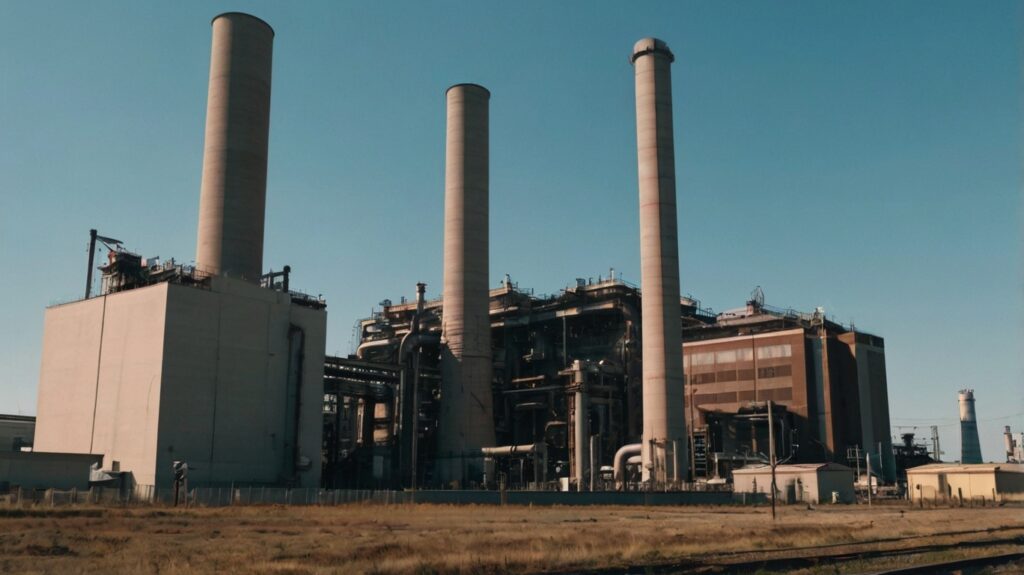
Definition: Intrinsically safe and explosion-proof are two distinct methods used to ensure the safe operation of electrical equipment in hazardous environments, such as those containing flammable gases, vapors, or dust.
Key Differences:
- Intrinsically Safe:
- Designed to prevent the equipment itself from causing an explosion. This is achieved by limiting both thermal and electrical energy to levels that cannot ignite the surrounding hazardous atmosphere. Intrinsically safe devices use techniques such as current limiting resistors, fuses, and low-voltage circuits (e.g., 24V) to minimize the risk of sparking or heat buildup.
- These devices are typically lighter, less bulky, and easier to maintain, making them suitable for both permanent and portable installations.
- Explosion-Proof:
- Designed to contain an explosion within the equipment if it were to occur. Explosion-proof devices are housed in robust enclosures, often made of materials like cast aluminum or stainless steel, which can withstand and contain an internal explosion. This prevents the explosion from spreading to the surrounding environment.
- These devices are heavier, bulkier, and more complex to install, making them better suited for permanent installations where higher power requirements are necessary.
Science Behind It: The science behind these methods involves understanding the combustion triangle (ignition source, oxidizer, and fuel) and either preventing the ignition source (intrinsically safe) or containing the explosion if it occurs (explosion-proof). Intrinsically safe devices focus on limiting energy levels to non-ignitable thresholds, while explosion-proof devices rely on robust enclosures to prevent the spread of an explosion.
Examples in Action:
- Intrinsically Safe: Portable measurement equipment, sensors, and actuators in chemical plants or oil refineries where the risk of flammable gases is high.
- Explosion-Proof: Electrical enclosures in permanent installations such as manufacturing facilities or power plants where higher power equipment is necessary.
Fun Fact: Intrinsically safe devices allow for maintenance and troubleshooting without shutting down the plant, as they can be safely opened or replaced in potentially explosive areas. This versatility makes them highly valuable in hazardous environments.
- Intrinsically safe devices prioritize prevention by limiting energy to prevent ignition, while explosion-proof devices focus on containing any potential explosion within the device.
- The classification of hazardous areas, such as Zones or Divisions, dictates the type of safety equipment required, guiding the decision between intrinsically safe and explosion-proof alternatives.
- Proper installation and certification of intrinsically safe and explosion-proof devices are crucial for maintaining safety and compliance in hazardous environments, reflecting their distinct design philosophies and operational requirements.
Understanding Intrinsically Safe Devices
When navigating the realm of safety equipment for hazardous environments, understanding the concept of intrinsically safe devices is crucial. These are specifically designed to ensure that even in the event of a fault, they will not cause an ignition of a flammable atmosphere. This core principle sets them apart, offering a unique advantage in maintaining safety standards in highly volatile areas.
Intrinsically safe devices achieve this through careful design and engineering, which limits electrical and thermal energy to levels below those that can ignite specific hazardous atmospheric mixtures. This involves the use of components that draw and store minimal power, alongside circuit designs that minimize the risk of sparks or high temperatures. Importantly, these devices are not merely about preventing ignition from their own power sources but also from any external factors that could result in hazardous scenarios.
To be certified as intrinsically safe, devices must undergo rigorous testing and meet strict standards set forth by recognized safety organizations. These certifications ensure that the devices are suitable for use in environments classified according to the type of explosive atmosphere they may encounter (such as gases, vapors, dust, or fibers). It is critical that organizations operating in hazardous environments select appropriately certified devices to ensure the safety and compliance of their operations.
In practice, intrinsically safe devices are employed in a variety of settings, from oil and gas production sites to chemical manufacturing plants. They include a wide range of equipment, such as natural gas detectors, communication devices, and even specialized computing equipment like intrinsically safe iPad cases. The primary goal of using such devices is to allow for safe operations within explosive or flammable environments without sacrificing functionality or communication capabilities.
Choosing intrinsically safe devices is a testament to an organization’s commitment to maintaining the highest safety standards while ensuring that their operations can proceed efficiently and without interruption. By integrating intrinsically safe equipment into their safety protocols, companies in hazardous industries can protect their employees, assets, and the environment from the risks associated with potential explosions or fires.
Find Your Intrinsically Safe Solution Today
Navigating the world of safety in hazardous environments can seem daunting, but ensuring the use of the right equipment is paramount to maintaining a safe workspace. Understanding the difference between intrinsically safe and explosion-proof devices is just the beginning. At the Intrinsically Safe Store, we’re committed to bridging the gap between complexity and safety compliance, offering a myriad of certified safe solutions conducive to a range of industries, including oil and gas, chemical plants, and more.
Why choose the Intrinsically Safe Store?
- Expertise: Leverage our deep understanding of safety requirements to find the perfect fit for your needs.
- Wide Range of Products: From iPad cases to natural gas detectors, explore our extensive selection of safety equipment.
- Speedy Delivery: Benefit from our free 2-8 day delivery service for a swift, seamless shopping experience.
- Data Privacy: Shop with confidence knowing your data is protected through our robust privacy policy.
Taking the right step towards enhancing safety in hazardous environments has never been easier. Contact the Intrinsically Safe Store today through our online chat or phone and start a conversation about your safety needs. Together, we can connect your team with a billion certified safe solutions to improve our world.
The Fundamentals of Explosion-Proof Devices
When discussing the difference between intrinsically safe and explosion-proof devices, it is crucial to understand the fundamentals of how explosion-proof technology operates. Explosion-proof devices are designed with the primary goal of containing an explosion within the device itself, preventing the ignition of hazardous materials present in the surrounding atmosphere. This design principle is fundamentally different from that of intrinsically safe devices, which are designed to prevent the generation of sufficient energy to cause an explosion in the first place.
Explosion-proof devices achieve their protective capabilities through a robust, heavy construction. They are typically encased in strong, durable materials that can withstand an internal explosion without cracking or deforming. The enclosures of these devices are built to contain any flames or sparks that might be generated within, thereby preventing those ignition sources from coming into contact with flammable gases or dust in the environment. This method allows the use of standard electrical components and circuits within the protected enclosure, as the containment strategy does not rely on limiting the electrical energy entering the device.
Furthermore, the construction of explosion-proof enclosures involves precise engineering to manage the aftermath of an internal explosion. Interfaces such as joints or flanges between the enclosure sections are specially designed to quench flames by cooling the hot gases as they are forced through narrow pathways, stopping the propagation of an external explosion.
One critical aspect of explosion-proof device maintenance is the integrity of its enclosure. Regular inspections are vital to ensure that the seals and surfaces remain intact, without cracks or gaps that could compromise the device’s ability to contain an explosion. Such precautions are necessary to maintain the safety and compliance of explosion-proof devices in hazardous environments.
In summary, explosion-proof devices provide safety by containing and isolating explosions within their enclosures, preventing the ignition of external hazardous atmospheres. Their construction and maintenance are paramount to their effectiveness, embodying a protective approach that contrasts with the preventive strategy of intrinsically safe devices. This robust and heavy-duty methodology enables their use in many industrial settings where hazardous materials are present, ensuring operations can continue with an added layer of safety.
Design Philosophies: Intrinsically Safe vs. Explosion-Proof
The core difference between intrinsically safe and explosion-proof devices lies in their design philosophies—how they achieve safety in hazardous environments. Understanding these design principles is fundamental for professionals and organizations operating in sectors such as the oil and gas industry and chemical plants, ensuring they choose the right equipment for their specific needs.
Intrinsically Safe Devices
The design philosophy of intrinsically safe devices centers around prevention. Instead of trying to contain an explosion should one occur, these devices are engineered to prevent the release of enough energy to ignite a hazardous atmosphere. This is achieved by limiting the electrical and thermal energy available for ignition, ensuring that even in the event of a fault, the device cannot cause an explosion. Intrinsically safe devices are often used in highly volatile environments where the presence of flammable gases or vapors presents a significant risk.
Key benefits of intrinsically safe devices include:
- Safety: By reducing the risk of ignition, these devices offer unparalleled safety in hazardous areas.
- Flexibility: They can be used in close proximity to the dangerous substances.
- Cost-Effectiveness: Lower installation and maintenance costs due to the absence of expensive explosion-proof enclosures.
Explosion-Proof Devices
Contrastingly, explosion-proof devices adopt a containment strategy. These devices are designed to withstand an internal explosion without allowing it to escape and ignite the external atmosphere. The construction of explosion-proof equipment is robust, featuring thick walls made from materials like steel or aluminum. If any explosive gas does get ignited within the device, the unit is built to contain the explosion and prevent it from causing a larger, external blast.
Advantages of explosion-proof devices include:
- Durability: Their rugged design makes them suitable for demanding environments.
- Versatility: They can handle higher power applications that intrinsically safe devices cannot.
- Compliance: Meets stringent safety standards and can be used in a variety of hazardous locations.
In choosing between intrinsically safe and explosion-proof devices, it’s essential to consider the specific characteristics of the hazardous environment and the nature of the work being performed. Each approach to safety has its merits, and the decision should be guided by a thorough risk assessment, considering both the immediate needs and the long-term safety protocols of the operation.
Remember, the goal is to provide the highest level of safety while ensuring compliance and productivity in hazardous work environments. Whether your operation benefits more from the preventive approach of intrinsically safe devices or the robust containment offered by explosion-proof solutions, staying informed about the different design philosophies helps in making the right equipment choice.
The Principles of Hazardous Area Classification
When discussing the difference between intrinsically safe and explosion-proof devices, it’s crucial to first understand the principles of hazardous area classification. This classification defines areas where flammable gases, vapors, liquids, or combustible dust may be present and pose a potential explosion or fire hazard. These classifications help dictate the type of safety equipment that is necessary to use within these zones, guiding the selection between intrinsically safe and explosion-proof devices.
Zone Classification
Hazardous areas are categorized into zones based on the frequency and duration of the explosive atmosphere’s presence.
- Zone 0 (Gas)/20 (Dust): These areas have an atmosphere that contains flammable materials continuously, frequently, or for long periods.
- Zone 1 (Gas)/21 (Dust): In these zones, flammable materials are likely to be present during routine operations.
- Zone 2 (Gas)/22 (Dust): Areas classified under Zone 2/22 have a flammable atmosphere only occasionally and for a short period.
Division Classification
Primarily used in North America, this classification system divides hazardous areas into two main divisions:
- Division 1: Where explosive or ignitable materials are continuously, intermittently, or periodically present during normal operations.
- Division 2: Where flammable materials are handled, processed, or used but are normally contained or present only in abnormal conditions.
Temperature Class and Protection Techniques
Alongside zone and division classifications, hazardous areas are also defined by the maximum surface temperature of equipment and devices, denoted by a “T” rating. This helps ensure that the temperature of the device does not exceed the ignition temperature of the hazardous substance present.
Safety in these zones is achieved through various protection techniques applicable to both intrinsically safe and explosion-proof devices. However, the choice between the two often depends on the specific classification of the hazardous area and the nature of the potential explosive atmosphere.
Understanding these classifications and principles is necessary for ensuring the safety and compliance of equipment used in hazardous areas. It informs professionals and organizations about the essential criteria for selecting safely designed and certified devices, aligning with our mission at The Intrinsically Safe Store to connect you with a vast array of certified safe solutions tailored for these demanding environments.
Materials and Construction: A Comparative Look
When comparing intrinsically safe and explosion-proof devices, it’s essential to delve into the materials and construction approaches unique to each type. This comparison not only highlights the difference between intrinsically safe and explosion-proof devices but also underscores the importance of choosing the right equipment for specific hazardous environments.
Intrinsically Safe Devices
Intrinsically safe devices are designed to limit electrical and thermal energy to levels below those that might ignite a specific hazardous atmospheric mixture. To achieve this, they often incorporate materials that are lightweight yet robust enough to minimize any risk of spark or excessive heat generation. This might include the use of special circuitry that controls the flow of electrical current, materials that dissipate heat efficiently, and components that are carefully selected to prevent the initiation of an explosive atmosphere.
The construction of intrinsically safe devices focuses on preventing an internal or external explosion by ensuring that the device cannot release sufficient energy to ignite surrounding gases, vapors, or dust. This is achieved not through heavy-duty casings but through meticulous design that emphasizes control and limitation of power. The certification process for these devices ensures that they meet stringent safety standards applicable to hazardous locations, making them a reliable choice for environments where traditional electronic devices would pose a significant risk.
Explosion-Proof Devices
Explosion-proof devices, on the other hand, are designed to contain any explosion that originates within its housing and to prevent ignitions outside the device from sparking an internal explosion. These devices are typically made from heavy-duty materials such as cast aluminum or stainless steel to withstand extreme conditions. The construction is robust, featuring thick walls and tight seals to ensure that any explosion is contained within the device itself.
The design philosophy here is fundamentally different from that of intrinsically safe devices. Instead of limiting the energy to prevent an explosion, explosion-proof devices are built to endure and contain it. This approach allows them to operate safely even in direct contact with flammable materials or in highly volatile environments. These devices are often larger and heavier due to the need for reinforced construction and materials meant to withstand and contain high-pressure explosions.
Choosing the Right Equipment
The decision between using intrinsically safe and explosion-proof devices ultimately depends on the specific requirements of the hazardous environment in question. Intrinsically safe devices are favored for their lighter, more manageable construction and their ability to prevent explosions by controlling the energy emission at the source. Explosion-proof devices, with their rugged construction, are suited for environments where the presence of hazardous gases or dust cannot be mitigated to levels safe for intrinsically safe devices.
Understanding the materials and construction of these devices is crucial for professionals operating in hazardous environments. It allows for informed decision-making that ensures both safety and efficiency in operations, aligning with our commitment at The Intrinsically Safe Store to connect people with certified safe solutions to improve our world.
Differences in Installation Procedures
When evaluating the difference between intrinsically safe and explosion-proof devices, it’s crucial to consider the contrasting installation procedures for each. These procedures play a significant role in ensuring safety in hazardous environments, reflecting a commitment to preventing accidents and enhancing operational efficiency.
Intrinsically Safe Devices
Intrinsically safe devices are designed to limit electrical and thermal energy to levels below those that can ignite a specific hazardous atmospheric mixture. The installation of these devices is typically more straightforward than their explosion-proof counterparts due to their lower energy usage. Installation procedures for intrinsically safe devices require careful consideration of the entire system, including cables, barriers, and other components certified as intrinsically safe. It’s crucial that all parts of the system are compatible and properly certified to maintain the intrinsic safety of the setup. These devices often necessitate detailed documentation and certifications that prove their safe use in hazardous locations. The focus is on preventing the generation of sparks or heat that could cause an ignition.
Explosion-Proof Devices
On the other hand, explosion-proof devices are engineered to contain an explosion within the device itself, should an ignition occur. This design principle requires these devices to be constructed with robust, heavy materials capable of withstanding an internal explosion without compromising their structural integrity. The installation of explosion-proof devices is generally more labor-intensive and requires specific precautions to ensure the device’s enclosure is not compromised. This includes meticulous inspection of the enclosure seals and the integrity of the device after installation. Due to the bulky nature of explosion-proof enclosures, the location and accessibility for maintenance and inspection can pose additional challenges. It’s also important to note that explosion-proof devices must be used in conjunction with properly rated conduit systems and fittings to maintain their explosion-proof rating.
Considerations for Compliance and Safety
Both installation processes demand a high level of expertise and knowledge of the relevant safety standards and regulations. Professionals undertaking these procedures must be trained and certified to work in hazardous environments. Compliance with national and international safety standards, such as the NEC (National Electrical Code) in the United States and ATEX directives in Europe, is mandatory to ensure the safety and efficacy of both intrinsically safe and explosion-proof installations.
It’s evident that the choice between intrinsically safe and explosion-proof devices extends beyond their operational capabilities. The installation procedures themselves reflect the devices’ underlying safety philosophies and the lengths to which industries must go to safeguard against the risks present in hazardous environments. For organizations operating in these sectors, understanding the detailed nuances of each approach is essential to selecting the right equipment for their specific needs, ensuring not only regulatory compliance but the safety of their operations and personnel.
FAQs: Understanding the Nuances of Intrinsically Safe and Explosion-Proof Devices
Can a device be both intrinsically safe and explosion-proof?
No, a device cannot be both intrinsically safe and explosion-proof. Intrinsically safe devices are designed to limit the energy, electrical and thermal, to a level below what is required to ignite a specific hazardous atmospheric mixture. In contrast, explosion-proof devices are designed to contain an explosion within the device itself, preventing the ignition of the surrounding atmosphere. The principles behind each design philosophy are fundamentally different, serving unique safety approaches in hazardous environments.
What certifications apply to explosion-proof devices?
Explosion-proof devices are typically certified by recognized testing labs and adhere to standards such as ATEX and IECEx in Europe, and UL in North America. These certifications ensure that the devices meet stringent requirements for construction and performance, allowing them to contain an internal explosion without igniting the external environment. Each geographic region may have its preferred or legally mandated certification standards, making it crucial for operators to be aware of the requirements specific to their location.
Are intrinsically safe devices repairable in hazardous areas?
Yes, intrinsically safe devices are designed to be safe for use and, in some cases, repairable in hazardous areas. Because these devices do not store enough energy to ignite a hazardous atmosphere, certain repairs and maintenance activities can be safely performed without removing the equipment from the hazardous location. However, it is crucial that any repairs are done following the manufacturer’s guidelines and any applicable workplace safety regulations to maintain the intrinsic safety certifications.
Can explosion-proof devices be opened in hazardous locations?
No, explosion-proof devices cannot be safely opened while in hazardous locations. Opening an explosion-proof device in a hazardous area compromises its integrity to contain an explosion and may expose the internal components to the external atmosphere, creating a risk of ignition. Maintenance, repair, or inspection that requires opening these devices should be carried out in a safe, non-hazardous environment to ensure safety.
How do maintenance requirements differ for intrinsically safe vs explosion-proof devices?
Maintenance requirements for intrinsically safe and explosion-proof devices differ significantly due to their design philosophies. Intrinsically safe devices typically allow for easier maintenance and inspection in hazardous areas, as they do not pose a risk of igniting the atmosphere. Conversely, explosion-proof devices, due to their design to contain explosions, often require more stringent maintenance protocols. This may involve regular inspection and maintenance to be conducted in safe environments to ensure their housings and seals remain intact. As each type of device serves different safety functions, the manufacturer’s maintenance guidelines and local safety regulations should always be followed to ensure continued compliance and safety.