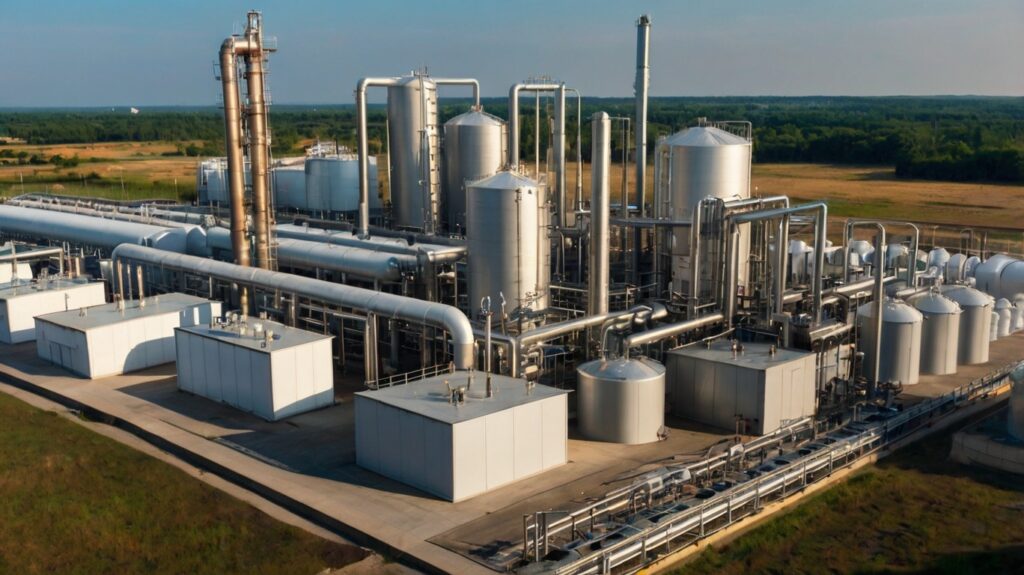
- Intrinsically Safe equipment limits energy to prevent ignition, while Explosion Proof devices contain potential internal explosions.
- Industry-specific needs determine the preference between mobility of Intrinsically Safe gear and the robustness of Explosion Proof solutions.
- Certification and understanding of operational environments are crucial for selecting appropriate safety measures.
The Key Differences Between Intrinsically Safe and Explosion Proof
In hazardous environments such as oil and gas industry sites, chemical plants, and similar high-risk areas, safety is not just a protocol—it’s a critical requirement. Choosing the right kind of safety equipment is paramount to ensure the well-being of those who operate within these environments. Two primary terms emerge when discussing equipment designed to mitigate risks in these dangerous settings: Intrinsically Safe and Explosion Proof. Though both are designed to prevent ignition in explosive atmospheres, they represent fundamentally different approaches and technologies. Understanding the distinctions between intrinsically safe and explosion-proof solutions is essential for selecting the correct equipment for specific environments. This article, brought to you by the expertise of Intrinsically Safe Store, aims to delineate the key differences between these concepts, emphasizing the importance of using certified safe solutions in hazardous areas. With our commitment to ensuring safety and our status as a trusted provider of industry-certified gear, we underscore the necessity of informed decision-making when it comes to protecting lives and properties.
Exploring Explosion Proof Equipment
When delving into the world of safety equipment for hazardous environments, “Explosion Proof” is a term that often emerges alongside “Intrinsically Safe.” Both are designed for use in volatile settings, but their approaches to safety are fundamentally different. Understanding the characteristics of Explosion Proof equipment is crucial for selecting the right kind of protection in environments where explosive gases, dust, or fibers might be present.
Explosion Proof equipment is designed to contain any explosion originating within its housing and to prevent sparks from within its enclosure from igniting vapors, gases, dust, or fibers in the surrounding air. This kind of protection is achieved through robust, heavy enclosures that can withstand an internal explosion without rupturing. The construction of Explosion Proof equipment must be such that, if an explosion were to occur inside an apparatus, the device itself would contain the explosion and prevent the ignition of the external environment. This capability is paramount in areas where hazardous materials are processed or stored, and where any source of ignition could lead to catastrophic consequences.
The term “Explosion Proof” does not imply that the equipment can withstand an external explosion; rather, it means that the device is capable of preventing an internal spark or explosion from causing a much larger blast. These devices are extensively tested to meet rigorous standards and certifications, ensuring they can perform under specific conditions. For sectors such as the oil and gas industry, chemical manufacturing, and others that operate in potentially explosive atmospheres, Explosion Proof equipment is a critical component of their safety protocols.
It’s important to note that Explosion Proof devices are often larger, heavier, and more costly due to the complexity and materials required to construct them safely. This makes them less suited for applications where size, weight, or cost is a significant concern but does not diminish their value in environments where their robust protection against internal explosions is necessary.
In contrast to Intrinsically Safe equipment, which is designed to limit energy available for ignition, Explosion Proof apparatuses take a more defensive approach by ensuring they can contain and isolate explosions within their structure. Both strategies are effective in mitigating risk, but the choice between Intrinsically Safe vs Explosion Proof equipment should be guided by the specific needs of the environment and the nature of the hazardous materials involved.
Employing Explosion Proof equipment offers peace of mind, knowing that even in the event of a failure that could lead to an internal explosion, the risk of igniting a potentially explosive atmosphere is minimized. This level of safety assurance is why organizations operating in hazardous areas prioritize the use of certified Explosion Proof devices as part of their comprehensive safety protocols.
In conclusion, while Intrinsically Safe Store specializes in products designed to prevent ignition in explosive atmospheres, understanding the role and benefits of Explosion Proof equipment is essential for those working in hazardous environments. The key is to ensure that the safety gear and equipment employed are certified and suitable for the specific nature of the hazardous areas in question.
Discover Certified Safe Solutions for Your Hazardous Environment
Navigating the hazardous environments of the oil and gas industry, chemical plants, and other high-risk sectors requires not just expertise but the right safety gear and equipment. Choosing between Intrinsically Safe and Explosion Proof solutions can often be the line between safety and potential disaster. At Intrinsically Safe Store, we are dedicated to your safety and well-being by providing certified safe solutions that meet industry standards and beyond.
- Explore Our Wide Range of Intrinsically Safe Products: From iPad cases that protect your tech in explosive atmospheres to natural gas detectors that ensure you’re always aware of potential hazards, our products are designed with your safety in mind.
- Learn With Us: Visit our comprehensive knowledge base and blog for educational resources that can help you understand the nuances of Intrinsically Safe vs Explosion Proof products, and why it’s crucial to choose the right solution for your needs.
- Stay Safe in Hazardous Areas: With our top-rated safety gear and equipment, confidently navigate your work environment knowing your safety is backed by certified solutions.
Visit us at the Intrinsically Safe Store, and let us help you make informed decisions for your safety in hazardous environments. Your safety is our priority, and it’s why we offer the best in certified safe solutions.
Fundamental Principles of Intrinsically Safe Design
When deciphering the features that distinguish intrinsically safe apparatus from explosion-proof configurations, understanding the fundamental principles of intrinsically safe design is imperative. At its core, intrinsically safe design aims to mitigate the risk of ignition in hazardous environments by limiting the energy—electrical and thermal—available for ignition to below the level that can ignite the specific hazardous atmosphere.
Energy Limitation
This principle is paramount in intrinsically safe design. By rigorously controlling the electrical energy within the device, such as voltage and current, the design ensures that even under fault conditions, the energy released cannot be sufficient to ignite the hazardous atmosphere. This not just pertains to normal operation but also considers the device’s conditions under fault, thereby providing an added layer of safety.
Environmental Consideration
Intrinsically safe devices are designed with the hazardous environment in mind. This entails not only the device’s operational functionality but also its durability and reliability in potentially corrosive or extreme conditions often found in industries such as oil and gas or chemical processing. The design process incorporates an understanding of the specific gases, dust, or fibers present in the environment and tailors the safety mechanisms accordingly.
Component Selection and Integration
Every component within an intrinsically safe device is selected based on its ability to operate within the defined safe energy parameters. Moreover, the integration of these components is carried out in a manner that maintains the overall integrity of the safety design. This meticulous process ensures that the device, as a whole, adheres to the intrinsic safety standards set forth by regulatory bodies.
Safety Certifications
For a device to be deemed intrinsically safe, it must undergo rigorous testing and certification processes by recognized standardization bodies. These certifications confirm that the device meets the strict criteria for energy limitation, environmental protection, and safe operation within hazardous areas. The Intrinsically Safe Store, for instance, strictly offers products that have undergone such certification processes, ensuring that the devices not only align with safety guidelines but also with the practical needs of industries operating in hazardous environments.
Understanding these principles provides a solid foundation for recognizing the critical role that intrinsically safe devices play in maintaining operational safety in hazardous environments. It underscores the commitment of organizations like the Intrinsically Safe Store to the provision of certified safe solutions, designed with the well-being and safety of their users in high-risk areas as the paramount concern.
Certification Standards for Intrinsically Safe Devices
Understanding the certification standards for intrinsically safe devices is crucial for individuals and organizations operating in hazardous environments. These certifications ensure that the equipment meets rigorous safety criteria, designed to prevent ignition and ensure the safety of workers in potentially explosive atmospheres.
The certification process for intrinsically safe devices involves a thorough examination and testing of the equipment to verify that it does not contain enough energy to cause ignition of a flammable atmosphere under both normal and fault conditions. This process is carried out by recognized certification bodies, which assess the devices according to international standards.
One of the key standards for intrinsically safe equipment is the ATEX Directive (Atmosphères Explosibles) in Europe, which provides the framework for equipment intended for use in potentially explosive atmospheres. The ATEX Directive categorizes equipment into different groups and categories, depending on the nature and severity of the environment in which they can be safely used.
In North America, the National Electric Code (NEC) Article 500 defines the requirements for electrical equipment and installations in hazardous (classified) locations. The NEC, along with standards from organizations such as Underwriters Laboratories (UL) and the Canadian Standards Association (CSA), provides certification for intrinsically safe devices based on the specific hazardous environment classifications.
Another important standard is the International Electrotechnical Commission’s IECEx system, which facilitates international trade in equipment and services for use in explosive atmospheres, while maintaining the required level of safety. Equipment certified under the IECEx system meets a set of standards that are accepted in many countries, simplifying the certification process for manufacturers and ensuring safety across borders.
For organizations and individuals in hazardous industries, choosing devices with the appropriate certification is not just a regulatory requirement—it’s a fundamental aspect of maintaining a safe working environment. The Intrinsically Safe Store specializes in providing a range of products that not only meet but exceed these certification standards, ensuring the highest level of safety and compliance for our customers operating in dangerous conditions.
By prioritizing certified intrinsically safe devices, businesses can safeguard their operations against the risks of explosions and fires, protect their employees, and ensure compliance with safety regulations, reflecting our company’s commitment to offering top-rated safety gear and equipment for hazardous areas.
Certification Standards for Explosion Proof Equipment
When it comes to ensuring the utmost safety in hazardous environments, understanding the certification standards for explosion proof equipment is crucial. These standards provide the framework for evaluating and certifying equipment as safe for use in explosive atmospheres, where flammable gases, dusts, or fibers may create a risk of ignition.
One of the key global standards for explosion proof certification is the ATEX directive, which is mandatory for equipment used in explosive atmospheres within the European Union. The ATEX directive categorizes equipment into groups and categories based on the environment in which they can safely operate. Equipment marked with an ‘Ex’ symbol meets these rigorous ATEX standards, indicating it has been designed and manufactured to prevent ignition and withstand explosions.
In the United States, the National Electric Code (NEC) Article 500 and the Occupational Safety and Health Administration (OSHA) provide the regulatory framework for explosion proof equipment. The NEC defines hazardous locations and classifies them according to the type of hazardous material present, guiding the appropriate selection of explosion proof equipment.
Underwriters Laboratories (UL) and Factory Mutual (FM) are two prominent certification bodies in the U.S. that test and certify equipment for use in hazardous locations. Equipment that is UL or FM approved has undergone rigorous testing to ensure it can safely operate in explosive or flammable atmospheres without igniting a fire or explosion.
It is essential for individuals and organizations operating in hazardous environments to understand these certification standards and ensure that their explosion proof equipment meets the required criteria. Utilizing certified explosion proof equipment not only helps to protect the well-being of workers and the facility but also complies with regulatory requirements, avoiding potential legal and financial penalties.
By choosing equipment that adheres to these recognized certification standards, businesses can demonstrate their commitment to safety and reliability. The Intrinsically Safe Store specializes in offering equipment that meets these rigorous certification standards, ensuring our customers have access to the safest possible options for their needs in hazardous areas. Remember, in environments where the risk of explosions is a constant threat, the quality and certification of your equipment can make all the difference.
Industry-Specific Applications and Preferences
When it comes to safeguarding operations in hazardous environments, the choice between intrinsically safe and explosion-proof equipment is not merely a matter of preference but a critical decision informed by specific industry requirements and the nature of the hazardous atmosphere. Each approach has its niche where it shines, influenced by the operational variables and regulatory standards of particular sectors.
Oil and Gas Industry
In the oil and gas sector, where the risk of explosive gases or vapors is ever-present, intrinsically safe equipment is often the go-to choice for portable devices like natural gas detectors and communication tools. The reason for this preference lies in the intrinsic safety’s core principle: limiting the energy available for ignition to such a low level that it cannot ignite a hazardous atmosphere, even under fault conditions. This approach is particularly suited to environments where the atmosphere is constantly or frequently hazardous, as it ensures worker safety without the bulky designs typically associated with explosion-proof enclosures.
Chemical Manufacturing and Processing
Chemical plants, with their wide array of volatile substances, also benefit from intrinsically safe equipment, especially in areas where processes involve the frequent handling or transfer of explosive chemicals. Intrinsically safe solutions are preferred for monitoring and control devices that necessitate close interaction with the process, providing safety without the operational hindrance of heavier explosion-proof alternatives. However, for fixed installations such as junction boxes or control panels that do not require regular human interaction, explosion-proof enclosures may be favored for their robust protection capabilities, even though they are generally more cumbersome and expensive to install and maintain.
Pharmaceuticals
The pharmaceutical industry, with its unique blend of research, production, and warehousing areas, often employs a mix of intrinsically safe and explosion-proof solutions tailored to the specific risks present in each area. Research labs with small-scale experiments may opt for intrinsically safe instrumentation to easily comply with stringent safety standards without compromising the precision and flexibility needed for innovative work. In contrast, larger-scale production areas with higher volumes of potentially explosive dusts or vapors might lean towards explosion-proof equipment, especially for fixed installations.
Utilities and Wastewater Treatment
For utilities and wastewater treatment facilities, where the presence of hazardous gases like methane can vary significantly by location and process stage, the selection between intrinsically safe and explosion-proof options is usually guided by a detailed risk assessment. Portable intrinsically safe devices are often preferred for fieldwork and inspection tasks due to their lighter weight and ease of use, whereas explosion-proof solutions might be selected for fixed installations in consistently hazardous areas.
Mining
The mining industry presents another distinct application, with its unique combination of explosive gases and combustible dust. Here, the robustness of explosion-proof enclosures makes them a suitable choice for fixed installations. Meanwhile, for portable equipment such as communication devices and gas detectors, the preference often leans towards intrinsically safe designs due to their enhanced safety and portability, which are crucial in the confined and often changing environment of a mine.
In summary, the specific applications and preferences for intrinsically safe versus explosion-proof technologies are driven by the intricate balance of safety, cost, and operational efficiency within each industry. Understanding these nuances is crucial for organizations operating in hazardous environments to select the certified safe solution that best aligns with their safety goals and operational needs, ensuring the protection and well-being of all involved.
Mobility and Flexibility in Hazardous Areas
In the realm of safety in hazardous environments, the concepts of Intrinsically Safe vs Explosion Proof equipment come into play not only in terms of protection but also regarding mobility and flexibility in operations. The nature of intrinsically safe and explosion-proof devices significantly influences how work can be carried out in areas prone to explosive risks.
Intrinsically safe equipment is designed to ensure that it cannot release enough energy to ignite a hazardous atmosphere, even under fault conditions. This principle allows for the use of mobile devices, such as intrinsically safe iPad cases and natural gas detectors, directly within hazardous zones without requiring additional protective measures. This inherently safe approach provides significant benefits in terms of mobility and flexibility, enabling workers to carry and use their devices across different locations within a hazardous area without the risk of causing an ignition.
On the other hand, explosion-proof equipment is designed to contain an explosion within its enclosure, preventing the ignition of the external hazardous atmosphere. While providing a high level of protection, explosion-proof designs tend to be bulkier and heavier due to the robust enclosures required to withstand an internal explosion. This characteristic can limit the mobility of devices or equipment, as their installation and movement are more cumbersome. In terms of flexibility, explosion-proof solutions may also restrict the types of equipment that can be used in hazardous areas, as each device must be enclosed in an explosion-proof casing.
When choosing between intrinsically safe and explosion-proof equipment, it’s essential to consider the specific requirements of the hazardous area, including the nature of the explosive atmosphere and the mobility needs of the operation. Intrinsically safe solutions, with their lightweight and flexible design, offer significant advantages for tasks requiring high mobility and frequent movement of equipment within hazardous zones. Explosion-proof solutions, while more restrictive in terms of mobility, provide a high degree of protection where robust containment is necessary.
At Intrinsically Safe Store, we understand the critical importance of selecting the right certified safe solutions for hazardous environments. Our range of intrinsically safe products is designed to meet the safety and operational needs of individuals and organizations working in these high-risk areas, emphasizing our commitment to ensuring the safety and well-being of those on the front lines of hazardous work. Selecting the appropriate safety equipment is not just a regulatory requirement but a crucial factor in maintaining operational efficiency and safeguarding lives in hazardous areas.
Conclusion
In the challenging environments posed by the oil and gas industry, chemical plants, and similar sectors, where the risk of explosions is ever-present, the importance of using certified safe solutions cannot be overstated. Understanding the key differences between Intrinsically Safe and Explosion Proof certifications is vital for ensuring the safety and well-being of those working in these hazardous areas. While both methodologies offer protection, they do so in fundamentally different ways: Intrinsically Safe equipment minimizes the energy available for ignition, whereas Explosion Proof enclosures are designed to contain any explosions that may occur.
Choosing the right safety solution requires a thorough understanding of the specific hazards present in a working environment, as well as the operational needs of the equipment being used. As a leader in providing certified safe solutions, Intrinsically Safe Store is committed to equipping our clients with the knowledge and tools they need to maintain the highest safety standards. Whether through our range of intrinsically safe products or our comprehensive educational resources, we are here to ensure that individuals and organizations operating in these high-risk areas are not just compliant, but are also adopting the best practices in safety and operational efficiency. Remember, in hazardous environments, the right choice in safety equipment isn’t just about compliance—it’s about protection, prevention, and peace of mind.
FAQs on Intrinsically Safe vs Explosion Proof
How do design considerations differ between intrinsically safe and explosion proof equipment?
Intrinsically safe equipment is designed to limit electrical and thermal energy to a level below what is required to ignite a specific hazardous atmospheric mixture, even under fault conditions. This approach often involves the use of barriers to restrict energy entering the hazardous area. In contrast, explosion proof equipment is designed to contain any explosion that originates within its housing and prevent it from igniting the hazardous atmosphere outside of the enclosure. This design typically results in more robust and heavier equipment, made to withstand the pressures of an internal explosion.
What are the maintenance requirements for intrinsically safe systems?
Intrinsically safe systems generally require less rigorous maintenance than explosion proof systems because they do not rely on a physical barrier to contain explosions. Maintenance primarily focuses on ensuring that the energy-limiting components, such as barriers and isolators, are functioning correctly and that no modifications have been made that could increase the energy levels in the system. Regular inspections are also necessary to ensure that all equipment is in compliance with relevant safety standards and certifications.
What are the maintenance requirements for explosion proof systems?
Explosion proof systems require meticulous maintenance to ensure that the integrity of the explosion proof enclosure is not compromised. This includes regular inspections for any signs of damage or wear, such as cracks or corrosion, which could impair its ability to contain an explosion. Seals and gaskets should be checked and replaced as necessary to maintain the protective barrier. Additionally, since explosion proof equipment can run hotter than its intrinsically safe counterparts, thermal inspections can be essential to prevent overheating risks.
What types of gases and dusts are considered in explosion proof design?
Explosion proof design considers a wide range of flammable gases, vapors, and dusts. These can include, but are not limited to, methane (often found in oil and gas environments), hydrogen, propane, ethanol, coal dust, and grain dust. The specific hazardous substances present in a particular environment will determine the classification of the area and the specific requirements for explosion proof equipment. Each type of gas or dust has its own ignition temperature and explosion pressure, which are critical parameters in the design of explosion proof enclosures.
Can you convert explosion proof equipment to intrinsically safe?
No, you cannot convert explosion proof equipment to intrinsically safe equipment due to the fundamental differences in their design principles and methods of protection. Intrinsically safe equipment is designed to prevent the release of enough energy to ignite a hazardous atmosphere, whereas explosion proof equipment is built to contain an explosion should it occur. Converting one type to another would require a complete redesign and re-certification according to the relevant safety standards for intrinsically safe equipment. When determining the best approach for a hazardous environment, it is crucial to consider the specific needs and regulations of the application to choose between intrinsically safe and explosion proof solutions.