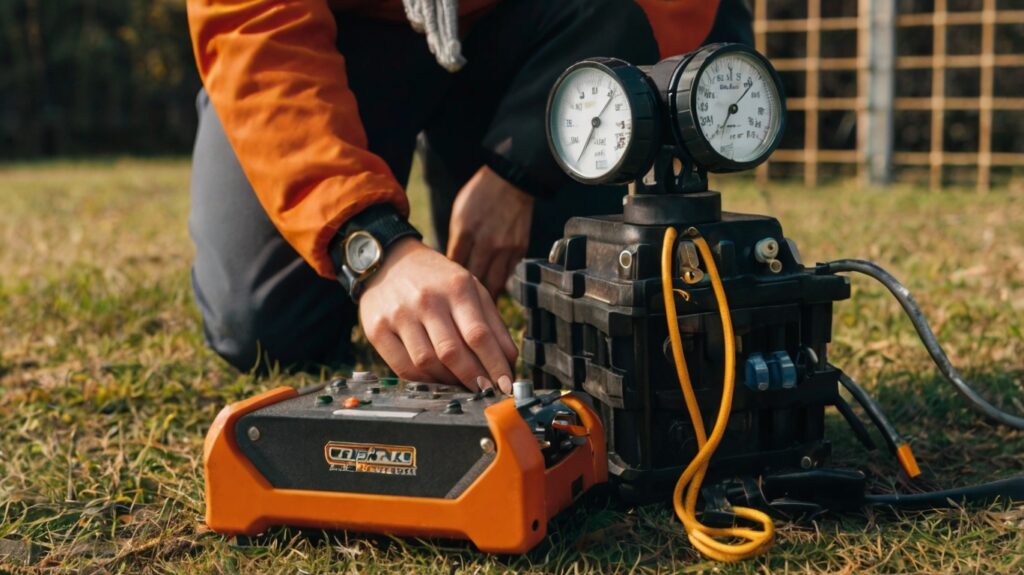
Definition: Industrial equipment maintenance involves the installation, troubleshooting, and ongoing upkeep of complex machinery used in various industries such as manufacturing, processing, and construction. It is crucial for ensuring the reliability, efficiency, and safety of industrial operations.
Types of Maintenance:
- Total Productive Maintenance (TPM): A holistic approach that involves both production and maintenance teams to optimize equipment performance, reduce downtime, and improve overall production quality. It uses metrics like OEE (Overall Equipment Effectiveness), MTTR (Mean Time To Repair), and MTBF (Mean Time Between Failures) to drive continuous improvement.
- Preventive Maintenance: Scheduled, regular maintenance activities aimed at preventing equipment failures through periodic inspections and replacements based on reliability tests and design life expectations.
- Predictive Maintenance: Uses advanced diagnostic methods such as vibration analysis, oil analysis, and machine learning algorithms to predict equipment failures and schedule maintenance before issues arise.
- Periodic Maintenance: Involves stopping equipment at predetermined intervals for overhaul, repair, or replacement of parts to prevent major failures and reduce unplanned downtime.
Career Overview: Industrial equipment maintenance requires highly skilled specialists who can diagnose, troubleshoot, and repair heavy machinery. Careers in this field include heavy equipment mechanics, millwrights, and machinery maintenance workers. These roles often require a postsecondary education or apprenticeship training in areas such as mathematics, electricity, and hydraulics.
Importance: Effective industrial equipment maintenance is critical for minimizing downtime, ensuring safety, and optimizing production efficiency. It also has a significant impact on the financial performance of industries, as companies with robust maintenance strategies can reduce operational costs and improve overall productivity.
Fun Fact: The U.S. Bureau of Labor Statistics projects that employment of industrial machinery mechanics is expected to grow by 19% from 2012 to 2022, highlighting the increasing demand for skilled maintenance professionals in this field.
- Emphasizes the strategic importance of regular equipment maintenance for operational excellence, safety, and business sustainability in hazardous manufacturing environments.
- Highlights the benefits of regular check-ups including enhanced safety, prevention of costly downtime, and compliance with regulatory standards.
- Advocates for predictive maintenance over reactive strategies to minimize risks and optimize machinery performance, endorsing a proactive approach in hazardous settings.
Introduction to Equipment Maintenance in Manufacturing
In the competitive and highly regulated world of manufacturing, especially within industries that operate in hazardous environments, the importance of equipment maintenance cannot be overstressed. Proper maintenance of industrial equipment is not just a safety measure; it’s a critical component of operational excellence and business sustainability. Key to navigating these waters is understanding that equipment check-ups go far beyond mere compliance. They are, in fact, a strategic approach to guaranteeing uninterrupted production, ensuring worker safety, and maintaining the quality of products.
Regular equipment maintenance, often viewed through the lens of industrial equipment maintenance, involves a systematic inspection, cleaning, lubrication, adjustments, and parts replacement of industrial machinery and devices. This process is pivotal in identifying wear and tear before it escalates into a major breakdown, potentially causing unsafe working conditions, significant production downtime, and financial losses.
At The Intrinsically Safe Store, our commitment to operational excellence and a supportive work environment underscores the significance we place on regular equipment check-ups. By integrating safety products designed for hazardous environments—such as intrinsically safe phones, explosion-proof tablets, and lighting—we envelop the manufacturing process in a layer of reliability and safety that protects both the workforce and the machinery they operate.
By fostering a culture that values clear, organized, and transparent operations, and emphasizing personal development, we aim to elevate the conversation around industrial equipment maintenance. It’s not just about ticking off a checklist; it’s about nurturing an ecosystem that thrives on vigilance, innovation, and a steadfast commitment to excellence. Through a blend of comprehensive training, specialized safety products, and a results-driven approach, we empower industries to not only meet but exceed their operational goals while maintaining the highest standards of safety and efficiency.
This strategic approach to equipment maintenance, rooted in understanding its critical role in manufacturing, directly aligns with our motto of operational excellence and providing a supportive, non-toxic work environment. In doing so, it not only ensures the longevity and reliability of industrial equipment but also fosters an environment where personal development and work-life balance are not just encouraged but are integral to the company’s ethos.
Take Action for a Safer Tomorrow
In the world of manufacturing, especially within hazardous environments, ensuring the regular check-up of industrial equipment isn’t just a recommendation – it’s a necessity. At The Intrinsically Safe Store, we’re committed to more than just selling products; we’re invested in fostering operational excellence and safety in every workspace. Here’s how you can partner with us to make safety a cornerstone of your operations:
- Reach Out for Expert Advice: Not sure where to start with ensuring your equipment is up to safety standards? Our team of experts is here to guide you through selecting the right intrinsically safe and explosion-proof products for your needs.
- Explore Our Wide Range of Products: From intrinsically safe phones to explosion-proof lighting, our extensive product catalog is tailored to meet the diverse requirements of hazardous industries like oil & gas, chemical, and pharmaceutical fields.
- Embrace a Culture of Safety: By choosing our products, you’re not just buying safety equipment; you’re investing in a philosophy of operational excellence, personal development, and a non-toxic work environment.
- Invest in Reliable Safety Solutions: Don’t wait for an accident to think about safety. Proactive measures today can prevent disasters tomorrow.
Discover how our specialized safety products, backed by a commitment to excellence and support, can help you maintain a safe, efficient, and compliant manufacturing operation. Visit our website now to learn more and to start prioritizing the well-being of your team with The Intrinsically Safe Store.
Key Benefits of Regular Equipment Check-Ups
Regular equipment check-ups in the manufacturing sector are an integral part of maintaining operational excellence and ensuring workplace safety, especially in industries operating within hazardous environments. The key benefits of conducting consistent inspections and maintenance checks of industrial equipment are manifold and critical for both employees’ safety and the successful, efficient operation of the company.
Enhanced Safety
One of the most significant benefits of regular equipment check-ups is the enhanced safety it guarantees for employees. In industries like oil & gas, chemical manufacturing, and pharmaceuticals, where the potential for hazardous incidents is higher, routine inspections help identify and mitigate risks before they can lead to accidents. Ensuring that all equipment operates correctly minimizes the chance of malfunction that could cause potentially dangerous situations, thus protecting lives and preventing injury.
Prevention of Costly Downtime
Equipment failures can result in unexpected downtime, significantly impacting productivity and, ultimately, the bottom line. Regular check-ups allow for the identification and rectification of issues before they escalate into major failures that can halt production. By proactively maintaining equipment, companies can plan maintenance during scheduled downtimes, thus minimizing disruption and maintaining steady production levels.
Prolonged Equipment Lifespan
Consistent maintenance and checks help extend the lifespan of industrial equipment. By replacing worn parts and making necessary adjustments, equipment can operate at optimal levels for longer, delaying the need for costly replacements. This not only ensures that the company gets the most out of its investment but also contributes to more sustainable operational practices by reducing waste.
Improved Efficiency and Performance
Regularly maintained equipment operates more efficiently and with better performance. This efficiency not only contributes to operational excellence but also to energy savings and reduced operational costs. Optimized equipment requires less energy to operate, which can significantly lower energy bills and contribute to a company’s sustainability goals.
Compliance and Standards Adherence
Industries operating in hazardous environments are often subject to strict regulatory standards and compliance requirements to ensure safety. Regular equipment check-ups help ensure that all operations are in line with these regulations, avoiding legal ramifications and potential fines. Keeping equipment up to standard also helps maintain a company’s reputation as a compliance-focused and safety-first organization.
Support for a Non-toxic Work Environment
Beyond the technical and operational benefits, regular equipment maintenance supports the creation and maintenance of a supportive, non-toxic work environment. When employees see that their employer invests in equipment safety and maintenance, it reassures them of their value to the company. This contributes to a culture where safety and personal development are prioritized, aligning with the values of companies like The Intrinsically Safe Store, which emphasizes the importance of a supportive work environment and operational excellence.
In summation, the benefits of regular equipment check-ups in the manufacturing sector are comprehensive, affecting everything from safety to efficiency and compliance. In hazardous working environments, these benefits are not just advantageous—they’re essential for ensuring the well-being of employees, the longevity of equipment, and the smooth, efficient operation of the company.
Maximizing Uptime and Productivity
In the high-stakes world of manufacturing, particularly where hazardous environments are concerned, equipment reliability isn’t just a matter of efficiency—it’s integral to operational safety and worker well-being. Regular equipment check-ups stand at the heart of maximizing uptime and productivity, offering a proactive path to maintaining not only machinery but also the morale and safety of the workforce.
The Pillars of Industrial Equipment Maintenance
- Predictive Maintenance: More than just a buzzword, predictive maintenance is the cornerstone of avoiding unexpected downtime. By utilizing data analysis and monitoring tools, manufacturers can predict equipment failures before they happen, scheduling maintenance activities at the most opportune times without disrupting production.
- Scheduled Downtime: Strategically planned downtime for equipment check-ups may seem counterintuitive to productivity. Yet, these scheduled intervals allow for thorough inspections, updates, and necessary repairs, which in turn minimize unplanned outages that could significantly halt operations, endanger employees, and impact the bottom line.
- Continuous Training: Empowering employees through continuous training on the latest safety protocols and equipment handling ensures that machinery is operated correctly and efficiently. In an environment that champions personal development and work-life balance, staff are more engaged, contributing to a culture of safety and operational excellence.
- Embracing Technology: Leveraging technology for equipment maintenance—from sensor-based monitoring to AI-driven predictive analytics—enables manufacturers to stay ahead of potential issues. This technological edge is crucial in hazardous environments, where the consequences of equipment failure are magnified.
The Intrinsically Safe Store Approach
At The Intrinsically Safe Store, we understand that in hazardous environments, equipment maintenance is interconnected with safety and productivity. Our commitment to operational excellence is evident in the quality and reliability of our intrinsically safe and explosion-proof products. We believe in providing not just equipment but solutions that ensure our clients’ operations are not just compliant, but also competitive and cutting-edge.
Through regular equipment check-ups, manufacturers can mitigate risks, reduce costly downtime, enhance worker safety, and ultimately, secure a stronger, more productive future. This proactive approach aligns with our ethos of fostering a supportive, non-toxic work environment focused on personal and collective advancement.
Quality Control: Impact on Product Output
Quality control is an integral part of industrial equipment maintenance and plays a pivotal role in influencing product output in manufacturing environments, especially those that are considered hazardous. Ensuring the consistent functionality and safety of equipment through regular check-ups is not merely a matter of meeting compliance standards; it is about safeguarding the integrity of manufacturing processes and the quality of the final product.
In industries such as oil & gas, chemical, and pharmaceuticals, the margin for error is minimal. Equipment failures can lead to not only productivity losses but also potentially catastrophic safety incidents. Thus, maintaining equipment in optimal condition is critical. This involves routine inspections, testing, validation, and calibration of equipment, all of which fall under the broader spectrum of quality control.
Regular equipment maintenance check-ups help identify wear and tear, mitigate risks of unexpected breakdowns, and extend the equipment’s life span. This proactive approach to maintenance ensures that equipment performs consistently at its peak efficiency, thereby directly impacting the quality of product output. For instance, a precisely calibrated intrinsically safe phone or an explosion-proof tablet in a hazardous environment ensures accurate data collection and communication, critical components in maintaining operational excellence.
Moreover, quality control through regular equipment maintenance aligns with the principles of operational excellence and supports a non-toxic, supportive work environment. It emphasizes the importance of reliability, efficiency, and safety—all of which contribute to a positive and productive workplace. This alignment not only enhances the company’s operational capabilities but also fosters an environment that prioritizes personal development and employee well-being. As employees understand their role in maintaining and improving quality standards, they feel more valued and integral to the company’s mission.
In sum, quality control via regular industrial equipment maintenance is indispensable for ensuring safety, operational excellence, and quality product output. It is a fundamental aspect that supports the broader objectives of providing a supportive, development-focused work environment and maintaining the integrity and reliability of manufacturing processes in hazardous industries.
Predictive Maintenance versus Reactive Maintenance
In the world of industrial equipment maintenance, two philosophies stand out: predictive maintenance and reactive maintenance. Understanding the differences between these approaches is crucial for companies operating in hazardous environments, where the stakes for safety and operational excellence are particularly high.
Predictive Maintenance
Predictive maintenance represents a proactive strategy aimed at identifying and addressing potential equipment failures before they occur. This approach relies heavily on the collection and analysis of data from equipment sensors and monitoring systems. By analyzing trends and anomalies, maintenance teams can predict when a piece of equipment is likely to fail and intervene accordingly. Predictive maintenance facilitates a planned approach to repairs and part replacements, minimizing unplanned downtime and extending the life of equipment. For industries such as oil & gas, chemical, and pharmaceuticals, where equipment failure can have severe safety implications, predictive maintenance is not just a strategy but a necessity.
Reactive Maintenance
Contrastingly, reactive maintenance is a strategy that waits for equipment to fail before any action is taken. This approach often results in unplanned downtime, higher repair costs, and, in hazardous environments, elevated risks to safety. While reactive maintenance may seem cost-effective in the short term, since it avoids the upfront investment in monitoring equipment and data analysis systems, it can lead to significantly greater expenses and safety risks over time. In environments where equipment failure can lead to significant hazards, relying solely on reactive maintenance is a risky strategy.
Both approaches to maintenance—predictive and reactive—have their place in industrial operations. However, the trend is increasingly moving towards predictive maintenance, driven by advancements in sensor technology and data analytics. Implementing a predictive maintenance strategy not only supports operational excellence but also aligns with a supportive, non-toxic work environment by prioritizing the safety and well-being of personnel.
For companies like The Intrinsically Safe Store, which operate at the intersection of safety and industrial efficiency, embracing predictive maintenance is a cornerstone of offering both safety expertise and operational excellence. Predictive maintenance aligns with our values by enhancing safety, minimizing downtime, and supporting a results-driven, transparent approach to operations. It underscores our commitment to a supportive, non-toxic culture where personal development and operational success go hand in hand.
The Dangers of Neglecting Equipment Maintenance
In the fast-paced world of manufacturing, especially within industries operating in hazardous environments, the maintenance of industrial equipment can sometimes fall by the wayside. However, neglecting equipment maintenance can lead to severe and far-reaching consequences that not only affect operational efficiency but also safety and compliance.
Safety Risks
The foremost risk of neglecting equipment maintenance is the compromise to worker safety. Equipment that is not regularly checked or properly maintained can malfunction, potentially causing accidents or exposing workers to hazardous conditions. This risk is particularly pronounced in industries such as oil & gas, chemical, and pharmaceuticals, where the consequences can be catastrophic due to the nature of the materials handled. A single incident can result in injury or even loss of life, highlighting the critical importance of regular maintenance checks.
Operational Downtime
Malfunctioning equipment due to poor maintenance practices can lead to unexpected downtime, significantly impacting production schedules and operational efficiency. The time and resources required to repair or replace equipment hastily are often much greater than those needed for regular, planned maintenance. Downtime not only affects the company’s bottom line but can also damage its reputation among customers and partners relying on its products or services.
Increased Costs
Neglecting equipment maintenance can lead to higher operational costs in the long run. Equipment that is not properly maintained tends to consume more energy, require more frequent repairs, and have a shortened lifespan, leading to increased expenditure on energy, spare parts, and replacement equipment. Regular maintenance helps in detecting and addressing issues early, often resulting in cost savings and extended equipment life.
Regulatory Non-Compliance
For industries working in hazardous environments, compliance with safety and environmental regulations is non-negotiable. Failure to maintain equipment can result in violations of these regulations, leading to fines, legal action, and damage to the company’s reputation. Regular maintenance checks help ensure that equipment operates within the required standards, avoiding the risks of non-compliance.
Conclusion
In the context of promoting a supportive, non-toxic work environment and personal development, ensuring the safety and well-being of employees through regular equipment maintenance cannot be overstated. The Intrinsically Safe Store, with its commitment to operational excellence and a results-driven approach, underscores the importance of these practices not only for the direct benefit they provide in terms of safety and efficiency but also as a reflection of the company’s values. Encouraging a culture that prioritizes thorough and regular equipment maintenance is integral to fostering a supportive and safe working environment, a hallmark of truly accountable and employee-focused organizations.
FAQs Section for “The Importance of Regular Equipment Check-ups in Manufacturing”
How often should equipment check-ups be scheduled?
Equipment check-ups should be scheduled based on the manufacturer’s recommendations and the intensity of equipment use. For heavy industrial applications, such as in the oil & gas, chemical, and pharmaceutical industries, it is advisable to perform at least quarterly inspections. However, critical equipment that is integral to operational safety or production continuity may require more frequent check-ups.
Can regular check-ups improve equipment lifespan?
Yes, regular equipment check-ups can significantly improve the lifespan of industrial equipment. By identifying and rectifying minor issues before they evolve into major failures, maintenance teams can prevent unnecessary wear and tear, thus extending the operational life of the equipment.
Who should perform equipment check-ups?
Equipment check-ups should be performed by qualified maintenance technicians who possess a deep understanding of the specific type of equipment. For specialized industrial equipment used in hazardous environments, it is crucial to engage technicians who are not only skilled in maintenance practices but also trained in handling equipment safely in such conditions.
What should be included in a typical equipment check-up?
A typical equipment check-up should include a visual inspection, testing for functionality and performance, verification of safety features, and a review of any error logs or alerts. Additionally, it may involve the replacement of worn-out parts, lubrication of moving components, and updates to software controlling the equipment. The exact scope will depend on the type of equipment and its usage conditions.
How can a company implement an effective maintenance schedule?
To implement an effective maintenance schedule, a company should start by inventorying all industrial equipment and categorizing each item based on its criticality to operations. Next, develop a maintenance plan that aligns with manufacturer guidelines and industry best practices. Incorporate a mix of preventive and predictive maintenance strategies, utilizing technology such as IoT sensors for real-time monitoring where feasible. Ensure the schedule is flexible enough to accommodate emergency repairs without significantly disrupting operations. Lastly, encourage a culture of proactive maintenance within the organization to minimize downtime and enhance operational efficiency.