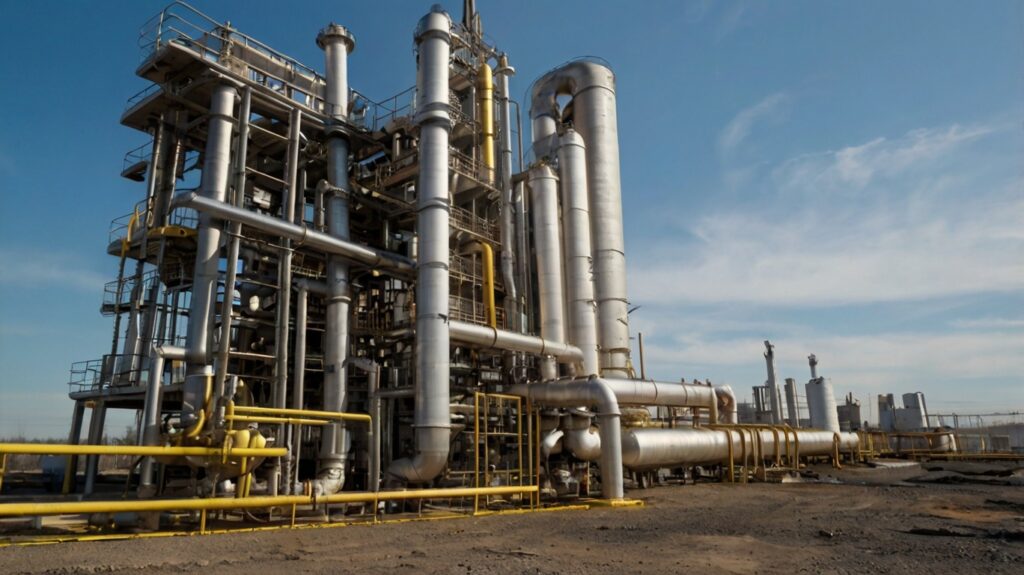
Definition: Choosing intrinsically safe devices involves selecting equipment that is specifically designed to prevent the ignition of flammable or combustible materials in hazardous environments. This ensures that the devices operate at energy levels that are incapable of causing an explosion, even under fault conditions.
Key Considerations:
Understand Your Environment’s Specific Hazards
Identify the types of gases, vapors, or particles present in your environment, their concentrations, and the zones or areas where explosive atmospheres may occur. This knowledge helps in matching equipment that is certified for use in those specific conditions.
Choose Certified and Approved Equipment
Ensure the equipment has undergone rigorous testing and certification by recognized bodies such as ATEX (Europe), IECEx (International), or UL (United States). These certifications guarantee that the equipment meets strict safety standards and can operate safely in hazardous environments.
Prioritize Compatibility and Integration
Select equipment that is compatible with your existing systems and can be easily integrated into your operations. This ensures a smooth implementation and enhances the overall safety and efficiency of your workflow. Incompatibilities can lead to operational disruptions or gaps in safety protocols.
Opt for Equipment with Robust Features and Reliability
Choose devices that are durable and reliable, with features such as impact resistance, waterproofing, and long battery life. Consider the manufacturer’s reputation for quality and after-sales support to ensure ongoing safety and performance.
Ensure Low Energy Signaling and Fault Tolerance
Intrinsically safe devices must operate with low energy levels and be evaluated under both normal and fault conditions to ensure they cannot cause ignition. This includes controlling component temperatures and eliminating internal sparking.
Use Barrier Devices and Intrinsically Safe Cases
Utilize barrier devices to limit the amount of energy that can enter the hazardous area and consider intrinsically safe cases for portable devices to control their power levels and prevent the release of sufficient energy to cause ignition.
Best Practices:
- Live Maintenance: Intrinsically safe systems often allow for live maintenance and troubleshooting within hazardous areas without the need to shut down the equipment or obtain special permits.
- Simplified Circuitry: Opt for devices with simplified circuitry that reduce the risk of ignition and make maintenance easier.
Importance: Selecting the right intrinsically safe devices is crucial for ensuring safety and compliance in hazardous environments. Incorrect choices can introduce new risks, while the right equipment can significantly reduce the risk of explosions and ensure a safe working environment.
- The utilization of intrinsically safe equipment is essential for preventing potential explosions and ensuring the safety of workers in hazardous environments such as petrochemical and mining sectors.
- Understanding the specific types of hazardous environments and selecting the appropriate intrinsically safe devices based on certifications and operational requirements is crucial in reducing explosion risks.
- Distinguishing between intrinsically safe and explosion-proof equipment involves considering factors like cost-effectiveness, flexibility, safety prevention strategies, and specific regulatory compliance needs, ensuring optimal safety in explosive atmospheres.
The Importance of Equipment Safety in Hazardous Environments
In hazardous environments, where the risk of explosions is ever-present, the safety of personnel and the integrity of operations hinge on the use of appropriately certified safety equipment. The selection of intrinsically safe devices is not just a regulatory compliance issue; it is a fundamental component of a comprehensive risk management strategy. Ensuring the safety of workers in sectors such as petrochemical, mining, and others prone to explosive atmospheres necessitates a thorough understanding of the nature of hazards these environments present and the protective measures available.
Intrinsically safe equipment is designed to operate in explosive atmospheres without igniting flammable gases, vapors, or dust. These devices are engineered to limit the energy, electrical and thermal, available for ignition. The significance of using such equipment cannot be overstated, as it directly correlates with the prevention of potentially catastrophic explosions that could lead to loss of life, significant property damage, and environmental harm.
Moreover, the utilization of equipment that complies with recognized safety standards, such as ATEX in Europe and HAZLOC in North America, is crucial. These certifications assure that the equipment has been tested and meets stringent safety requirements, providing an additional layer of reliability and peace of mind for businesses operating in such volatile environments.
Selecting the right intrinsically safe equipment entails a deep understanding of the specific hazards of an environment and the operational requirements of the equipment. It is not only about preventing ignition but also ensuring that the equipment can perform its intended function effectively under challenging conditions. This dual requirement of safety and functionality underscores the need for sourcing equipment from trusted suppliers, like the Intrinsically Safe Store, which specializes in providing high-quality, certified intrinsically safe and explosion-proof products.
For professionals and organizations operating in hazardous environments, prioritizing equipment safety is essential. It is an integral part of safeguarding workers, preserving assets, and maintaining operational continuity in industries where risks are inherent. Thus, embracing the best practices in selecting intrinsically safe devices is not merely a precaution; it is a critical investment in the future viability and safety of any operation within such challenging and hazardous settings.
Take Action for Safety Now
Finding the right intrinsically safe equipment for your hazardous environment is critical to ensuring the safety of your team and operations. The Intrinsically Safe Store is your dedicated partner in navigating these complex requirements with a comprehensive range of certified safety devices. Here’s why you should choose us for your safety needs:
- Expert Guidance: Our team of experts is always ready to help you select the best products for your specific needs, ensuring you have the right tools to maintain a safe working environment.
- Certified Safety: With products certified and compliant with ATEX and HAZLOC standards, you can trust that every device we offer meets the rigorous safety requirements of your industry.
- Wide Product Range: From intrinsically safe cameras and LED work lights to explosion-proof enclosures, we provide a diverse array of devices to cover all your safety needs in hazardous locations.
- Tailored for Your Industry: Our products cater to the specialized needs of the petrochemical, mining, and other sectors where explosive atmospheres present a significant risk.
Don’t compromise on safety. Visit the Intrinsically Safe Store today to explore our high-quality, intrinsically safe and explosion-proof products designed to prevent explosions and protect your team in hazardous environments.
Your safety is our priority. Make the right choice with the Intrinsically Safe Store.
Types of Hazardous Environments and Associated Risks
When selecting the right intrinsically safe equipment for your operations, understanding the various types of hazardous environments and their associated risks is crucial. Hazardous environments are categorized based on the nature and concentration of flammable gases, vapors, dust, or fibers present, which could potentially lead to explosive or fire hazards. These categories help in determining the specific requirements for intrinsically safe devices in various settings.
Class I: Gases and Vapors
Class I hazardous environments are areas where flammable gases or vapors are present under normal operating conditions. These are commonly found in industries such as petrochemical, chemical manufacturing, and gasoline storage or dispensing. The primary risk in these environments is the potential for an explosive atmosphere to form if the concentration of gases or vapors reaches a certain level. Therefore, equipment used in these areas must be designed to prevent the ignition of these gases or vapors.
Class II: Dust
Class II locations are characterized by the presence of combustible dust. Industries such as agriculture, wood processing, metalworking, and pharmaceuticals often have areas where fine particles accumulate, creating the risk of fire or explosion. Dust can be just as hazardous as gases and vapors because of its ability to ignite and cause a rapid fire or explosion. Intrinsically safe devices for Class II environments need to minimize the risk of igniting this dust.
Class III: Fibers and Flyings
Class III hazardous environments are marked by the presence of easily ignitable fibers or flyings, which are not typically suspended in the air but can collect around machinery and equipment. Textile mills, cotton processing plants, and woodworking facilities are prime examples of Class III locations. While these materials may not form an explosive atmosphere as gases or vapors do, they can ignite and fuel a fire. Equipment in such environments is designed to prevent the ignition of these fibers.
Zone Classification
In addition to the Class system used primarily in North America, the international community often refers to hazardous areas in terms of Zones. This classification considers how often and for how long an explosive atmosphere is present. Zones 0, 1, and 2 are used for gases, vapors, and mists, while Zones 20, 21, and 22 apply to dusts. This zoning helps further specify the appropriate intrinsically safe equipment needed based on the likelihood of explosive conditions.
Understanding the Risks
The inherent risks in these environments stem from the potential of a spark or excessive heat igniting flammable substances, leading to fires or explosions. These incidents can cause devastating injury, property loss, and environmental damage. Therefore, the selection of intrinsically safe devices is not merely a compliance issue but a critical component of maintaining safety and preventing disaster in hazardous environments. The Intrinsically Safe Store specializes in providing equipment that meets the strict safety standards required for each class and zone, ensuring your operations are equipped with the right tools to maintain safety and compliance.
Principles of Intrinsically Safe Design
When selecting the right intrinsically safe equipment for hazardous environments, understanding the underlying principles of intrinsically safe design is crucial. Intrinsically safe devices are engineered to operate safely in explosive atmospheres by limiting the energy, electrical and thermal, available for ignition. Here are the core principles that guide the design and selection of such devices:
Energy Limitation
Intrinsically safe devices are designed to ensure that they cannot release sufficient energy, under normal or fault conditions, to cause ignition of a specific hazardous atmospheric mixture. This is achieved by carefully controlling the electrical energy within the device so that sparks or heat emissions cannot ignite gases, dust, or fibers present in the environment.
Temperature Control
Temperature is a critical factor in the safety of equipment used in hazardous areas. Intrinsically safe devices are designed to operate below the ignition temperature of the specific hazardous substances they might encounter. This involves selecting components and designing circuits in a way that the maximum surface temperature of the device will not ignite a flammable atmosphere.
Component Selection
The components used in intrinsically safe devices are selected based on their ability to prevent the release of excessive energy. This means using components that inherently limit current or voltage to safe levels, even under fault conditions. High-quality, certified components are essential for ensuring the reliability and safety of the equipment.
Certification and Compliance
For a device to be considered intrinsically safe, it must undergo rigorous testing and certification by recognized authorities. Certifications such as ATEX (Europe) and HAZLOC (North America) are indicators that a device meets stringent safety standards for use in hazardous environments. These standards ensure that devices are not only designed according to safety principles but also tested to perform safely under expected conditions.
Safety Barriers and Isolation
Safety barriers and isolation methods are often employed in conjunction with intrinsically safe devices to further limit the energy reaching the hazardous area. These barriers are placed between the hazardous and non-hazardous areas, ensuring that only low energy communication or power reaches the intrinsically safe equipment. Proper selection and installation of these barriers are as critical as the device itself in maintaining intrinsic safety.
Understanding these principles is fundamental in selecting the right equipment for hazardous environments. It is not only about choosing devices labeled as intrinsically safe but selecting equipment that is designed and certified to operate safely within the specific conditions and substances present in your work environment. This approach is at the heart of the Intrinsically Safe Store’s commitment to offering high-quality, certified intrinsically safe and explosion-proof products, designed to prevent explosions and ensure safety in hazardous environments.
Key Features to Look for in Intrinsically Safe Equipment
When selecting intrinsically safe equipment for hazardous environments, understanding the key features that ensure safety and compliance is crucial. These features not only help in choosing the right devices but also ensure the protection of personnel and property in explosive atmospheres. Here are some essential characteristics to consider:
1. Certification and Compliance
Look for equipment that is certified and compliant with international safety standards such as ATEX (Europe) and HAZLOC (North America). These certifications guarantee that the devices meet the stringent requirements for use in explosive atmospheres.
2. Low Energy Design
Intrinsically safe devices are designed to operate at energy levels insufficient to cause an ignition. Ensure that the equipment you select is specifically engineered to minimize power consumption and prevent the ignition of flammable gases, vapors, or particles.
3. Durability and Robustness
Hazardous environments demand equipment that can withstand harsh conditions. Look for devices housed in robust enclosures that are resistant to extreme temperatures, impacts, and corrosive substances. This durability ensures long-term reliability and safety.
4. Explosion-Proof Enclosures
In addition to being intrinsically safe, some environments may require explosion-proof equipment. Such devices are designed to contain any internal explosion, preventing it from triggering a larger, external blast. Ensure that the equipment has an appropriate explosion-proof rating for your specific environment.
5. Ease of Use and Maintenance
The complexity of operating in hazardous environments makes it essential for equipment to be user-friendly. Choose devices that are easy to use and maintain, with clear instructions and accessible support resources. This reduces the risk of accidental misuse, which could compromise safety.
6. Compatibility and Integration
Ensure that the intrinsically safe equipment is compatible with existing systems and can be easily integrated into your operations. This compatibility helps in maintaining efficient workflows and ensuring universal safety protocols are adhered to throughout your workplace.
7. Environmental Protection
Select equipment rated for protection against environmental factors such as water, dust, and explosive gases. Look for IP ratings (Ingress Protection) that indicate the level of sealing effectiveness of electrical enclosures against intrusion from foreign bodies and moisture.
In summary, when choosing intrinsically safe devices, prioritize features that ensure compliance, safety, and reliability. By selecting equipment that meets these criteria, professionals and organizations can significantly mitigate the risks associated with operating in hazardous environments.
Common Misconceptions about Intrinsically Safe Products
When it comes to selecting intrinsically safe devices for hazardous environments, various misconceptions can lead to confusion and, potentially, unsafe decisions. Understanding and dispelling these myths is crucial for professionals and organizations aiming to uphold safety standards while operating in sectors such as petrochemical and mining.
Myth 1: Intrinsically Safe Means Explosion-Proof
One common misunderstanding is equating intrinsically safe (IS) equipment with explosion-proof devices. While both designs aim to prevent explosions, their approaches are fundamentally different. Intrinsically safe devices are engineered to operate at energy levels too low to cause ignition of flammable gases or vapors, thus preventing explosions at the source. In contrast, explosion-proof equipment is designed to contain an explosion within its enclosure, preventing the spread of flames and potential chain reactions. It’s essential to choose the type that best suits the specific needs of your environment.
Myth 2: All Intrinsically Safe Devices Are the Same
Another misconception is that all IS devices offer the same level of protection across various hazardous environments. In reality, intrinsically safe certifications, such as ATEX (for Europe) and HAZLOC (for North America), indicate the specific conditions under which an item can safely operate. These certifications take into account factors like the nature of the hazardous material (gas, vapor, or dust), the typical operating temperatures, and the device’s energy levels. Therefore, it’s critical to select devices with the appropriate certification for your specific environment.
Myth 3: Intrinsically Safe Devices Don’t Require Regular Maintenance
Some might believe that once an intrinsically safe device is installed, it doesn’t require regular maintenance since it’s designed to prevent ignition. However, like all safety equipment, IS devices need routine checks and maintenance to ensure they continue to operate within the safe parameters for which they were designed. Regular maintenance not only confirms the integrity of the product but also helps in identifying potential issues before they become serious hazards.
Myth 4: Certification Guarantees Total Safety
While certification is an essential factor in selecting intrinsically safe equipment, it doesn’t eliminate the need for proper usage and adherence to safety protocols. Certified equipment is designed to significantly reduce the risk of ignition in hazardous environments. However, the effectiveness of these devices also depends on their correct application and the overall safety culture within the organization. Comprehensive training and ongoing safety education are paramount to ensure that these devices contribute effectively to a safer working environment.
By understanding and addressing these misconceptions, professionals and organizations can make informed decisions when choosing intrinsically safe devices. This knowledge, combined with the high-quality, certified intrinsically safe and explosion-proof products offered by The Intrinsically Safe Store, empowers users to prevent explosions and ensure safety in hazardous environments effectively.
Comparison of Intrinsically Safe Equipment to Explosion-Proof Alternatives
In hazardous environments, selecting the right safety equipment can mean the difference between operational integrity and catastrophic failure. When it comes to ensuring the safety of such environments, two primary options emerge: intrinsically safe equipment and explosion-proof devices. Understanding the differences between these two can help you make informed decisions on how to choose intrinsically safe devices that best suit your operational needs.
Intrinsically Safe Equipment operates on the principle of energy limitation. These devices are designed to ensure that the energy levels are too low to cause ignition of flammable substances. This is achieved by limiting the amount of energy available for ignition, thus preventing the occurrence of an explosion. Intrinsically safe devices are particularly beneficial in environments where explosive gases, vapors, or dusts are present. Their designs ensure that even in the event of a component failure, there is insufficient energy to ignite the surrounding hazardous atmosphere. For professionals in the petrochemical, mining, and other industries with explosive atmospheres, selecting intrinsically safe devices means prioritizing continuous operation safety without the risk of igniting hazardous materials.
Explosion-Proof Equipment, on the other hand, is designed to contain an explosion within its enclosure, preventing the spread of flames or explosive gases into the surrounding environment. These robust enclosures can withstand and contain internal explosions, preventing them from causing wider damage. While effective, explosion-proof options are often heavier, bulkier, and sometimes more costly due to their rugged construction designed to contain explosions.
Key Differences
- Cost-Effectiveness: Intrinsically safe equipment is typically less expensive over its lifecycle compared to explosion-proof alternatives, not only in terms of initial purchase price but also installation and maintenance costs. Intrinsically safe devices require less stringent wiring practices, which can reduce installation expenses.
- Flexibility and Portability: Intrinsically safe equipment tends to be more compact and lighter than explosion-proof devices, offering greater flexibility and ease of use in the field. This portability is crucial for tasks that require mobility within hazardous areas.
- Safety and Prevention: While both types of equipment are designed to mitigate risk, intrinsically safe devices focus on preventing the explosion at its source by limiting energy to safe levels. In contrast, explosion-proof equipment aims to contain an explosion should it occur.
- Certification and Compliance: Both intrinsically safe and explosion-proof devices must meet stringent regulatory standards, such as ATEX in the European Union and HAZLOC in North America. However, the certification processes can differ, with intrinsically safe equipment often undergoing more rigorous testing to prove that it cannot ignite hazardous atmospheres under normal or fault conditions.
In conclusion, the choice between intrinsically safe and explosion-proof equipment should be informed by a thorough risk assessment of the specific hazardous environment, considering factors such as the nature of the explosive materials present, the likelihood of an explosive atmosphere, and the operational requirements of the device. Understanding the unique benefits and limitations of each option ensures the safety and efficiency of operations in hazardous areas.
FAQs on Selecting the Right Intrinsically Safe Equipment for Hazardous Environments
How do I know if a device is intrinsically safe?
To determine if a device is intrinsically safe, look for certification markings from recognized standards such as ATEX (Europe) or HAZLOC (North America). These certifications ensure that the device operates at energy levels insufficient to cause ignition in hazardous environments. Manufacturers, including The Intrinsically Safe Store, provide documentation and labels indicating the compliance and certification of their devices.
How do I select the right intrinsically safe equipment for my needs?
Selecting the right intrinsically safe equipment involves understanding the specific hazards present in your environment. Key factors to consider include the type of hazardous material (gas, vapors, or dust), the zone classification of the hazard area, and the operational requirements of the device (such as battery life, durability, and functionality). Consulting with experts like those at The Intrinsically Safe Store can also provide insights tailored to your industry’s needs.
What factors should I consider when determining the safety level required?
The safety level required for intrinsically safe equipment in your operation depends on the zone classification of the hazardous area and the nature of the explosive materials present. Zones are defined based on the frequency and duration of the presence of an explosive atmosphere, with Zone 0 (or 20 for dust) representing areas where explosive atmospheres are continuously present, and Zone 2 (or 22 for dust) where it is less likely to occur and for shorter periods. The type of explosive atmosphere (Group I for mines, Group II for gases, and Group III for dust) also influences the selection. Compatibility with the specific hazardous substances and operating conditions are crucial factors as well.
Can intrinsically safe equipment be repaired or must it be replaced?
Intrinsically safe equipment can be repaired, but it must be done so under stringent conditions to ensure that the repairs or replacements of parts do not compromise its intrinsically safe properties. Only certified service centers and technicians should perform repairs on these devices. Unauthorized modifications or repairs could invalidate certifications and render the equipment unsafe.
How do I verify that intrinsically safe equipment is still safe after maintenance?
After maintenance, verification that intrinsically safe equipment is still safe involves ensuring that any repairs or modifications were conducted by certified technicians and that the device has been tested and recertified if necessary. The equipment should be thoroughly inspected for any damage or unauthorized alterations. Refer to the manufacturer’s guidelines or consult with experts like The Intrinsically Safe Store to confirm compliance and certifications are intact post-maintenance.