
In industries like oil and gas, chemical processing, and mining, maintaining safety in hazardous zones is paramount. Flammable gases, vapors, or dusts can pose severe risks if electrical equipment generates enough energy to cause ignition. This is where intrinsically safe barriers come into play. These safety devices are engineered to limit energy transfer, ensuring that even in fault conditions, the energy remains insufficient to ignite hazardous substances.
This guide explores how intrinsically safe barriers work, the various types available, how they ensure compliance with ATEX and IECEx regulations, and why they are essential for circuit protection in hazardous zones.
What is an Intrinsically Safe Barrier?
An intrinsically safe barrier is a device that limits the electrical energy—both voltage and current—that can be transferred to hazardous zones. The primary function is to ensure that the energy remains below the ignition threshold for flammable substances, thereby preventing any accidental sparks or heat from triggering an explosion.
Key Components of Intrinsically Safe Barriers:
- Zener Diodes: Clamp voltage levels, ensuring they don’t exceed safe limits.
- Resistors: Limit current flow to prevent the possibility of excessive energy transfer.
- Fuses: Act as a final safeguard by breaking the circuit in the event of an overload or fault.
By utilizing these components, intrinsically safe barriers provide a reliable safety solution, ensuring that electrical systems remain safe even under fault conditions.
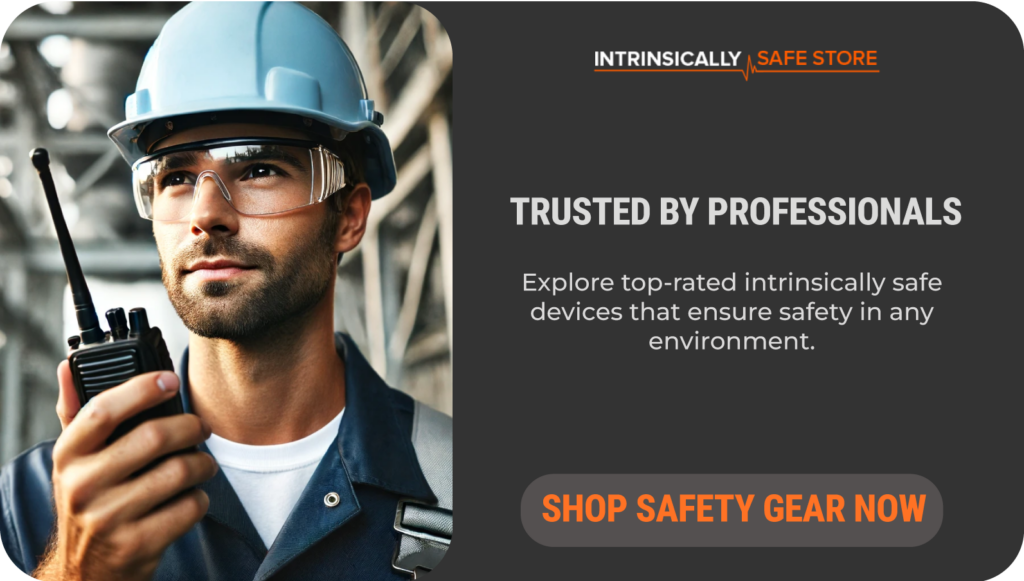
How Do Intrinsically Safe Barriers Work?
Intrinsically safe barriers are installed between the hazardous area and the control system. Their main role is to:
- Limit Energy: Prevent electrical faults (like short circuits or over-voltages) from transmitting sufficient energy to cause ignition.
- Redirect Excess Energy: Ground the excess energy safely, preventing it from reaching hazardous areas.
- Maintain Circuit Integrity: Even if a fault occurs, the barrier ensures that electrical energy is discharged in a controlled, safe manner.
For instance, if an overvoltage occurs, the Zener diode within the barrier will redirect this excess energy to the ground. Simultaneously, resistors will restrict the flow of current to safe levels, and fuses will act as a fail-safe by cutting off the circuit if necessary.
Types of Intrinsically Safe Barriers
Understanding the types of barriers is essential for selecting the right solution for hazardous areas.
1. Zener Barriers
- Working Principle: Use Zener diodes, resistors, and fuses to limit voltage and current. They require a reliable earth ground to function properly.
- Applications: Suitable for simple, cost-effective systems where a solid grounding system is already in place.
- Advantages:
- Lower initial cost.
- Simple installation process.
- Limitations:
- Dependence on a reliable grounding system.
- Can be vulnerable to ground loop interference.
2. Isolated Barriers (Galvanic Isolators)
- Working Principle: Provide complete isolation between the control system and hazardous area circuits. They use transformers, opto-isolators, or capacitors to prevent direct electrical contact.
- Applications: Ideal for complex systems where signal integrity is crucial or where grounding is unreliable.
- Advantages:
- No need for a grounding system.
- Reduces noise and interference.
- Greater signal integrity.
- Limitations:
- Higher initial cost.
- More complex to install.
Unsure about which barriers are right for your industry? Schedule a consultation with our experts.
Comparison Table: Zener vs. Isolated Barriers
Feature | Zener Barrier | Isolated Barrier |
---|---|---|
Installation Cost | Lower | Higher |
Grounding Required | Yes | No |
Noise Resistance | Susceptible to ground loops | Excellent noise rejection |
Maintenance | Requires regular grounding checks | Minimal once installed |
Signal Integrity | Limited in noisy environments | High integrity in all conditions |
Recommended For | Simple, low-budget applications | Complex or critical signal environments |
The Importance of Intrinsically Safe Barriers for ATEX and IECEx Compliance
Hazardous area regulations are stringent, and compliance is critical for both legal and safety reasons.
ATEX Certification
- Applicable within the European Union.
- Ensures that equipment is safe for use in explosive atmospheres.
- Categorizes hazardous zones based on the presence of flammable gases or dust.
IECEx Certification
- An international standard accepted worldwide.
- Ensures that equipment, including barriers, meets global safety requirements for hazardous environments.
How Intrinsically Safe Barriers Support Compliance:
- Energy Limitation: Prevents equipment from exceeding the energy levels that could ignite hazardous substances.
- Fault Protection: Ensures that even under fault conditions, circuits cannot release enough energy to cause an explosion.
- Certification Readiness: Products like intrinsically safe barriers must be ATEX and IECEx certified to ensure operational safety.
By installing certified intrinsically safe barriers, companies ensure they meet regulatory standards and mitigate the risk of non-compliance penalties.
Installation Best Practices for Intrinsically Safe Barriers
- Understand Zone Classifications: Install barriers based on zone classifications, ensuring each barrier is certified for its respective hazardous zone.
- Verify Grounding (for Zener Barriers): Ensure the ground connection is secure and properly tested. Poor grounding can compromise safety.
- Correct Barrier Selection: Choose between Zener or isolated barriers depending on system complexity, budget, and grounding availability.
- Routine Maintenance: Inspect barriers regularly to ensure they remain functional and compliant with regulations.
- Proper Documentation: Keep detailed records of all installations, inspections, and maintenance for compliance audits.
Discover our range of certified intrinsically safe barriers designed to limit energy transfer and protect against ignition risks. Ensure compliance with ATEX and IECEx standards while enhancing operational safety.
Common Applications of Intrinsically Safe Barriers
- Oil & Gas Platforms: Protect circuit integrity in environments with explosive gases.
- Chemical Plants: Safeguard sensors and actuators handling volatile chemicals.
- Mining Operations: Prevent ignition risks in underground operations.
- Pharmaceutical Industry: Protect circuits in zones with combustible dust.
- Food & Beverage Production: Ensure safety where dust or vapor hazards exist.
FAQs About Intrinsically Safe Barriers
What is the main purpose of an intrinsically safe barrier?
The primary purpose is to limit electrical and thermal energy in hazardous zones, ensuring it remains below ignition levels, even under fault conditions.
How do I choose between Zener and isolated barriers?
Choose Zener barriers for simpler, grounded systems where cost is a concern. Opt for isolated barriers when higher signal integrity is required or when grounding is unreliable.
Do intrinsically safe barriers require maintenance?
Yes, especially Zener barriers, which depend on a solid grounding system. Regularly check grounding connections and barrier functionality.
Are intrinsically safe barriers mandatory for ATEX compliance?
Yes. Any equipment used in hazardous zones must comply with ATEX standards, and barriers are critical for maintaining safe energy levels.
Can I use the same barrier for different types of hazardous zones?
No. Barriers are rated for specific zones and types of hazards (e.g., gas vs. dust). Always verify certification before installation.
How often should barriers be tested?
Regular inspections should occur every 6-12 months or as specified by the manufacturer and regulatory guidelines.
What happens if an intrinsically safe barrier fails?
If a barrier fails, it can lead to excessive energy reaching hazardous zones, risking ignition. This is why regular testing and maintenance are crucial.
Conclusion
Intrinsically safe barriers are essential for ensuring the safety of electrical systems in hazardous environments. By limiting energy transfer and adhering to international standards like ATEX and IECEx, these barriers play a pivotal role in protecting personnel, assets, and operations.
Whether you choose Zener or Isolated barriers, the key is proper installation, routine maintenance, and ensuring compliance with regulatory standards.
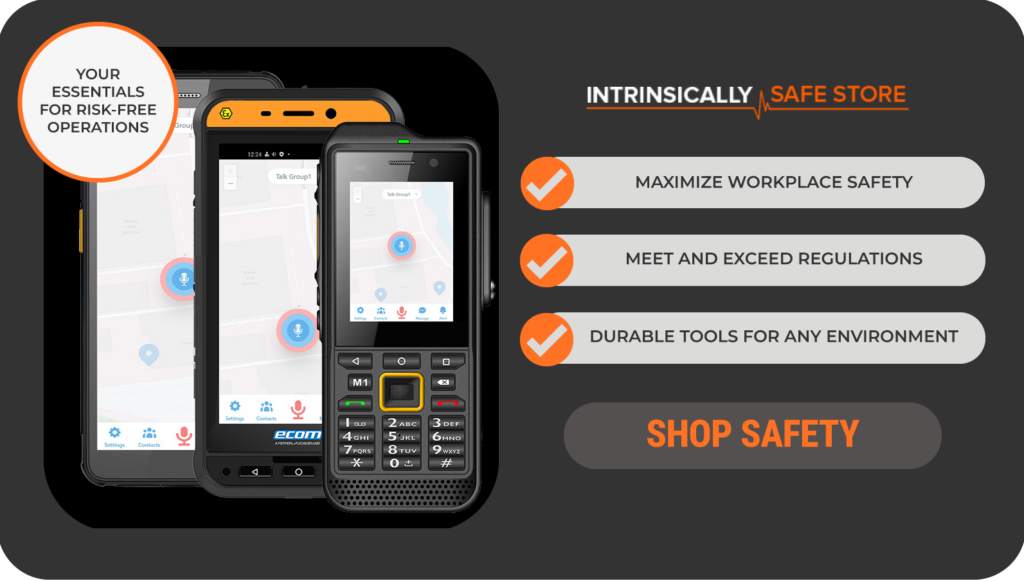