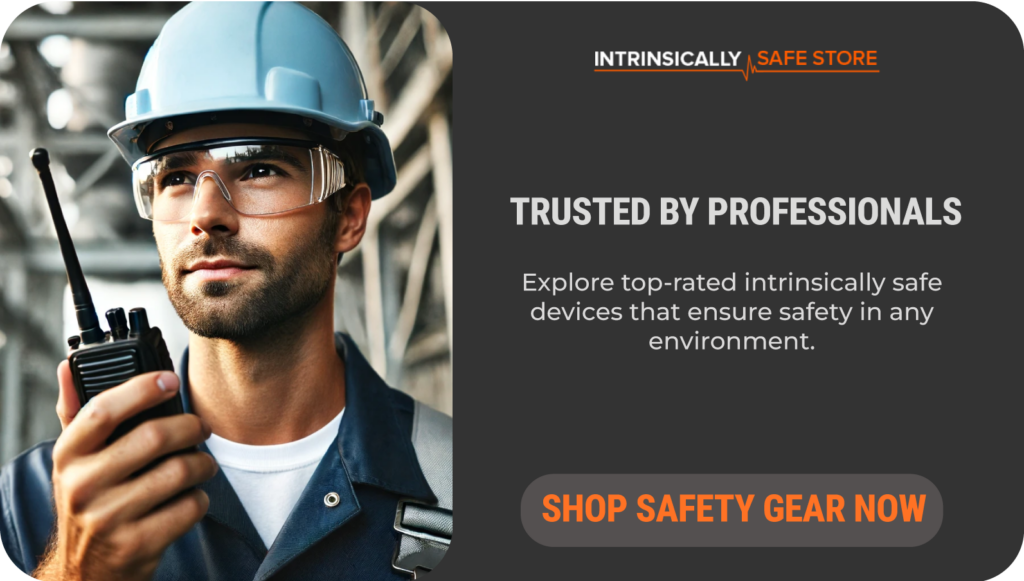
Calibration Frequency Guidelines
The frequency of calibration depends on the manufacturer’s recommendations, industry regulations, and the environmental conditions in which the gas detector operates.
- Bump Test (Functional Check): Recommended daily or before each use.
- Full Calibration: Typically required every 30 to 90 days, but high-risk environments may require more frequent calibration.
- Sensor Replacement: If calibration adjustments exceed manufacturer limits, the sensor may need to be replaced.
Regulatory Compliance:
Ensure calibration follows industry standards, such as:
- OSHA (Occupational Safety and Health Administration)
- NIOSH (National Institute for Occupational Safety and Health)
- IECEx / ATEX (for international hazardous location certification)
Step-by-Step Calibration Process
1. Preparation
Equipment Needed:
- Calibration gas cylinder (with a known concentration of the target gas)
- Zero gas (pure air or nitrogen)
- Regulator and tubing (to control gas flow)
- Calibration cap (for directing gas to the sensor)
- Gas detector manufacturer’s manual
Safety Precautions:
- Perform calibration in a well-ventilated area.
- Wear appropriate personal protective equipment (PPE).
- Ensure all equipment is intrinsically safe and meets hazardous location standards.
2. Zero Calibration (Baseline Adjustment)
Before testing the sensor’s response to gas, the detector must be calibrated to a known zero gas to ensure accuracy.
Procedure:
- Attach the zero gas cylinder to the detector’s calibration port using the tubing and regulator.
- Turn on the gas detector and enter the calibration mode (refer to the user manual for your model).
- Open the gas flow and allow the sensor to stabilize (typically 30–60 seconds).
- Adjust the detector to read “0 ppm” (zero point adjustment).
- Turn off the gas and disconnect the tubing.
If the detector does not stabilize at zero, the sensor may need cleaning or replacement.
3. Span Calibration (Adjusting Sensitivity)
This step ensures the detector reads the correct gas concentration when exposed to a known test gas.
Procedure:
- Connect the calibration gas cylinder containing the target gas to the detector.
- Initiate span calibration mode on the gas detector.
- Open the regulator and allow the calibration gas to flow.
- Monitor the gas detector reading – it should match the gas concentration on the cylinder.
- If necessary, adjust the detector’s response using the span calibration function.
- Once stabilized, turn off the gas and disconnect the equipment.
If the reading does not stabilize at the expected value, the sensor may need recalibration or replacement.
4. Post-Calibration Checks
After calibration, perform a functional bump test to confirm the detector responds correctly to gas exposure.
- Expose the sensor to a test gas briefly and check if the alarm triggers.
- If the detector does not respond correctly, repeat calibration or inspect the device for faults.
Finally, log the calibration details in maintenance records, including:
- Date of calibration
- Gas concentration used
- Adjustments made
- Next scheduled calibration date
Ensuring Safety with Proper Calibration
Regular calibration of your intrinsically safe gas detector is essential for workplace safety and regulatory compliance. By following manufacturer guidelines and industry best practices, you can maintain accurate gas detection and protect workers from hazardous gases.
Need intrinsically safe calibration gas or gas detectors? Visit Intrinsically Safe Store to explore certified safety solutions!
Have questions? Contact our experts for guidance on selecting and maintaining gas detection equipment.
Common Calibration Issues and Solutions
Issue | Cause | Solution |
---|---|---|
Detector won’t zero | Sensor contamination | Clean or replace the sensor |
Incorrect gas readings | Sensor drift | Perform full calibration |
Slow response time | Aging sensor | Replace the sensor |
Detector fails bump test | Calibration gas expired | Use fresh calibration gas |
Best Practices for Maintaining Calibration Accuracy
- Use certified calibration gas: Expired or contaminated gas can lead to incorrect adjustments.
- Store gas cylinders properly: Keep in a cool, dry place to maintain accuracy.
- Follow a strict calibration schedule: Set reminders for routine calibration.
- Keep detailed calibration logs: For compliance and troubleshooting.
FAQs: Calibrating an Intrinsically Safe Gas Detector
What is the difference between a bump test and a full calibration?
- Bump Test: A quick test to confirm the detector responds correctly to gas.
- Full Calibration: Adjusts the sensor to ensure accurate readings.
How do I know if my gas detector needs recalibration?
- If it fails a bump test.
- If gas readings drift outside acceptable limits.
- If the detector frequently alarms incorrectly.
Can I calibrate my gas detector in a hazardous environment?
- No, calibration should be done in a controlled, non-hazardous area unless using an intrinsically safe calibration station.
What gases require regular calibration?
- Methane (CH4), Carbon Monoxide (CO), Hydrogen Sulfide (H2S), Oxygen (O2), VOCs.
How long does a gas detector sensor last?
- 2–5 years, depending on usage and environmental conditions.
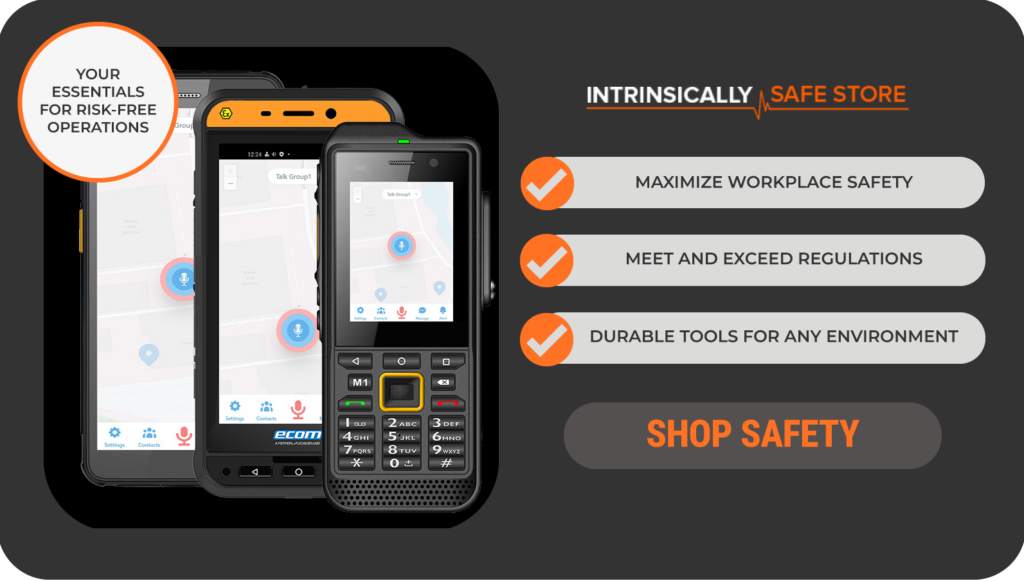