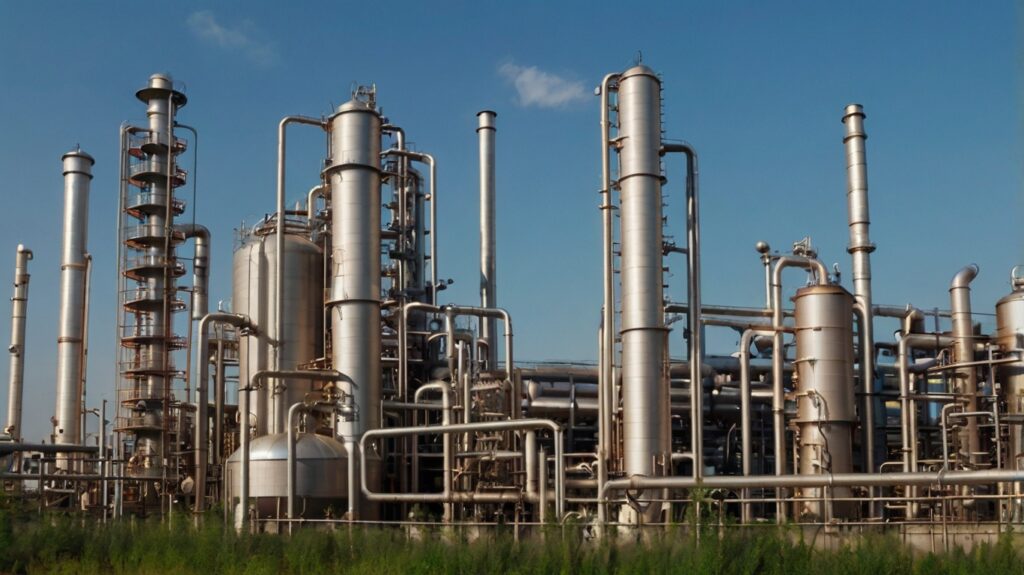
Definition: IoT-enabled devices are part of the Internet of Things (IoT), a network of physical objects, vehicles, home appliances, and other items embedded with sensors, software, and connectivity, allowing them to collect, exchange, and act on data.
Key Statistics:
- By 2025, it is estimated that there will be over 64 billion IoT devices worldwide, significantly surpassing the number of people on the planet.
- IoT devices are expected to generate 73.1 zettabytes of data by 2025, a substantial increase from current data volumes.
- Every minute, 152,200 IoT devices connect to the internet, highlighting the rapid growth of IoT adoption.
Examples in Action:
- Smart Homes: Devices like smart thermostats, voice-controlled assistants (e.g., Amazon Echo, Google Home), and smart light bulbs automate home tasks, enhance comfort, and reduce energy consumption.
- Connected Healthcare: Wearable medical sensors and smart mirrors enable remote patient monitoring, real-time health parameter tracking, and even remote medical diagnoses.
- Industrial Automation: IoT devices in manufacturing, such as smart factories and industrial robots, improve efficiency by up to 12% and add significant economic value, with smart factories in North America expected to add 500billionto500 billion to 500billionto1.5 trillion to the economy in the next five years.
Security and Risks:
- Despite the benefits, IoT devices often come with inherent security risks, including vulnerabilities to hacking, data breaches, and the creation of botnets. For example, hackers have been known to compromise devices like thermostats, baby monitors, and printers, highlighting the need for robust cybersecurity measures.
Fun Fact: The concept of IoT dates back to the early 1980s when university students at Carnegie Mellon created a sensor-controlled Coke machine that could be monitored via a computer program, marking one of the earliest examples of IoT technology in action.
- The Industrial Internet of Things (IIoT) revolutionizes manufacturing by integrating IoT-enabled devices for enhanced operational efficiency, safety, and productivity, particularly in hazardous environments.
- Implementing IIoT in factories offers significant advantages such as improved operational efficiency, worker safety, cost reduction, quality control, and sustainability, essential for industries like petrochemical and mining.
- Smart devices in IIoT facilitate predictive maintenance and real-time monitoring, crucial for optimizing safety and preventing downtime in environments at risk of explosive atmospheres.
Introduction to IIoT and Manufacturing
The Industrial Internet of Things (IIoT) marks a revolutionary shift in manufacturing, integrating IoT-enabled devices into the very fabric of industrial operations. This transformation leverages smart devices and sensors to collect, analyze, and utilize data in ways that significantly enhance operational efficiency, safety, and productivity. In essence, IIoT represents the convergence of information technology (IT) and operational technology (OT), enabling a level of connectivity and insight previously unimaginable.
At the heart of IIoT are IoT-enabled devices, which serve as the eyes and ears of the industrial environment. These devices collect critical data from machines and systems across the manufacturing floor, providing a real-time overview of operations that can help identify inefficiencies, predict equipment failures, and guide strategic decision-making. This ecosystem of connected devices not only streamlines processes but also introduces unprecedented levels of automation and precision in manufacturing.
Safety is a paramount concern in such technologically advanced environments, especially in sectors where the risk of explosive atmospheres cannot be ignored. The integration of intrinsically safe IoT-enabled devices ensures that the benefits of IIoT can be harnessed without compromising the safety of the workplace or personnel. These devices are specifically designed to operate in hazardous areas by limiting the energy, electrical or thermal, that they can release, thereby preventing ignition of flammable materials.
For industries like petrochemical and mining, where the potential for explosive atmospheres is a constant threat, the advent of IIoT offers a promising path forward. It allows for the optimization of manufacturing processes while adhering to the stringent safety protocols these industries must follow. By utilizing intrinsically safe and explosion-proof IoT-enabled devices, companies can embrace the efficiency and productivity gains of IIoT without increasing the risk to their operations or employees.
The integration of IIoT in manufacturing, therefore, represents a win-win scenario. It achieves operational excellence and maintains the highest safety standards, ensuring that advancements in technology do not come at the cost of workers’ safety or environmental stewardship. As industries continue to evolve with these intelligent systems, the role of specialized equipment, such as that offered by the Intrinsically Safe Store, becomes increasingly vital in bridging the gap between innovation and safety.
Take Your Safety to the Next Level with IoT-Enabled Devices
In today’s rapidly evolving industrial landscape, ensuring the safety of personnel and operations in hazardous environments has never been more critical. The Intrinsically Safe Store stands at the forefront of this mission, providing an unparalleled selection of IoT-enabled devices tailored for safety in high-risk sectors such as petrochemical and mining. Here’s why you should consider enhancing your safety protocols with our products:
- Enhanced Safety Compliance: Our selection of IoT-enabled devices meets the most stringent safety standards, including ATEX and HAZLOC certifications. By incorporating our equipment into your safety protocols, you ensure compliance with industry regulations, protecting both your workforce and operations.
- Prevention of Hazardous Incidents: Equip your environment with our intrinsically safe and explosion-proof devices designed to operate safely amidst flammable gases or vapors, significantly reducing the risk of ignition and explosions.
- Real-Time Monitoring and Control: Leverage the power of IoT to gain real-time insights into the operational status of machinery and environmental conditions. Early detection of potential issues allows for immediate corrective actions, enhancing overall safety and efficiency.
- Customized Solutions for Hazardous Environments: Understanding that every industrial setting has unique challenges, we offer expert consultations to tailor the most effective safety solutions for your specific needs.
Invest in safety today and future-proof your operations against potential hazards. Explore our collection of safety devices and take the first step towards a safer, smarter working environment.
The Evolution of Industrial Automation
The journey towards the sophisticated, interconnected enterprise we witness today in the industrial sector has been marked by continuous innovation and the relentless pursuit of efficiency and safety. The advent of the Industrial Internet of Things (IIoT) represents a pivotal phase in this evolution, where the leap from mechanical automation to digital transformation is drastically reshaping manufacturing landscapes.
In the early stages of industrial automation, the focus was primarily on mechanizing repetitive tasks to increase productivity and reduce human error. These were the days of assembly lines that revolutionized manufacturing processes, enabling mass production. However, with advancements come heightened complexities and the inevitable need for more nuanced control systems. This spawned the era of programmable logic controllers (PLCs) and robotic arms, which introduced a new level of flexibility and efficiency in manufacturing operations.
The transition from simple mechanization to sophisticated digital automation was not instantaneous. It required incremental advancements in technology and a shift in mindset towards embracing digital solutions. The development and integration of IoT-enabled devices became the cornerstone of this transformation. These devices, capable of collecting and analyzing data in real-time, opened up possibilities for unprecedented operational insights, predictive maintenance, and optimization that were once unimaginable.
Today, the IIoT stands at the forefront of industrial automation, driven by smart, IoT-enabled devices. These devices are not just transforming the way factories operate but are also enhancing safety protocols in hazardous environments. For instance, intrinsically safe devices, equipped with IoT capabilities, can now monitor conditions in real-time, ensuring that operations within sectors like petrochemical and mining are conducted within safe parameters. This level of monitoring helps in preemptively identifying risks and averting potential incidents, which is critical in environments where the margin for error is slim.
The evolution of industrial automation, powered by IIoT, is a testament to the industry’s commitment to advancing safety alongside efficiency. As we move forward, the role of IoT-enabled devices in automating and securing industrial operations will only grow, underscoring the importance of adopting technologies that not only enhance operational efficiency but also prioritize the safety of personnel in hazardous environments.
Advantages of Implementing IIoT in Factories
The Industrial Internet of Things (IIoT) represents a seismic shift in the way factories operate, ushering in an era of unprecedented efficiency, safety, and productivity. By integrating IoT-enabled devices into the manufacturing environment, organizations operating in hazardous industries such as petrochemical, mining, and others can reap several significant benefits. Here are some of the key advantages:
Enhanced Operational Efficiency
IIoT platforms enable real-time monitoring and control of equipment and processes, leading to improved operational efficiency. By harnessing data from IoT-enabled devices, factories can predict maintenance needs, minimize downtime, and optimize production schedules, significantly improving overall productivity.
Improved Worker Safety
Safety is a paramount concern in hazardous environments. IoT-enabled devices, particularly those designed to meet the stringent safety requirements of intrinsically safe and explosion-proof certifications, play a crucial role in ensuring worker safety. These devices can monitor environmental conditions, detect the presence of hazardous gases or vapors, and trigger alarms or emergency shutdowns in dangerous situations, thereby preventing accidents and ensuring a safer workplace.
Cost Reduction
Implementing IIoT can lead to substantial cost savings over time. By optimizing resource utilization, reducing waste, and minimizing equipment downtime, factories can lower operational costs. Additionally, the data collected from IoT-enabled devices can be used to make informed decisions that further drive down costs, such as predictive maintenance which prevents costly repairs and replacements.
Enhanced Quality Control
IIoT technologies offer advanced monitoring capabilities, enabling factories to maintain high standards of product quality. Sensors and automation devices can detect deviations in product specifications or manufacturing conditions in real-time, allowing for immediate corrections that ensure the consistency and quality of the final product.
Sustainable Operations
By optimizing energy use and reducing waste, IIoT contributes to more sustainable manufacturing practices. IoT-enabled devices monitor and manage energy consumption, identify inefficient processes, and suggest modifications to improve sustainability, helping companies meet their environmental responsibility goals.
In the context of hazardous environments, where the focus on safety and reliability is paramount, the Intrinsically Safe Store provides IoT-enabled devices that meet the toughest safety standards, including ATEX and HAZLOC certifications. These devices are engineered to prevent explosions and ensure the safety of personnel by operating at energy levels that cannot ignite flammable atmospheres, making them ideal for integrating into IIoT solutions in factories located in high-risk areas. Through the adoption of these technologies, industries are not only able to enhance operational efficiency and worker safety but also contribute toward creating a safer, more sustainable world.
Cost-Saving Strategies with Smart Devices
In the realm of manufacturing, especially within hazardous environments, operational efficiency and cost management are key priorities. The advent of the Industrial Internet of Things (IIoT) and the integration of IoT-enabled devices offer unprecedented opportunities for cost savings. By embracing smart devices within these high-risk settings, businesses can unlock significant financial benefits without compromising safety — a core value proposition from the Intrinsically Safe Store.
Predictive Maintenance
IoT-enabled devices can monitor the health and performance of manufacturing equipment in real-time. Through predictive analytics, these devices can forecast potential failures before they occur, facilitating timely maintenance interventions. This predictive maintenance strategy reduces the likelihood of expensive unscheduled downtime, extends the lifespan of equipment, and optimizes maintenance costs.
Energy Efficiency
Smart devices not only operate at low energy levels, preventing ignition in flammable atmospheres, but they also contribute to overall energy savings. By continuously monitoring and analyzing energy usage across operations, these IoT-enabled devices can identify inefficiencies and suggest optimizations. For industries like petrochemical and mining, where energy consumption is significant, even small percentage savings can translate into substantial cost reductions.
Resource Optimization
The integration of IoT-enabled devices enhances the visibility of manufacturing processes. It allows for precise tracking of materials, tools, and personnel in real time. This heightened visibility leads to improved resource allocation, minimizing waste and ensuring that every asset is used efficiently. In hazardous environments where every entry and operation must be carefully planned, such optimization not only saves costs but also enhances safety.
Compliance and Safety
Adhering to safety and regulatory standards is of paramount importance in environments prone to explosive atmospheres. Non-compliance can result in hefty fines and operational shutdowns. IoT-enabled devices, especially those certified and compliant with standards like ATEX and HAZLOC, ensure continuous monitoring and adherence to safety protocols. By preventing accidents and ensuring compliance, these smart devices significantly reduce the potential financial risks associated with safety breaches.
By implementing IoT-enabled devices that are specifically designed for safety and efficiency in hazardous environments, organizations can achieve a delicate balance between operational excellence and stringent safety protocols. The Intrinsically Safe Store’s offerings exemplify how technology can be leveraged to usher in a safer, more efficient era in manufacturing while securing cost savings in the process. This strategic adoption of smart devices stands as a testament to how innovation can align with safety to drive industry forward.
Predictive Maintenance and Downtime Reduction
In the realm of hazardous environments such as those in the petrochemical and mining industries, the implementation of IoT-enabled devices transcends mere operational efficiency and enters the critical domain of safety management. Predictive maintenance, enabled by the Industrial Internet of Things (IIoT), is a game-changer in reducing downtime and preventing potentially hazardous situations.
IoT-enabled devices, equipped with various sensors, collect real-time data on the condition and performance of machinery. This data includes temperature, vibration levels, and other critical indicators that signify the health of the equipment. Through advanced analytics and machine learning algorithms, this data is then analyzed to predict equipment failures before they occur. This predictive capability allows maintenance to be scheduled at convenient times, reducing unexpected breakdowns that can lead to hazardous situations and costly downtime.
For industries operating in environments where safety is paramount, the value of predictive maintenance becomes immeasurable. A sudden failure in such settings can not only lead to production losses but also pose significant risks of explosions or other dangerous incidents. By enabling early detection of potential issues, IoT-enabled devices play a crucial role in preempting these risks.
The Intrinsically Safe Store recognizes the importance of integrating these advanced technological solutions into safety equipment. Their range of IoT-enabled devices is designed to operate safely within hazardous environments, ensuring that the benefits of predictive maintenance can be realized without introducing new risks. These devices are built to comply with the stringent regulatory standards required in such settings, including ATEX and HAZLOC certifications. This ensures they not only contribute to operational efficiency and reduced downtime but also uphold the highest safety standards.
As industries continually seek ways to enhance safety and efficiency, the adoption of IoT-enabled devices for predictive maintenance signifies a proactive approach to risk management. By leveraging these technologies, companies can protect their personnel, minimize economic losses, and maintain compliance with safety regulations, all while navigating the complexities of hazardous environments. This strategic application of IIoT aligns with our commitment at The Intrinsically Safe Store to offer high-quality, certified intrinsically safe and explosion-proof products designed to prevent explosions and ensure safety in hazardous environments.
Quality Control and Real-time Monitoring
In the realm of manufacturing, especially within environments where the stakes are high due to the potential for explosive atmospheres, the role of IoT-enabled devices in quality control and real-time monitoring cannot be overstated. These smart, interconnected devices offer unprecedented opportunities to capture and analyze data, opening up new avenues for improving the safety, efficiency, and reliability of operations in sectors like petrochemical, mining, and more.
Leveraging IoT for Enhanced Safety Measures
Safety is paramount in hazardous environments. IoT-enabled devices, particularly those that are intrinsically safe and explosion-proof, are pivotal in monitoring conditions in real time, thereby significantly mitigating risks. For instance, intrinsically safe sensors can continuously monitor the concentration of volatile gases, ensuring that they remain below dangerous levels. In the event of an anomaly, these systems can trigger alarms and initiate automated safety protocols, such as shutting down operations or activating ventilation systems, well before potential hazards escalate into accidents.
The Intrinsically Safe Store supplies a range of these critical safety devices, designed specifically for high-risk environments. Our products, including cameras, LED work lights, and cases for smartphones and tablets, are engineered to operate safely within explosive atmospheres, offering an added layer of protection and peace of mind for organizations prioritizing the safety of their personnel and facilities.
Boosting Operational Efficiency and Quality
Beyond safety, IoT-enabled devices play a crucial role in enhancing operational efficiency and product quality. Through the collection and analysis of data from various stages of the manufacturing process, these devices offer insights that can lead to significant improvements in production techniques. Real-time monitoring allows for immediate adjustments to be made, ensuring that conditions are always optimal for the highest quality output. For example, temperature and humidity sensors can ensure that storage conditions are maintained within precise parameters, preserving the integrity of sensitive materials.
The ability to monitor equipment performance in real time also enables predictive maintenance, reducing downtime and extending the lifespan of critical machinery. By analyzing data trends, potential issues can be identified and addressed before they lead to equipment failure, ensuring that operations run smoothly and without unexpected interruptions.
In conclusion, the integration of IoT-enabled devices into manufacturing and other high-risk sectors offers substantial benefits in terms of safety, quality control, and operational efficiency. As a provider of certified intrinsically safe and explosion-proof products, the Intrinsically Safe Store is at the forefront of delivering solutions that not only meet but exceed the stringent safety requirements of these challenging environments. By leveraging the power of IoT, we help our clients create safer, more efficient workplaces that stand ready to face the demands of modern manufacturing.
FAQs on The Industrial Internet of Things (IIoT): Transforming Manufacturing with Smart Devices
What are the main components of an IIoT system?
An Industrial Internet of Things (IIoT) system includes several key components vital for its operation. At the heart are the IoT-enabled devices, such as sensors and actuators, which gather and act on environmental data. These devices are connected via networks to edge computing devices or directly to cloud-based platforms where data is processed and analyzed. Software applications then utilize this data to optimize operations, predict maintenance needs, or monitor safety conditions in real-time. Additionally, user interfaces (UIs) allow human operators to interact with the system, making informed decisions based on the data presented.
What kind of smart devices are used in IIoT?
In an IIoT ecosystem, a wide range of smart devices are utilized to monitor and control industrial operations safely and efficiently. These include various sensors that detect parameters like temperature, pressure, and flow; actuators that control mechanical systems; intrinsically safe cameras, LED work lights, and flashlights for visual monitoring in hazardous environments; and ruggedized cases for smartphones and tablets that can safely be used near explosive atmospheres. All these devices are designed to collect and/or affect data in real time, enabling a more responsive and adaptive manufacturing process.
Can IIoT be implemented in any type of manufacturing?
Yes, IIoT can be applied across a variety of manufacturing settings, ranging from heavy industries like petrochemical and mining to precision manufacturing such as pharmaceuticals and electronics. The versatility of IIoT lies in its ability to be customized to the specific needs and safety requirements of each environment. By selecting the appropriate intrinsically safe and explosion-proof devices and technologies, organizations in even the most hazardous environments can harness the benefits of IIoT, improving efficiency, safety, and productivity.
How does IIoT enable real-time monitoring and control?
IIoT enables real-time monitoring and control by employing a network of connected devices that continuously collect and transmit data regarding the operational status of industrial processes. This data is analyzed either at the edge or in the cloud, providing actionable insights almost instantly. For example, temperature sensors within a reactor can provide immediate data to control systems to adjust heating elements, preventing overheating and potential hazards. This immediacy ensures that conditions are continually optimized for safety and efficiency, minimizing risks and downtime.
How does IIoT integrate with existing manufacturing systems?
Integrating IIoT with existing manufacturing systems typically involves connecting current machinery and control systems to IoT-enabled devices and platforms. This connection can be achieved through retrofitting existing equipment with sensors and smart devices or by incorporating interface modules that enable communication between older systems and modern IIoT infrastructure. Such integration allows manufacturers to gain the benefits of real-time monitoring and predictive analytics without the need to completely replace their current machinery, offering a cost-effective way to upgrade to smart manufacturing methodologies.