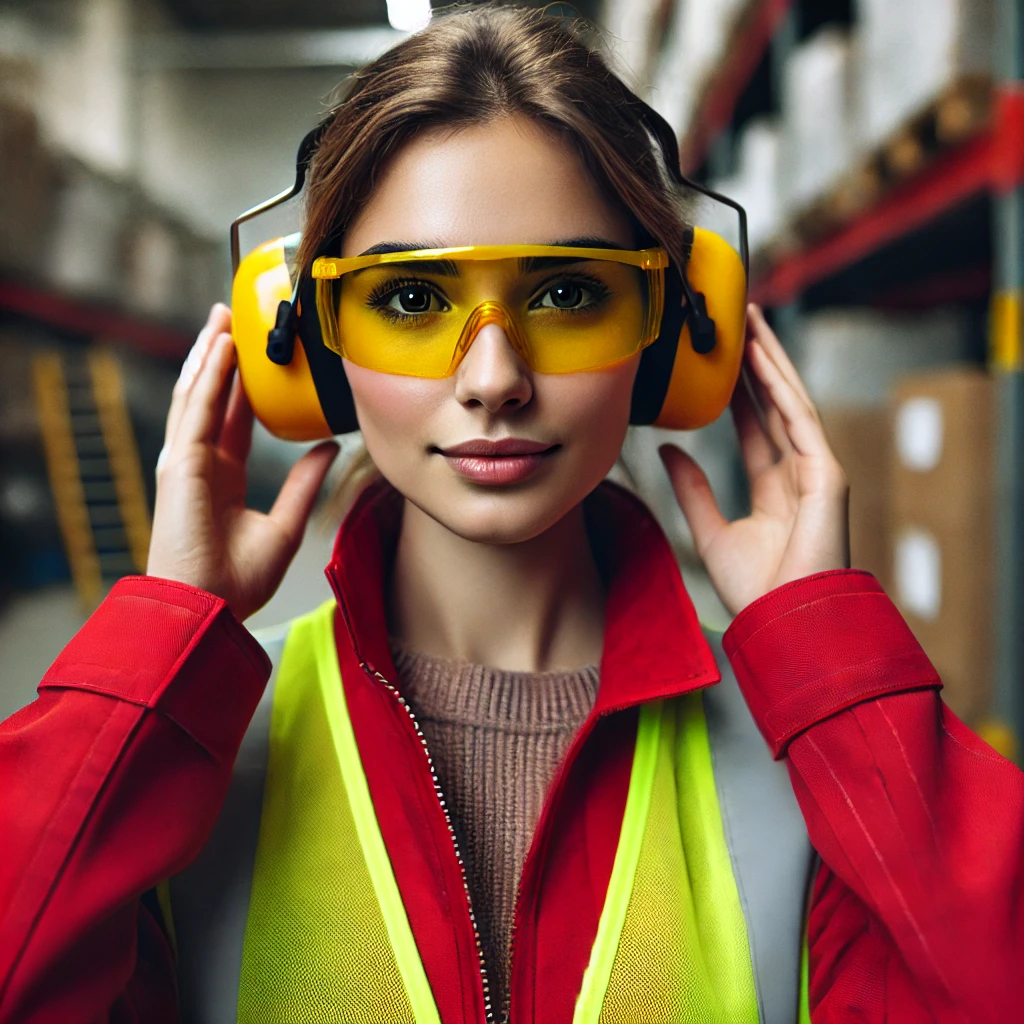
Safety equipment in hazardous areas is a cornerstone of workplace safety, especially in industries where the potential for accidents and exposure to dangerous substances is significant. These environments are often characterized by the presence of flammable gases, vapors, dust, or fibers that can ignite under certain conditions, posing substantial risks to both personnel and property. The primary objective of safety equipment in these settings is to mitigate these risks, ensuring that workers can perform their duties without compromising their health or safety. This comprehensive guide delves into the intricacies of safety equipment in hazardous areas, exploring who should use it, the benefits it offers, and how to effectively implement and source it.
Understanding Safety Equipment in Hazardous Areas
Safety equipment in hazardous areas is a critical component of workplace safety, particularly in industries where the risk of accidents and exposure to dangerous substances is high. These areas are typically defined by the presence of flammable gases, vapors, dust, or fibers that can ignite under certain conditions, posing significant risks to both personnel and property. The primary goal of safety equipment in these environments is to mitigate these risks, ensuring that workers can perform their duties without compromising their health or safety.
The selection and implementation of safety equipment in hazardous areas require a comprehensive understanding of the specific hazards present. This involves a detailed risk assessment to identify potential sources of ignition and the types of hazardous substances involved. Once these factors are understood, appropriate safety measures can be put in place. This might include the use of explosion-proof equipment, which is designed to contain any explosion within the device itself, preventing it from igniting the surrounding atmosphere. Such equipment is typically constructed with robust materials and sealed to prevent the ingress of hazardous substances.
Another critical aspect of safety equipment in hazardous areas is personal protective equipment (PPE). This includes items such as flame-resistant clothing, respirators, and protective eyewear, all of which are designed to protect workers from specific hazards. For instance, in environments where toxic gases are present, respirators equipped with the appropriate filters are essential to prevent inhalation of harmful substances. Similarly, flame-resistant clothing is crucial in areas where there is a risk of fire or explosion, as it can provide a vital layer of protection against burns.
In addition to PPE, safety equipment in hazardous areas often includes gas detection systems. These systems are designed to continuously monitor the atmosphere for the presence of hazardous gases and vapors, providing early warning of potential dangers. Advanced gas detection systems can be integrated with alarm systems, automatically alerting workers and initiating evacuation procedures if dangerous levels of gases are detected. This proactive approach is essential in preventing accidents and ensuring a swift response to potential threats.
Furthermore, communication systems play a vital role in maintaining safety in hazardous areas. Reliable communication is essential for coordinating emergency responses and ensuring that all personnel are aware of potential hazards. In many cases, specialized communication devices are required, as standard equipment may not be suitable for use in explosive atmospheres. These devices are designed to operate safely in hazardous conditions, providing a critical link between workers and emergency response teams.
The implementation of safety equipment in hazardous areas is not a one-time task but an ongoing process. Regular maintenance and testing of equipment are essential to ensure that it remains effective and compliant with safety standards. This includes routine inspections, calibration of gas detection systems, and replacement of worn or damaged PPE. Training is also a crucial component, as workers must be familiar with the proper use and limitations of safety equipment to ensure their effectiveness.
In summary, safety equipment in hazardous areas is a multifaceted approach that involves the use of specialized equipment, personal protective gear, and advanced monitoring systems to protect workers from the inherent risks of these environments. By understanding the specific hazards and implementing appropriate safety measures, industries can create a safer working environment, reducing the likelihood of accidents and ensuring the well-being of their workforce.
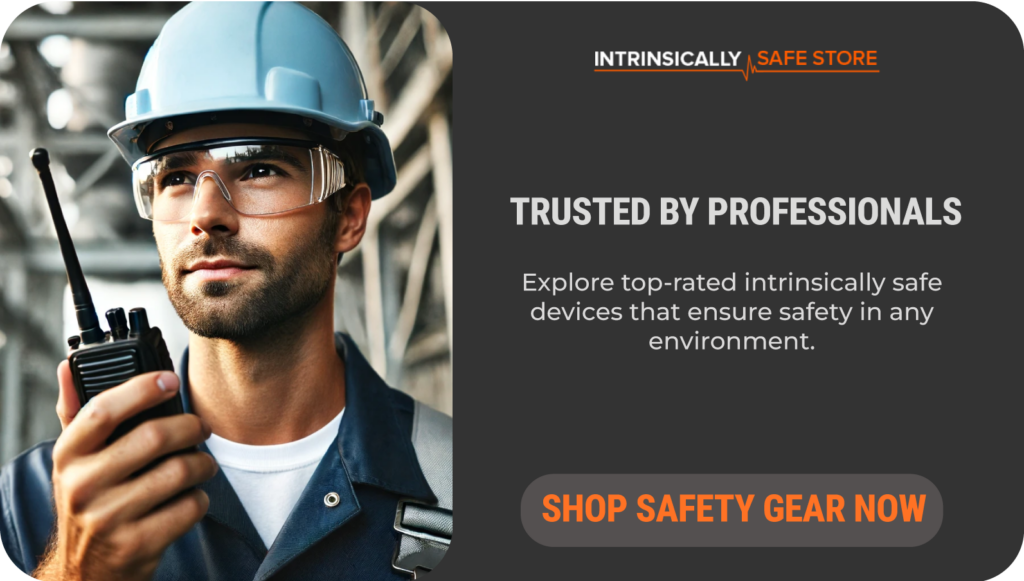
Who Should Use Safety Equipment in Hazardous Areas
In environments where the risk of injury or exposure to harmful substances is high, the use of safety equipment is not just a recommendation but a necessity. The responsibility for using safety equipment in hazardous areas extends beyond a single group of individuals; it encompasses a wide range of professionals and stakeholders who are directly or indirectly involved in operations within these environments. Understanding who should use safety equipment is crucial for maintaining safety standards and ensuring the well-being of everyone involved.
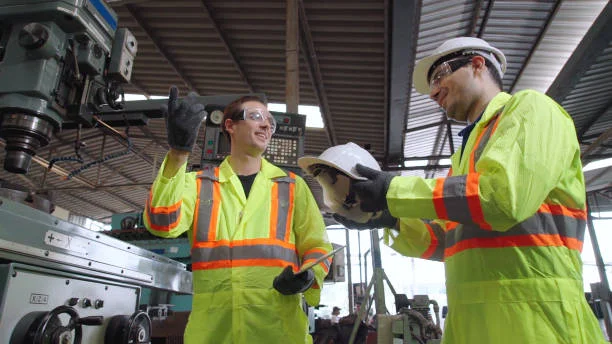
First and foremost, employees who work directly in hazardous areas are the primary users of safety equipment. These individuals include construction workers, chemical plant operators, miners, and laboratory technicians, among others. Their daily tasks often expose them to potential dangers such as toxic chemicals, heavy machinery, and unstable structures. For these workers, safety equipment serves as a critical line of defense against accidents and health hazards. Employers are legally and ethically obligated to provide appropriate safety gear and ensure that their employees are trained in its proper use. This not only protects the workers but also minimizes the risk of workplace incidents that could lead to costly legal repercussions and damage to the company’s reputation.
Supervisors and managers also play a pivotal role in the use of safety equipment in hazardous areas. While they may not be directly involved in the hands-on tasks, their responsibility lies in overseeing operations and ensuring that safety protocols are strictly followed. They must conduct regular safety audits, provide ongoing training, and foster a culture of safety within the organization. By doing so, they help to create an environment where the use of safety equipment is second nature to all employees. Moreover, supervisors are often tasked with the responsibility of selecting the appropriate safety equipment, which requires a thorough understanding of the specific hazards present in their work environment.
Contractors and subcontractors who are brought in for specific projects or tasks within hazardous areas must also adhere to the same safety standards as regular employees. These individuals may not be as familiar with the specific risks associated with a particular site, making it even more critical for them to use safety equipment diligently. Companies must ensure that all external personnel are adequately briefed on safety protocols and equipped with the necessary gear before they commence work. This not only protects the contractors but also ensures that the safety of the entire workforce is not compromised.
Regulatory bodies and safety inspectors, while not directly involved in the day-to-day operations, have a significant influence on the use of safety equipment in hazardous areas. These entities establish the guidelines and standards that dictate what constitutes adequate safety measures. They conduct inspections and audits to ensure compliance, and their findings can lead to improvements in safety practices. Their role is crucial in holding organizations accountable and driving continuous improvement in safety standards.
Finally, the responsibility for using safety equipment extends to the manufacturers and suppliers of the equipment itself. These entities must ensure that their products meet the highest safety standards and are suitable for the specific hazards they are designed to mitigate. They must also provide clear instructions and training materials to ensure that end-users can effectively utilize the equipment.
In summary, the use of safety equipment in hazardous areas is a collective responsibility that involves a diverse group of individuals and organizations. From the workers on the ground to the regulatory bodies overseeing safety standards, each plays a vital role in ensuring that safety equipment is used effectively to protect lives and maintain a safe working environment.
The Main Benefits of Safety Equipment in Hazardous Areas
The implementation of safety equipment in hazardous areas is not merely a regulatory requirement; it is a fundamental aspect of ensuring the well-being of workers and the smooth operation of industrial processes. One of the primary benefits of using safety equipment in such environments is the significant reduction in the risk of accidents and injuries. Hazardous areas, by their very nature, are fraught with potential dangers, including exposure to toxic substances, extreme temperatures, and the risk of explosions. Safety equipment acts as a critical barrier between these hazards and the workers, providing a layer of protection that can prevent minor incidents from escalating into major accidents. For instance, personal protective equipment (PPE) such as helmets, gloves, and protective eyewear can shield workers from physical injuries, while specialized gear like respirators can protect against inhalation of harmful chemicals.
Another crucial benefit of safety equipment in hazardous areas is the enhancement of operational efficiency. When workers feel safe and protected, they are more likely to perform their tasks with confidence and precision. This sense of security can lead to increased productivity, as employees are less likely to be distracted by concerns about their personal safety. Moreover, the use of appropriate safety equipment can minimize downtime caused by accidents or equipment failures. For example, explosion-proof equipment and intrinsically safe devices are designed to operate safely in environments with flammable gases or dust, reducing the likelihood of incidents that could halt production. By maintaining a safe working environment, companies can ensure that their operations run smoothly and efficiently, ultimately contributing to their bottom line.
The presence of safety equipment in hazardous areas also plays a vital role in fostering a culture of safety within an organization. When companies prioritize the health and safety of their employees by investing in high-quality safety equipment, it sends a clear message that they value their workforce. This commitment to safety can boost employee morale and job satisfaction, leading to lower turnover rates and a more engaged workforce. Furthermore, a strong safety culture can enhance a company’s reputation, making it more attractive to potential employees, clients, and partners. In industries where safety is a top priority, having a reputation for maintaining high safety standards can be a significant competitive advantage.
Lastly, the use of safety equipment in hazardous areas is essential for compliance with legal and regulatory requirements. Governments and industry bodies have established stringent safety standards to protect workers and the environment from the risks associated with hazardous areas. Non-compliance with these regulations can result in severe penalties, including fines, legal action, and damage to a company’s reputation. By adhering to safety standards and using the appropriate equipment, companies can avoid these negative consequences and demonstrate their commitment to responsible and ethical business practices. In summary, the benefits of safety equipment in hazardous areas extend beyond mere compliance; they encompass the protection of human life, the enhancement of operational efficiency, the promotion of a positive safety culture, and the safeguarding of a company’s reputation and financial stability.
Safeguarding the Future with Effective Safety Equipment
The implementation of safety equipment in hazardous areas is not merely a regulatory requirement; it is a fundamental aspect of ensuring the well-being of workers and the smooth operation of industrial processes. The benefits of using safety equipment extend beyond mere compliance; they encompass the protection of human life, the enhancement of operational efficiency, the promotion of a positive safety culture, and the safeguarding of a company’s reputation and financial stability. By strategically planning the timing of installations, sourcing equipment from reliable suppliers, and continuously monitoring and evaluating safety protocols, organizations can enhance the effectiveness of their safety measures, protect their workforce, and maintain operational efficiency. As industries continue to evolve and face new challenges, the commitment to safety must remain unwavering, ensuring that the future is safeguarded with effective safety equipment and practices.
For more information on safety equipment and to explore our range of products, visit our store.
Getting Started with Safety Equipment in Hazardous Areas
Embarking on the journey of implementing safety equipment in hazardous areas requires a meticulous approach, as the stakes are incredibly high. The first step is to conduct a comprehensive risk assessment. This involves identifying potential hazards, evaluating the risks associated with them, and determining the necessary safety measures to mitigate these risks. It’s crucial to involve a team of experts who understand the specific challenges of the environment in question. This team should include safety engineers, industrial hygienists, and other relevant professionals who can provide insights into the unique risks present in the area. Their expertise will guide the selection of appropriate safety equipment, ensuring that it meets the specific needs of the environment.
Once the risk assessment is complete, the next step is to select the appropriate safety equipment. This selection process should be guided by the findings of the risk assessment, as well as industry standards and regulations. It’s important to choose equipment that is not only compliant with these standards but also suitable for the specific conditions of the hazardous area. For instance, in environments where explosive gases are present, intrinsically safe equipment that prevents sparks and overheating is essential. Similarly, in areas with high levels of dust, equipment that minimizes dust accumulation and is easy to clean should be prioritized. The goal is to ensure that the equipment not only protects workers but also enhances the overall safety of the environment.
After selecting the appropriate equipment, the next step is to ensure proper installation and maintenance. This involves working with qualified professionals who can install the equipment according to the manufacturer’s specifications and industry standards. Proper installation is critical, as even the most advanced safety equipment can fail if not installed correctly. Regular maintenance is equally important, as it ensures that the equipment remains in optimal working condition. This includes routine inspections, testing, and servicing to identify and address any potential issues before they become serious problems. Maintenance schedules should be established based on the manufacturer’s recommendations and the specific conditions of the hazardous area.
Training is another critical component of getting started with safety equipment in hazardous areas. Workers must be trained on how to use the equipment properly, as well as how to respond in the event of an emergency. This training should be comprehensive and ongoing, with regular refresher courses to ensure that workers remain knowledgeable and confident in their ability to use the equipment effectively. It’s also important to foster a culture of safety within the organization, where workers feel empowered to report potential hazards and suggest improvements to safety protocols.
Finally, it’s essential to continuously monitor and evaluate the effectiveness of the safety equipment and protocols in place. This involves regularly reviewing incident reports, conducting audits, and seeking feedback from workers. By doing so, organizations can identify areas for improvement and make necessary adjustments to enhance safety. This proactive approach not only helps to prevent accidents and injuries but also demonstrates a commitment to the well-being of workers and the overall safety of the environment.
Optimal Timing for Implementing Safety Equipment in Hazardous Areas
Determining the best time to implement safety equipment in hazardous areas is crucial for ensuring the well-being of workers and maintaining operational efficiency. The timing of such implementations can significantly impact the effectiveness of safety measures, the cost of installation, and the overall productivity of the workplace. One of the most critical factors to consider is the nature of the hazardous environment itself. For instance, in industries where conditions are dynamic and constantly changing, such as construction or mining, the timing of safety equipment installation should align with the phases of the project. Installing equipment too early might lead to unnecessary wear and tear or even damage, while installing it too late could expose workers to unnecessary risks.
Seasonal variations also play a significant role in determining the optimal timing for safety equipment installation. In regions where weather conditions fluctuate dramatically, it is essential to consider how these changes might affect both the installation process and the functionality of the equipment. For example, in areas prone to heavy rainfall or snow, it might be more practical to schedule installations during drier months to avoid complications that could arise from adverse weather conditions. Additionally, certain types of safety equipment may require specific environmental conditions to function correctly, such as temperature-sensitive sensors or materials that could degrade in extreme weather. Therefore, aligning the installation schedule with favorable weather conditions can enhance the longevity and reliability of the equipment.
Another critical consideration is the operational schedule of the facility or site. Implementing safety equipment during periods of low activity or scheduled downtime can minimize disruptions to regular operations. This approach not only ensures that the installation process is smooth and efficient but also reduces the risk of accidents occurring during the transition period. For facilities that operate around the clock, it might be necessary to plan installations during off-peak hours or to stagger the implementation process to maintain a balance between safety and productivity. Engaging with stakeholders, including management, safety officers, and workers, can provide valuable insights into the most suitable times for installation, ensuring that the process aligns with the operational needs and safety priorities of the organization.
Furthermore, regulatory requirements and compliance deadlines can influence the timing of safety equipment implementation. Staying informed about industry regulations and upcoming changes in safety standards is essential for ensuring that installations are completed in a timely manner. Proactively planning for these changes can prevent last-minute rushes that might compromise the quality of the installation or lead to non-compliance penalties. Collaborating with regulatory bodies and industry experts can provide guidance on the best practices for timing installations to meet compliance requirements while optimizing safety outcomes.
In summary, the best time to implement safety equipment in hazardous areas is a multifaceted decision that requires careful consideration of environmental conditions, operational schedules, and regulatory requirements. By strategically planning the timing of installations, organizations can enhance the effectiveness of their safety measures, protect their workforce, and maintain operational efficiency.
Navigating the Marketplace for Safety Equipment in Hazardous Areas
When it comes to sourcing safety equipment for hazardous areas, the stakes are incredibly high. The right equipment can mean the difference between a safe working environment and one fraught with risks. Therefore, understanding where to procure these essential tools is crucial for any business operating in potentially dangerous settings. The marketplace for safety equipment is vast and varied, offering a plethora of options that cater to different industries and specific needs. However, navigating this marketplace requires a strategic approach to ensure that the equipment not only meets regulatory standards but also aligns with the unique demands of your work environment.
One of the primary avenues for acquiring safety equipment is through specialized suppliers who focus exclusively on products designed for hazardous areas. These suppliers often have a deep understanding of the specific requirements and challenges associated with such environments. They offer a range of products that are compliant with industry standards and regulations, ensuring that the equipment is both reliable and effective. Engaging with these suppliers can provide businesses with access to expert advice and guidance, helping them make informed decisions about the most appropriate equipment for their needs. Additionally, these suppliers often offer customization options, allowing businesses to tailor equipment to their specific operational requirements.
Another viable option is to explore partnerships with manufacturers who produce safety equipment. Direct engagement with manufacturers can be particularly beneficial for businesses that require large quantities of equipment or have unique specifications that off-the-shelf products cannot meet. Manufacturers can offer insights into the latest technological advancements and innovations in safety equipment, providing businesses with cutting-edge solutions that enhance safety and efficiency. Furthermore, establishing a direct relationship with manufacturers can lead to cost savings, as it eliminates the middleman and allows for more favorable pricing arrangements.
Online marketplaces have also become an increasingly popular source for safety equipment. Platforms such as Amazon Business, Intrinsically Safe Store, Grainger, and Global Industrial offer a wide array of products from various suppliers, providing businesses with the convenience of comparing prices and features from the comfort of their office. These platforms often include customer reviews and ratings, offering valuable insights into the performance and reliability of different products. However, it is essential to exercise caution when purchasing from online marketplaces, as the quality and authenticity of products can vary significantly. Ensuring that the products are certified and meet industry standards is crucial to avoid potential safety hazards.
Trade shows and industry conferences present another opportunity to explore the latest offerings in safety equipment. These events bring together manufacturers, suppliers, and industry experts, providing a platform for businesses to discover new products, network with key players, and gain insights into emerging trends and technologies. Attending these events can be particularly beneficial for businesses looking to stay ahead of the curve and adopt innovative solutions that enhance safety in hazardous areas.
Finally, consulting with industry peers and professionals can provide valuable recommendations and insights into reliable sources for safety equipment. Networking with other businesses operating in similar environments can uncover trusted suppliers and manufacturers, as well as provide firsthand accounts of product performance and reliability. Engaging with industry associations and professional organizations can also offer access to resources and support in navigating the complex landscape of safety equipment procurement.
In summary, sourcing safety equipment for hazardous areas requires a multifaceted approach that leverages specialized suppliers, direct manufacturer relationships, online marketplaces, industry events, and professional networks. By exploring these avenues, businesses can ensure they acquire the most suitable and effective equipment to safeguard their operations and protect their workforce.
Frequently Asked Questions About Safety Equipment in Hazardous Areas
Navigating the complexities of safety equipment in hazardous areas can be daunting, especially when the stakes are high. Ensuring the safety of personnel and the integrity of operations in environments fraught with potential dangers requires a comprehensive understanding of the equipment designed to mitigate these risks. Below, we delve into some of the most frequently asked questions about safety equipment in hazardous areas, providing detailed insights to enhance your knowledge and decision-making processes.
What constitutes a hazardous area?
A hazardous area is any environment where there is a potential risk of fire, explosion, or other dangerous events due to the presence of flammable gases, vapors, dust, or fibers. These areas are commonly found in industries such as oil and gas, chemical manufacturing, mining, and pharmaceuticals. The classification of these areas is typically based on the likelihood and duration of the presence of explosive atmospheres, which is crucial for determining the appropriate safety measures and equipment.
Why is specialized safety equipment necessary in hazardous areas?
Specialized safety equipment is essential in hazardous areas to prevent accidents and ensure the safety of workers. This equipment is designed to withstand and operate safely in environments where conventional equipment might fail or cause ignition. For instance, intrinsically safe devices are engineered to limit electrical and thermal energy to levels that cannot ignite a hazardous atmosphere. This is critical in preventing explosions and ensuring that operations can continue without interruption.
What types of safety equipment are commonly used in hazardous areas?
The range of safety equipment used in hazardous areas is extensive and includes personal protective equipment (PPE), gas detectors, intrinsically safe communication devices, explosion-proof lighting, and ventilation systems. PPE such as flame-resistant clothing, helmets, and gloves protect workers from direct exposure to hazardous substances. Gas detectors are vital for monitoring the presence of flammable or toxic gases, providing early warnings to evacuate or take corrective action. Intrinsically safe communication devices ensure that workers can maintain contact without risking ignition. Explosion-proof lighting and ventilation systems are designed to operate safely in explosive atmospheres, reducing the risk of ignition from electrical sparks or heat.
How is safety equipment certified for use in hazardous areas?
Safety equipment used in hazardous areas must undergo rigorous testing and certification to ensure compliance with international safety standards. Organizations such as the International Electrotechnical Commission (IEC) and the National Fire Protection Association (NFPA) provide guidelines and standards for equipment used in explosive atmospheres. Certification involves testing the equipment’s ability to operate safely under specific conditions and ensuring that it meets the necessary safety requirements. This process is crucial for maintaining safety and preventing accidents in hazardous environments.
What are the key considerations when selecting safety equipment for hazardous areas?
Selecting the right safety equipment for hazardous areas involves several key considerations. First, it is essential to understand the specific hazards present in the environment, including the types of flammable substances and their concentrations. This information helps determine the appropriate equipment and safety measures. Additionally, the equipment must be compatible with the existing infrastructure and operational requirements. Durability, ease of use, and maintenance are also critical factors, as they impact the equipment’s effectiveness and longevity. Finally, ensuring that the equipment is certified and compliant with relevant safety standards is paramount to safeguarding personnel and operations.
Understanding these aspects of safety equipment in hazardous areas is vital for ensuring a safe working environment. By addressing these frequently asked questions, organizations can better equip themselves to handle the challenges posed by hazardous environments, ultimately protecting their workforce and assets.
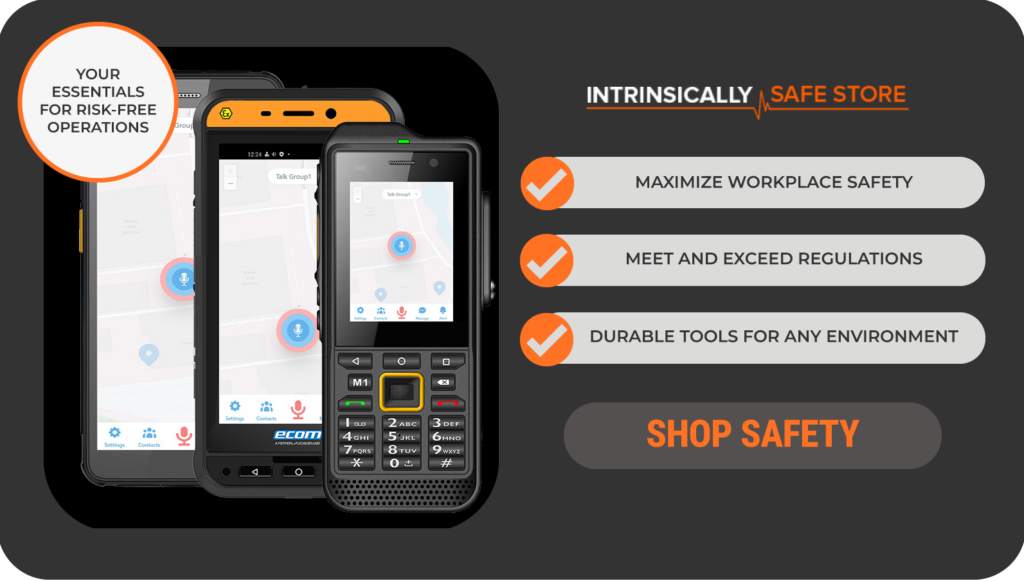