Why Intrinsically Safe Sensors Matter
Hazardous industries such as oil and gas, chemical processing, mining, and pharmaceuticals require specialized equipment to prevent ignition risks. Intrinsically safe (IS) sensors play a crucial role in mitigating explosion hazards by ensuring that electrical and thermal energy levels remain below ignition thresholds. But with numerous options available, how do you choose the right intrinsically safe sensor for your industry?
This guide will walk you through key selection criteria, industry applications, certification standards, and the advantages of using intrinsically safe sensors.
What Are Intrinsically Safe Sensors?
Intrinsically safe sensors are designed to operate in hazardous environments without producing enough energy to ignite flammable gases, vapors, dust, or fibers. Unlike explosion-proof sensors that contain potential explosions within heavy enclosures, intrinsically safe sensors limit electrical and thermal energy at the source.
Selecting the Right Intrinsically Safe Sensor
Choosing the right intrinsically safe sensor depends on your industry’s hazardous classification, measurement needs, certification requirements, and environmental conditions. Investing in properly certified, durable, and reliable sensors ensures workplace safety and regulatory compliance.
For certified intrinsically safe sensors, explore our Intrinsically Safe Store and find solutions tailored to your industry!
Need expert advice? Contact our safety specialists today!
Key Features of Intrinsically Safe Sensors:
- Energy Limitation: Prevents sparks and heat generation above ignition levels.
- Compact and Lightweight Design: Suitable for portable and fixed applications.
- Compliance with Safety Standards: Certified for use in hazardous locations (ATEX, IECEx, NEC, etc.).
- Low Maintenance: No heavy enclosures or cooling mechanisms required.
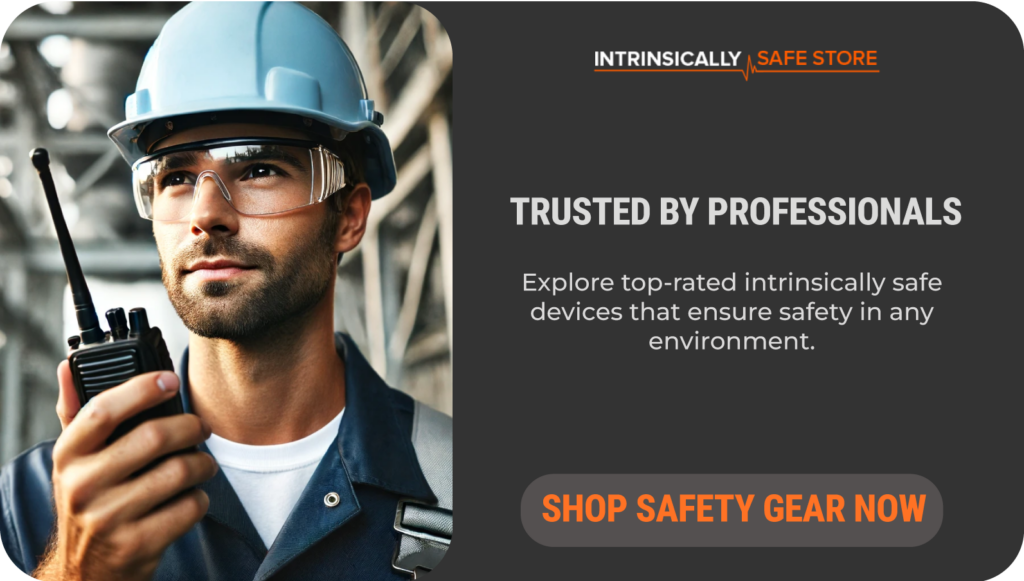
Key Factors to Consider When Choosing an Intrinsically Safe Sensor
1. Hazardous Area Classification
Before selecting a sensor, you must understand the hazardous environment where it will operate. Different industries have specific classifications based on the National Electrical Code (NEC), ATEX, and IECEx standards.
Hazardous Area | Classification System | Example Environments |
---|---|---|
Gases & Vapors | ATEX Zone 0, 1, 2 / NEC Class I | Oil refineries, chemical plants |
Dust & Fibers | ATEX Zone 20, 21, 22 / NEC Class II & III | Grain mills, pharmaceutical facilities |
Mining | ATEX Group I / NEC Class I, Division 1 | Underground mines, coal processing plants |
If your industry requires continuous exposure to hazardous materials, Zone 0 / Class I, Division 1 certified sensors are recommended. For intermittent risks, Zone 1, 2 / Class I, Division 2 sensors may be sufficient.
2. Sensor Type and Measurement Needs
Intrinsically safe sensors come in various types, depending on what they measure. Consider your application when selecting a sensor:
Sensor Type | Application | Industry |
---|---|---|
Temperature Sensors | Monitor heat levels in hazardous areas | Oil & Gas, Chemical Processing |
Gas Detection Sensors | Detect explosive or toxic gases | Mining, Petrochemicals |
Pressure Sensors | Ensure safe pressure levels in pipelines & tanks | Manufacturing, Oil & Gas |
Level Sensors | Monitor liquid levels in hazardous tanks | Wastewater, Pharmaceuticals |
Vibration Sensors | Detect faults in rotating machinery | Heavy Equipment, Aerospace |
Choosing the wrong sensor type can result in operational inefficiencies and safety risks, so always assess your measurement needs before purchase.
3. Certification and Compliance
Certifications ensure that the sensor meets global safety standards. Look for:
- ATEX Certification (Europe): Required for equipment used in explosive atmospheres.
- IECEx Certification (Global): Recognized worldwide for hazardous environment compliance.
- NEC (NFPA 70) & UL (North America): Defines safety for electrical equipment in classified locations.
- CSA (Canada): Verifies compliance with Canadian safety regulations.
If your facility operates across multiple regions, IECEx-certified sensors provide broader compliance.
4. Material and Durability
Hazardous environments expose sensors to corrosive chemicals, extreme temperatures, dust, and moisture. Choosing a sensor with the right material ensures long-term durability and reliability.
Material | Best for |
---|---|
Stainless Steel (316L) | Corrosive environments (chemical plants, marine applications) |
Aluminum Alloy | Lightweight applications (portable sensors) |
Polycarbonate / FRP | Non-metallic, lightweight, and corrosion-resistant |
Explosion-proof enclosures are not required for intrinsically safe sensors, but robust housing is still recommended for harsh environments.
5. Power Supply and Connectivity
Consider whether your sensor will be battery-powered, wired, or wireless.
- Battery-Powered Sensors: Ideal for portable and remote monitoring applications.
- Wired Sensors (4-20mA, Modbus, HART): Ensure stable, long-distance communication in industrial settings.
- Wireless Sensors (LoRa, Bluetooth, Wi-Fi): Reduce installation costs but may require additional approvals for hazardous areas.
Pro Tip: If using wireless intrinsically safe sensors, ensure they meet ISA100.11a or WirelessHART standards for hazardous environments.
Industry-Specific Sensor Recommendations
Industry | Recommended Sensor | Why? |
---|---|---|
Oil & Gas | Gas Detection Sensor | Detects methane, hydrogen sulfide, and VOCs |
Pharmaceuticals | Humidity & Temperature Sensor | Ensures controlled production conditions |
Chemical Processing | pH & Conductivity Sensor | Prevents hazardous chemical reactions |
Mining | Vibration Sensor | Monitors heavy machinery for failures |
Food & Beverage | Level Sensor | Prevents overflows and contamination risks |
Frequently Asked Questions (FAQs)
What is the difference between intrinsically safe and explosion-proof sensors?
Intrinsically safe sensors prevent ignition by limiting energy levels, while explosion-proof sensors contain potential explosions within rugged enclosures.
Can intrinsically safe sensors be used in all hazardous zones?
No. Some sensors are rated only for Zone 1 / Division 2, while others are designed for Zone 0 / Division 1 environments. Always check certification labels before use.
Do intrinsically safe sensors require special installation?
Yes. They require IS barriers or isolators to ensure electrical signals do not exceed safe energy limits.
How do I maintain intrinsically safe sensors?
- Perform regular inspections for physical damage.
- Ensure wiring and connectors remain intact.
- Use certified replacement parts to maintain compliance.
Can I use a regular sensor in a hazardous environment if it’s enclosed in an explosion-proof case?
No. Explosion-proof enclosures prevent external ignition, but they do not make standard sensors intrinsically safe.
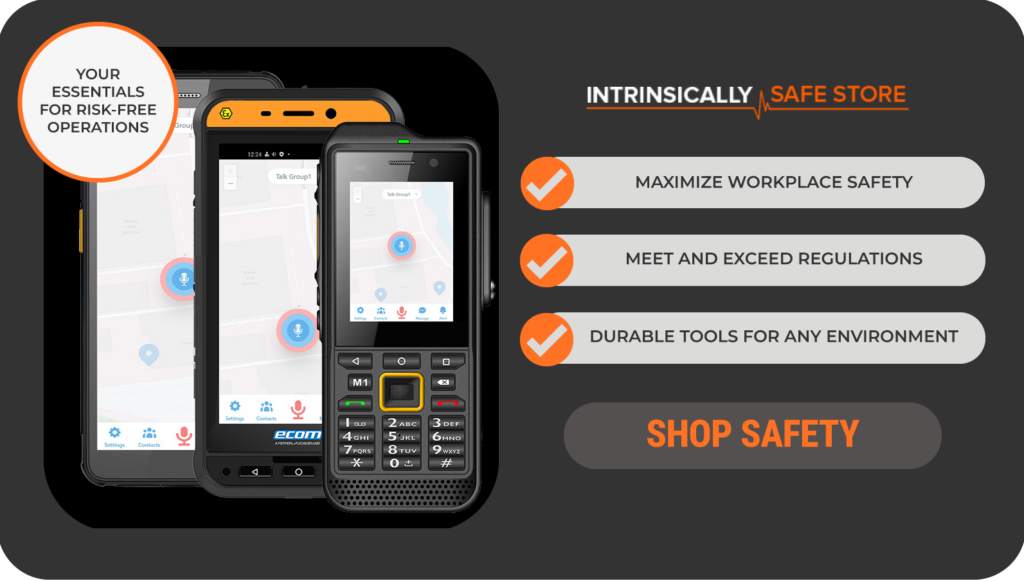