Industrial fans usually handle different types of solids and gases, some of which are flammable. When these combustible materials are present in an environment in high concentrations, they may ignite and cause an explosion. As such, you want to install an explosion proof fan if you operate in a dangerous area where flammable particles or gases are in the air or passing through ventilation systems.
Defining an Explosion Proof Fan
An explosion proof fan is a ventilation device with sufficient protection to contain an internal blast on exposure to a combustible airstream. Proofing such a system means providing a physical/mechanical construction to prevent an explosion from spreading externally and causing harm or damage in the area around it. Users or buyers of hazard area ventilation systems are responsible for selecting the appropriate explosion proof blower or fan for their operating environment.
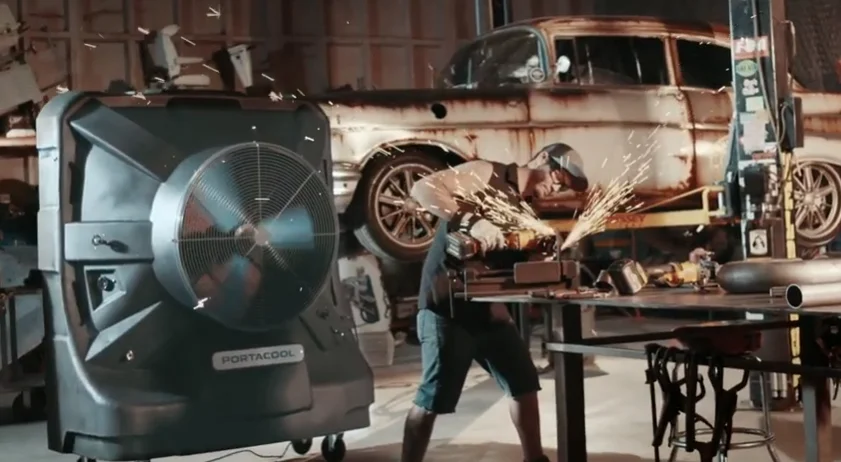
The main difference between an Explosion Proof fan and a traditional fan is that the latter is not safe for use in areas that the National Fire Protection Association (NFPA) has designated as dangerous or hazardous. The device’s electrical circuitry is not designed to prevent sparking, arcs, heating, and other factors that may ignite an explosive mixture in the air. Also, the mechanical construction of such a fan cannot contain an explosion within itself. Therefore, installing a non-Explosion Proof -rated fan is dangerous in operations or facilities such as petrochemical, combustible fluid storage containers, chemical room ventilation systems, paint booth exhaust systems, and gunpowder manufacturing or storage.
Difference Between Explosion Proof and Intrinsically Safe Fan
An intrinsically safe fan that’s also explosion proof is the ideal solution to the risk of igniting a combustible mixture in a hazardous environment. However, intrinsic safety and Explosion Proof differ in significant ways.
A fan has an Explosion Proof rating if, without coming apart, it can contain an explosion originating within itself. Its internal electrical components, such as the motor, must be cushioned such that sparks or arcs coming from within cannot escape into the environment and ignite potentially explosive fibers, gases, or moisture. It’s imperative to note that a fan installed in a hazardous area is continuously or occasionally in the path of possibly flammable mixtures, so, an Explosion Proof construction must ensure that the device’s electrical components do not come into contact with any surrounding combustible elements in concentrations high enough for ignition.
On the other hand, an Intrinsically Safe fan is built to prevent an explosion from occurring on exposure to a combustible airstream. Typically, the product comes with built-in anti-sparking characteristics based on the design of its electrical parts and circuit.
Spark Proof Fan Design Considerations
A high-quality explosion proof inline exhaust fan boasts several design characteristics that help to minimize the risk of internal sparking. The industry standard that most manufacturers follow when designing and building such a fan is the Air Movement and Control Association International (AMCA). Here are the three AMCA designations for a spark resistant construction:
Type A
The standard requires all airstream components in an Explosion Proof fan to be nonferrous. A common material for this application is aluminum because it’s spark resistant. However, any contact between the metal and rusty steel may create sparks. As such, end users should appropriately coat any steel surfaces that the fan may rub on to prevent rusting. This construction type also minimizes the risk of contact between the fan’s spinning wheel and fixed parts.
Type B
This specification requires a spark-resistant impeller. A nonferrous material is used to make the rubbing ring around the opening through which the shaft enters the device’s housing. The construction must ensure that the shaft, bearings, and impeller cannot shift. As such, engineers should implement a restraining mechanism that prevents the axial or lateral movement of these fan components.
Type C
The standard takes into account the possibility of two ferrous fan parts moving during operation. In that case, any such parts must not come into contact with each other.
With that said, all fan components must be grounded to get rid of static electricity, which can create an arc or spark. Sparking inside a fan is dangerous if an airstream containing combustible substances is present. That’s a critical requirement, even if the ventilation device is constructed using a spark-resistant material, such as fiber reinforced plastic.
Also, engineers do well to ensure all electrical components, bearings, or drive parts are not placed in the airstream unless their construction prevents ignition of any surrounding flammable vapors or gases in the event of equipment failure. Enclosing these fan parts enhances overall safety too.
Intrinsic Safety and NEC Standards
A small explosion proof exhaust fan may have a spark-resistant physical design, but that does not necessarily make it 100 percent intrinsically safe. Its electrical engineering must also meet industry standards, especially in line with National Electric Code (NEC) specifications.
The most critical electrical part of a hazardous area fan is the motor. The internal component is not intrinsically safe unless its circuitry is built not to heat up beyond the temperature specified for its operating conditions as per NEC location classifications. Non-sparking materials should be used to make this type of fan motor.
For example, an Explosion Proof motor for use in a location designated as Class 1, Division 1, Group A (which contains flammable gases like acetylene) should have tighter tolerances and extended flame paths. The device’s surface temperature must not reach levels dangerous enough to ignite combustible gases in the atmosphere. As per Class 1 Div 2 directives, the unit must be designed to minimize the risk of igniting an explosive mixture in the air where the danger is only present during abnormal operating conditions.
Be sure to take into account the type of hazard in your facility to identify an appropriate rating for your Explosion Proof or Intrinsically Safe fan. Hydrogen and ethylene are in NEC Group B and International Electrotechnical Commission (IEC) Group IIC, while hydrogen sulfide is in NEC and IEC Groups C and IIB respectively. Propane and gasoline are NEC and IEC Groups D and IIA respectively.
Wrapping it Up
An explosion proof fan is ideal for use in operations or industries that have combustible gases or vapors in the air. Such a unit has a sturdy construction and enclosures that enable it to contain an internal explosion without itself exploding. Its intrinsically safe design includes spark-resistant characteristics and electrical components with low surface temperatures. As such, the device is incapable of causing an explosion including when exposed to a flammable airstream. At Intrinsically Safe Store, we offer different types of hazardous area certified equipment. Visit our store to check out our extensive range of certified products!