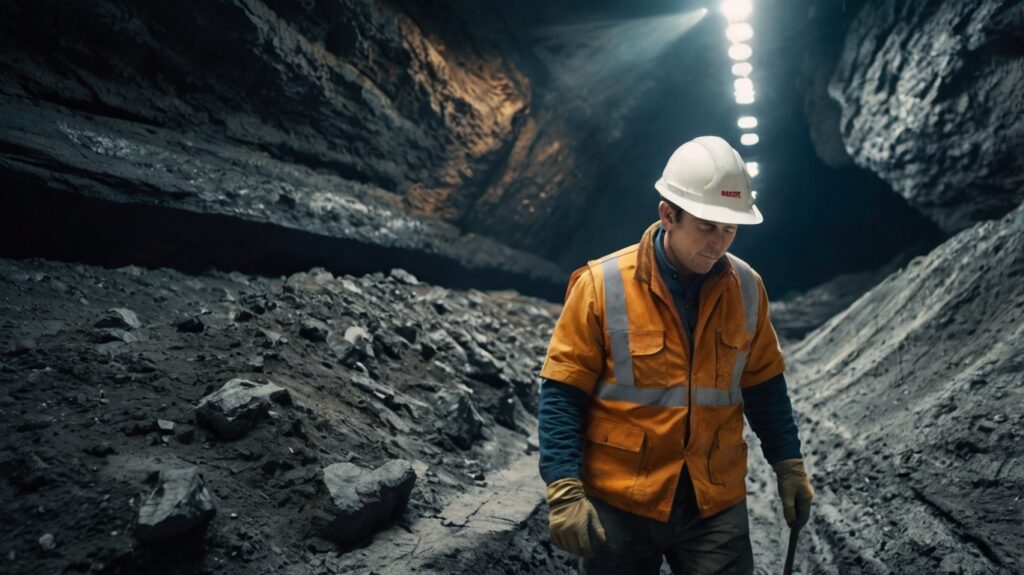
Definition: Mining equipment maintenance is the systematic and proactive approach to ensuring the optimal performance, safety, and longevity of mining machinery. It involves regular inspections, servicing, and repairs to prevent breakdowns, reduce downtime, and maintain operational efficiency in the harsh and demanding environment of mining operations.
Science Behind It: This maintenance strategy is grounded in understanding the mechanical, financial, and operational aspects of mining equipment. It leverages various types of maintenance, including preventive, corrective, reliability-centered, and predictive maintenance. By using data analytics, condition monitoring, and scheduled servicing, mining operators can identify and address potential issues before they escalate, thereby optimizing equipment performance and minimizing costs.
Examples in Action:
- Daily Checks: Operators conduct daily visual inspections, check fluid levels (engine oil, hydraulic fluid, coolant), and ensure all safety features are intact to prevent immediate breakdowns and accidents.
- Scheduled Servicing: Regular maintenance tasks such as lubrication, hydraulic system checks, and replacement of wear parts are performed according to manufacturer guidelines and operational usage to maintain equipment longevity and efficiency.
- Predictive Maintenance: Advanced technologies like condition monitoring and sensors are used to assess equipment health in real-time, allowing for maintenance to be performed as needed rather than on a fixed schedule.
Fun Fact: Did you know that proper maintenance of mining equipment can reduce maintenance costs by up to 30-50% of the overall haulage costs in surface mining operations? Additionally, regular servicing can extend the lifespan of equipment, enhance safety, and increase operational productivity, leading to significant financial savings and improved overall efficiency.
- Understanding the life cycle of mining equipment is essential for optimizing maintenance practices while ensuring safety in explosive environments.
- Maintenance strategies, including preventive and predictive approaches, play a crucial role in extending equipment lifespan and minimizing operational downtime.
- Proper training and safety protocols are vital for personnel to manage sophisticated equipment, ensuring efficiency and reducing risks in hazardous mining conditions.
Understanding Equipment Life Cycle in Mining
In the rigorous and hazardous world of mining, the life cycle of equipment is a critical factor that significantly impacts operational efficiency and safety. A deep understanding of this life cycle is essential for optimizing mining equipment maintenance, ensuring equipment longevity, and upholding the highest safety standards, especially in environments prone to explosive atmospheres.
The equipment life cycle in mining can be broken down into several key stages, starting with acquisition and installation. At this initial stage, selecting the right equipment that meets both operational needs and safety protocols like those set forth by ATEX and HAZLOC standards is crucial. For environments with a high risk of explosion, utilizing intrinsically safe and explosion-proof equipment from the outset is paramount to prevent ignition of flammable gases or vapors.
Following installation, the operation and maintenance phase represents the longest period of the equipment life cycle. Regular, comprehensive maintenance is critical, not only to ensure operational efficiency but also to extend the equipment’s life span. Maintenance routines should include inspections, cleaning, lubrication, and, when necessary, the timely replacement of worn parts. The focus should always be on preventing breakdowns and minimizing downtime, which can be costly and hazardous in mining operations.
Predictive maintenance strategies, underpinned by the latest monitoring technologies, can significantly enhance maintenance efforts. These strategies involve using sensors and data analytics to predict equipment failures before they occur, allowing for preemptive repairs that save time and money while enhancing safety. Products designed for use in hazardous environments, such as the intrinsically safe devices available from the Intrinsically Safe Store, are particularly suitable for these applications, as they reduce the risk of sparking that could lead to an explosion.
Eventually, equipment reaches the end of its useful life and must be decommissioned. This final phase involves safely removing the equipment from operation and recycling or disposing of it in an environmentally friendly manner. Proper decommissioning ensures that hazardous materials are not released into the environment, and valuable materials are recovered or recycled where possible.
Understanding each stage of the mining equipment life cycle, from acquisition and operation to decommissioning, is fundamental for optimizing maintenance practices. It not only contributes to extending the life span of essential mining equipment but also ensures compliance with strict safety standards, protecting both personnel and the environment. Adopting a holistic view of the equipment life cycle, underscored by a safety-first approach with the use of certified intrinsically safe and explosion-proof products, empowers mining operations to achieve their efficiency and safety goals.
Take Action for Safer, More Efficient Mining Operations
Optimizing the longevity and performance of your mining equipment isn’t just about implementing routine maintenance; it’s about incorporating best practices with the right tools for safety and efficiency. The Intrinsically Safe Store is your go-to partner for safeguarding your operations in hazardous environments. Here’s how we can assist:
- Discover a Wide Range of Safety Solutions: From intrinsically safe cameras to LED work lights and explosion-proof enclosures, our products are designed with the safety of your personnel and the integrity of your operations in mind.
- Ensure Compliance and Safety: All our devices are certified and comply with ATEX and HAZLOC standards, providing you peace of mind that your equipment meets the highest safety standards for hazardous environments.
- Enhance Maintenance Practices: Equip your maintenance teams with the safest, most reliable tools to perform their duties in potentially explosive atmospheres without compromising on efficiency or safety.
- Customized Solutions for Your Needs: We understand that each operation is unique. Contact us to discuss how our products can be integrated into your mining equipment maintenance plan for optimal safety and performance.
Take the first step toward extending the life cycle of your mining equipment and ensuring the safety of your operations. Visit The Intrinsically Safe Store today and explore our solutions. Together, let’s optimize your mining operations for safety and efficiency.
The Importance of Maintenance in Mining Operations
In the rugged and demanding field of mining, the importance of equipment maintenance cannot be overstated. The efficiency, safety, and continuity of mining operations hinge on the optimal functioning of machinery. Effective maintenance practices are critical not just for the lifespan of the mining equipment but also for the safety of the workforce and the minimization of environmental impact.
Preventive Maintenance: A Proactive Approach
Preventive maintenance forms the cornerstone of upkeep strategies in mining operations. This proactive approach involves regular, systematic inspection, detection, and correction of incipient failures, either before they occur or before they develop into major defects. By focusing on preventative measures, mining operations can avoid costly downtime and extend the life cycle of their equipment, ensuring that the machines are running safely and efficiently.
Safety as a Top Priority
In an environment as inherently hazardous as mining, the maintenance of equipment is inextricably linked with safety. Mining equipment maintenance must, therefore, include the latest safety protocols and practices. Utilizing intrinsically safe and explosion-proof equipment plays a vital role in preventing incidents. Devices such as LED work lights, flashlights, and communication tools designed for hazardous areas contribute to creating a safer work environment by significantly reducing the risk of sparking explosions in volatile atmospheres.
The Role of Technological Advancement
Technological advancements have introduced sophisticated machinery in mining, which, while increasing efficiency and productivity, also calls for specialized maintenance. The complexity of modern mining equipment demands expert attention and adherence to stringent safety standards, such as those provided by ATEX and HAZLOC certifications. Integrating technology in maintenance routines, such as real-time monitoring systems and predictive maintenance software, can further optimize the maintenance process, reducing unexpected equipment failures and ensuring continuous operation.
Sustainability and Environmental Considerations
Mining operations are increasingly under scrutiny for their environmental impact. Effective maintenance strategies are crucial in minimizing this footprint. Well-maintained equipment operates more efficiently, requires less energy, and reduces emissions, contributing to more sustainable mining practices. Moreover, extending the life cycle of mining equipment through meticulous maintenance routines lowers the need for frequent replacements, leading to reduced material waste and better resource utilization.
In conclusion, the maintenance of mining equipment is a critical practice that serves multiple essential functions. It ensures the efficiency and longevity of machinery, upholds the highest safety standards, leverages technological advancements for improved performance, and contributes to the environmental sustainability of mining operations. For professionals and organizations operating in hazardous environments, adopting rigorous maintenance practices is not just a strategic business decision but a fundamental safety imperative.
Maintenance Strategies: Preventive vs. Predictive
When it comes to optimizing the maintenance of mining equipment, two primary strategies stand out: preventive maintenance and predictive maintenance. Both approaches play a critical role in extending the life cycle of mining equipment, but they do so in distinctly different ways. Understanding the nuances of each strategy is key to implementing a maintenance program that not only prolongs the lifespan of mining equipment but also maximizes safety and efficiency.
Preventive Maintenance
Preventive maintenance is scheduled regularly and aims to keep equipment running smoothly before any problems occur. This approach is akin to the routine check-ups that aim to prevent health issues. By adhering to a predetermined schedule, preventive maintenance tasks are performed on mining equipment, such as inspections, cleaning, lubrication, and parts replacement, regardless of whether signs of wear are evident.
The main advantage of preventive maintenance is that it can significantly reduce the likelihood of equipment failures, hence minimizing unplanned downtime and potentially hazardous situations that could arise from sudden equipment malfunctions. However, performing maintenance tasks too frequently can sometimes lead to unnecessary expense and downtime, making it crucial to balance the frequency of these activities carefully.
Predictive Maintenance
On the flip side, predictive maintenance leverages advanced technologies to monitor the condition of equipment in real-time and predict when maintenance should be performed. This approach uses various tools and techniques, such as vibration analysis, thermography, and fluid analysis, to detect anomalies and signs of wear before they lead to failure.
The primary benefit of predictive maintenance is its ability to optimize maintenance tasks based on the actual condition of the equipment rather than following a fixed schedule. This not only reduces unnecessary maintenance activities and costs but also minimizes the risk of unexpected equipment failures. Predictive maintenance requires a higher initial investment in technology and skills, but it can lead to substantial long-term savings and enhanced safety by preventing equipment breakdowns before they occur.
Combining the Best of Both Worlds
In practice, the most effective maintenance strategy in hazardous environments often involves a combination of both preventive and predictive maintenance. By integrating regular checks and maintenance routines with advanced monitoring and predictive analytics, organizations can ensure that their mining equipment operates reliably and safely while minimizing downtime and maintenance costs.
For industries operating in hazardous environments, such as mining, where safety is paramount, employing a strategy that emphasizes both regular maintenance and advanced prediction can prevent potential disasters before they occur. The Intrinsically Safe Store underscores the importance of this dual approach by offering products that support both preventive and predictive maintenance strategies, ensuring that equipment remains safe and operational without increasing the risk of explosive atmospheres.
Challenges in Mining Equipment Maintenance
Ensuring the longevity and reliability of mining equipment is a cornerstone of operational safety and efficiency in the mining sector. However, maintaining such equipment presents a unique set of challenges, primarily due to the harsh and unpredictable environments in which these machines operate. Understanding these challenges is the first step towards optimizing mining equipment maintenance strategies for extended life cycles.
Harsh Operating Conditions
Mining equipment is routinely exposed to extreme conditions, including dust, moisture, corrosive materials, and significant temperature fluctuations. These elements can lead to accelerated wear and tear, corrosion, and mechanical failures. The abrasive nature of mined materials further exacerbates equipment deterioration, demanding more frequent inspections and maintenance to prevent breakdowns.
Accessibility and Safety Concerns
Mining often occurs in remote and difficult-to-access locations, complicating maintenance efforts. The logistics of transporting heavy machinery parts and specialized repair personnel to these sites can delay essential maintenance work, increasing the risk of equipment failure. Additionally, ensuring the safety of maintenance staff in hazardous environments remains a primary concern, necessitating the use of intrinsically safe and explosion-proof equipment to prevent accidents.
Cost and Time Constraints
Maintenance activities can be costly and time-consuming, requiring significant downtime that reduces productivity. The challenge lies in scheduling maintenance tasks to minimize operational disruptions while ensuring thorough inspections and repairs are conducted. Moreover, the high cost of replacement parts and specialized labor can strain budgets, pushing companies to seek more cost-effective maintenance solutions.
Technological Complexity
Modern mining equipment often incorporates sophisticated technology, including automation and advanced sensor systems. While these advancements enhance efficiency and safety, they also add complexity to maintenance routines. Diagnosing issues with such systems requires specialized knowledge and skills, making it challenging to promptly address malfunctions without impacting mining operations.
Lack of Standardization
The mining industry employs a wide variety of equipment, often from different manufacturers, leading to a lack of standardization in maintenance procedures and parts. This diversity complicates maintenance protocols, as technicians must be familiar with a broad range of equipment specifications and repair techniques. The absence of unified standards can also hinder the efficient organization of maintenance inventories, creating potential delays in obtaining necessary parts.
Addressing these challenges requires a holistic approach to mining equipment maintenance, combining proactive strategies, advanced technologies, and adherence to safety standards. By recognizing the unique obstacles presented by the mining environment, industry professionals can develop more effective maintenance practices that extend the life cycle of critical mining equipment while ensuring the safety and productivity of their operations.
Wear and Tear: Recognizing Equipment Fatigue
Mining equipment maintenance isn’t just about responding to breakdowns and failures; it’s also about proactively recognizing signs of wear and tear to prevent equipment fatigue. This approach is critical in hazardous environments such as mines, where safety is paramount and the risk of an accident can have severe consequences. Recognizing equipment fatigue early can significantly extend the life cycle of mining machinery, ensuring operational efficiency and the safety of personnel.
Wear and tear in mining equipment can manifest in several ways, depending on the type of machinery and the environment in which it operates. Common signs include:
- Increased Vibration: Unusual or excessive vibration in machinery, such as drilling equipment, conveyors, and crushers, can indicate misalignment, imbalanced components, or wear in bearings.
- High Temperature: Components running at higher temperatures than normal can be a sign of friction, inadequate lubrication, or failure of cooling systems, all of which signal wear.
- Unusual Noises: Changes in the operational sounds of equipment, such as grinding, screeching, or banging, can be early indicators of wear or malfunction.
- Decreased Performance: A reduction in efficiency, such as slowing down of production rates or increased fuel consumption, may indicate that components are wearing out and need maintenance or replacement.
It’s crucial for maintenance teams to conduct regular inspections, utilizing both visual checks and sophisticated diagnostic tools, to identify these early signs of wear and tear. For example, vibration analysis and thermal imaging can detect problems invisible to the naked eye, while regular oil and lubricant analyses can provide insights into the internal condition of machinery components.
Implementing a comprehensive predictive maintenance program is invaluable. This strategic approach involves scheduling maintenance based on data-driven projections about when equipment components are likely to fail, rather than reacting to unexpected breakdowns. Predictive maintenance not only helps in avoiding the costs associated with unplanned downtime but also significantly extends the life of mining equipment.
In environments where explosive atmospheres are a constant risk, ensuring that mining equipment is maintained to the highest standards is not just a matter of efficiency but of safety. Using intrinsically safe and explosion-proof equipment, as provided by The Intrinsically Safe Store, can add an additional layer of protection. These devices are designed to operate safely within hazardous conditions, reducing the risk of ignition from equipment fatigue-related failures.
The focus on recognizing and addressing equipment wear and tear is more than just maintaining productivity; it’s about creating a safe working environment for all. With the right approach to mining equipment maintenance, it’s possible to achieve both goals, ensuring that machinery runs efficiently and safely extends its operational life cycle.
Training Personnel for Optimized Maintenance
Ensuring that mining equipment operates efficiently and has an extended life cycle necessitates not only regular maintenance but also a well-trained team. Sophisticated mining machinery, often operating under hazardous conditions, requires precise care to prevent premature wear and tear, downtime, and most critically, accidents that endanger personnel.
Understanding the Importance of Safety
The first step in training personnel for optimized maintenance revolves around inculcating a deep understanding of safety protocols. Given the hazardous environments in which mining equipment operates, emphasis on the use of intrinsically safe and explosion-proof devices cannot be overstated. The Intrinsically Safe Store provides an array of products that are critical in maintaining safety standards during maintenance procedures. Training sessions should cover the usage of such equipment extensively, highlighting how these devices prevent potential ignition sources in explosive atmospheres.
Enhancing Technical Skills
Optimizing mining equipment maintenance requires personnel to possess a robust set of technical skills. This includes understanding the operational mechanics of various mining machinery, the ability to diagnose issues accurately, and executing maintenance practices that adhere to the manufacturer’s guidelines and safety standards like ATEX and HAZLOC. Specialized training modules designed to upgrade the technical skills of maintenance staff are paramount. These modules should cover a range of topics from routine checks and troubleshooting to advanced predictive maintenance techniques.
Implementing a Culture of Continuous Learning
The rapidly evolving nature of mining technology means that maintenance practices also need to keep pace. Implementing a culture of continuous learning within the workforce is essential. Encourage personnel to stay abreast of the latest advancements in mining technology and maintenance methodologies. Providing access to ongoing educational resources, workshops, and seminars can foster a knowledgeable and proactive maintenance team that is well-equipped to handle complex maintenance scenarios efficiently.
Promoting Teamwork and Communication
Effective maintenance is seldom the result of individual effort. It requires a coordinated approach, where information and best practices are shared freely among team members. Training programs should, therefore, emphasize the importance of teamwork and effective communication. Simulation exercises that mimic real-life maintenance scenarios can be particularly beneficial in teaching teams how to work together seamlessly, share critical information, and make collective decisions quickly and accurately.
In conclusion, training personnel for optimized maintenance is a multifaceted process that requires a comprehensive approach. It involves not only equipping teams with the necessary technical skills and safety knowledge but also fostering a culture of continuous improvement and teamwork. By prioritizing these aspects, mining operations can ensure that their equipment is maintained to the highest standards, thereby extending its life cycle and ensuring the safety of all personnel involved.
FAQs: Optimizing Mining Equipment Maintenance for an Extended Life Cycle
How can the use of technology improve mining equipment maintenance?
The use of technology in mining equipment maintenance plays a crucial role in enhancing efficiency, reliability, and safety. Innovative tools and devices, such as intrinsically safe cameras and LED work lights, facilitate thorough inspections and monitoring in hazardous environments without the risk of ignition. Predictive maintenance technologies, including vibration analysis and thermal imaging, allow for early detection of equipment anomalies. This proactive approach minimizes downtime, extends the life cycle of mining equipment, and ensures operational safety.
What metrics should be monitored to assess maintenance effectiveness?
Effectiveness of maintenance operations can be measured using several key performance indicators (KPIs). These include equipment uptime vs. downtime, mean time to repair (MTTR), mean time between failures (MTBF), maintenance costs as a percentage of replacement asset value (RAV), and overall equipment effectiveness (OEE). Monitoring these metrics provides valuable insights into the health and performance of mining equipment, guiding decisions to optimize maintenance strategies.
How does environmental conditions affect mining equipment maintenance?
Environmental conditions in mining operations—such as dust, moisture, extreme temperatures, and the presence of explosive gases—significantly affect maintenance requirements. Equipment operating in such conditions is more susceptible to wear and tear, corrosion, and other forms of degradation. Regular and thorough maintenance schedules adapted to these harsh conditions are crucial to mitigate these effects, ensure equipment integrity, and maintain safety standards compliant with ATEX and HAZLOC requirements.
What is the impact of maintenance on the safety of mining operations?
Proper maintenance of mining equipment is fundamental to ensuring the safety of operations within hazardous environments. Regular and systematic maintenance helps prevent mechanical failures that could lead to dangerous incidents, including explosions. The use of certified intrinsically safe and explosion-proof maintenance tools and equipment further ensures that maintenance activities do not introduce additional hazards. By maintaining equipment in peak condition, the risk of accidents is minimized, protecting personnel and enabling safe, efficient operations.
What software tools are available to assist with mining equipment maintenance planning?
Several software tools are designed to streamline mining equipment maintenance planning and execution. These include computerized maintenance management systems (CMMS), asset management software, and predictive maintenance platforms. These tools offer features such as scheduling maintenance tasks, tracking the history of equipment maintenance, predicting potential failures, and optimizing spare parts inventory. By leveraging these technologies, mining operations can enhance their maintenance practices, improve equipment reliability, and ensure safety compliance.
Our commitment at the Intrinsically Safe Store to providing high-quality, certified safety equipment aligns with the goal of optimizing mining equipment maintenance. By incorporating our intrinsically safe and explosion-proof products into your maintenance routines, you not only extend the life cycle of your equipment but also uphold the highest safety standards.