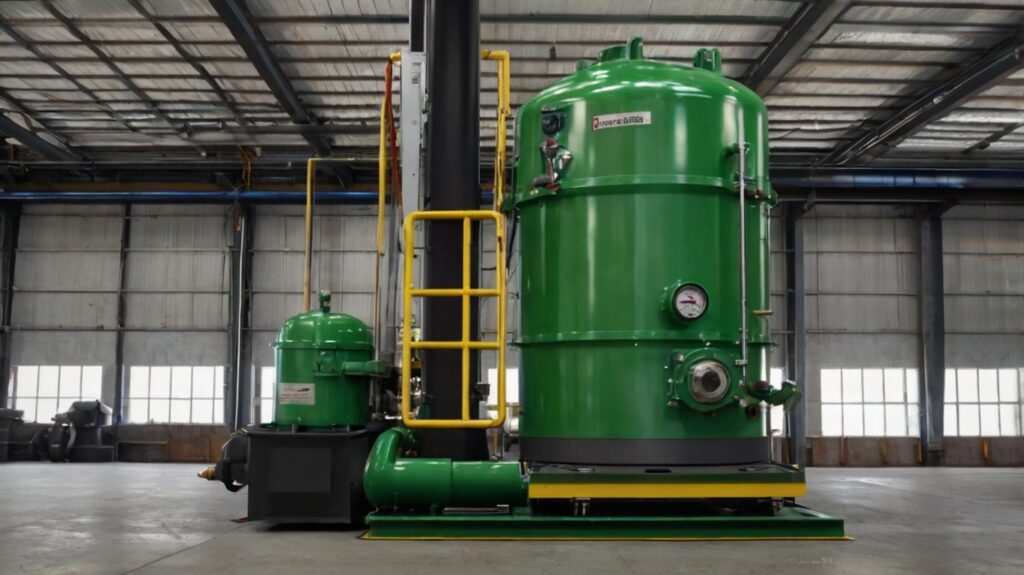
Cleaning in industrial environments may seem routine, but in explosive atmospheres, it’s a critical safety task. A traditional vacuum cleaner—designed for general use—can become a source of ignition in the presence of flammable dust, vapors, or gases.
Intrinsically safe vacuum cleaners are engineered to operate safely in hazardous areas. Certified for use in environments where explosive atmospheres are present, they reduce the risk of ignition by eliminating sources of heat, sparks, or static discharge. This article explores what makes these vacuums safe, the consequences of using uncertified equipment, top models available, key buying criteria, and long-term maintenance practices.
Explore our range of ATEX & IECEx-certified intrinsically safe vacuums for industrial environments.
What Makes a Vacuum Cleaner Intrinsically Safe?
An intrinsically safe vacuum cleaner is designed to prevent ignition in hazardous environments by limiting energy—both electrical and thermal—below the threshold that could ignite an explosive atmosphere.
Key characteristics of intrinsically safe vacuums include:
- Non-sparking materials used in motor housing, nozzles, and filters
- Static-dissipative hoses and grounded components to prevent electrostatic discharge
- Sealed or brushless motors that eliminate arc generation
- HEPA filtration systems for safe dust containment
- Low surface temperature ratings, compliant with explosion zone requirements
These vacuums undergo third-party certification to meet international safety standards for hazardous locations, including ATEX (EU), IECEx (global), and NEC Class I Division 1 (North America). The equipment is tested to remain safe even during fault conditions, making it a primary safety barrier in many industrial sites.
Risks of Using Non-Certified Vacuum Equipment
Standard vacuum cleaners are not designed to manage the hazards of explosive zones. Even a seemingly minor feature—like an ungrounded hose—can produce a static spark strong enough to ignite a combustible cloud.
Risks associated with uncertified vacuum use include:
- Ignition of flammable gases or vapors due to internal sparking or motor failure
- Static electricity buildup in hoses or tanks leading to electrostatic discharge
- Heat generated by motors exceeding ignition temperatures
- Inadequate filtration systems that allow combustible dust to become airborne
- Legal and financial penalties for non-compliance with OSHA, NFPA, or ATEX requirements
In hazardous zones, even microscopic particles of dust can create volatile conditions when suspended in air. That’s why certified equipment is required—not just recommended—in environments classified under ATEX or NEC codes.
Protect your workplace from fire and explosion risks with a certified vacuum. Shop intrinsically safe vacuums now.
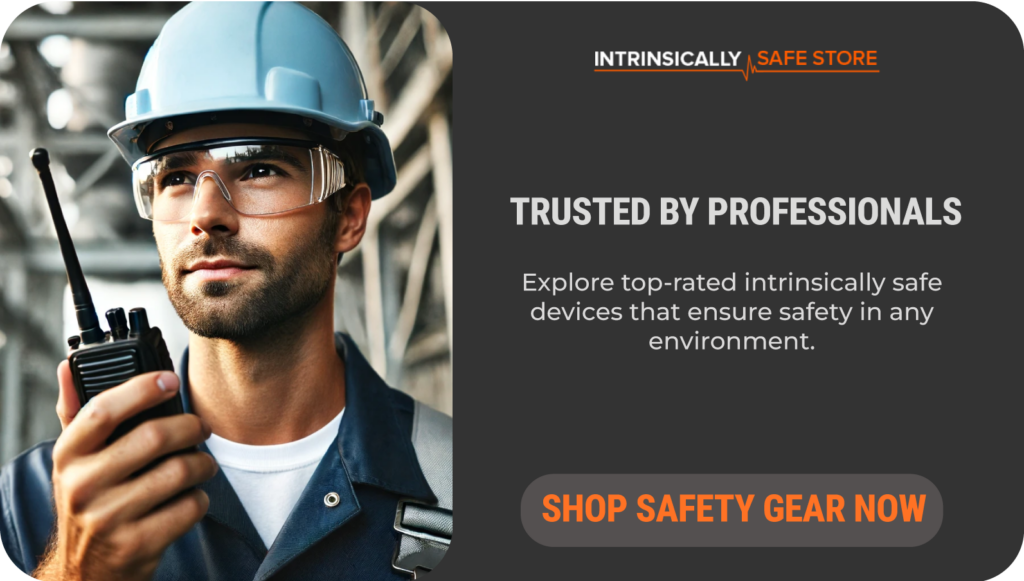
Top-Rated Intrinsically Safe Vacuums for Industrial Environments
The following models are certified and trusted in hazardous industrial operations. Selection depends on the specific zone classification, type of hazard, and the operational needs of the facility.
Model | Certifications | Application | Features |
---|---|---|---|
Tiger-Vac C-10EX | ATEX, IECEx, C1D1 | Wet and dry hazardous zones | Stainless steel housing, static-dissipative hose, HEPA filter |
Prestivac EV1-5 EX | Class I, Division 1 | Hazardous locations with combustible dust and flammable liquids | Stainless steel construction, HEPA filtration, anti-static tools |
Delfin Z22 | ATEX Zone 2, C1D2 | General industrial | Brushless motor, portable, antistatic filtration system |
Prestivac AV1-5 EX HEPA | Class I Division 1 | Industrial environments with flammable vapors and dust | Stainless steel, HEPA filtration, anti-static accessories |
Each model listed complies with zone or division requirements and is suitable for Class I, II, and III locations, depending on the type of hazardous material present.
Understanding ATEX, IECEx, and C1D1 Compliance
Before selecting a vacuum, it’s essential to understand how explosive zones are defined and which certification applies to your environment.
Key certification frameworks:
ATEX (EU)
- Zone 0: Constant presence of explosive gases
- Zone 1: Likely presence under normal operation
- Zone 2: Unlikely but possible presence under abnormal conditions
- Zone 20, 21, 22: Dust equivalents for solid particulates
IECEx (Global)
- Recognized internationally and aligned with ATEX for testing and labeling
NEC (North America)
- Class I: Gases and vapors
- Class II: Combustible dust
- Division 1: Hazard present during normal operation
- Division 2: Hazard present under abnormal conditions
How to verify certification:
- Check labeling for “Ex” marking, group classification (e.g., IIC, IIIC), and temperature class (e.g., T4)
- Review product documentation for applicable standards (EN 60079, UL, CSA)
- Match the vacuum’s rating with your facility’s hazardous area classification
Choosing equipment without verifying certification puts personnel, property, and compliance at risk.
Maintenance and Best Practices for Long-Term Safety
Even the best vacuum can become unsafe if not properly maintained. Certified equipment requires regular checks to ensure continued compliance and functionality in high-risk areas.
Best practices include:
- Conduct weekly inspections of grounding continuity and antistatic components
- Replace filters and bags with manufacturer-approved parts only
- Keep motor housings and enclosures clean and free from dust accumulation
- Train operators on correct procedures for use, cleaning, and storage
- Maintain records of maintenance, filter changes, and zone assignments
Avoid common mistakes such as modifying equipment, bypassing safety features, or using uncertified accessories. Maintenance should always align with the original certification to retain legal and functional safety status.
Need expert guidance? Contact us today for a free consultation on selecting the right intrinsically safe vacuum for your facility.
Schedule a Call with Our Safety Experts
Frequently Asked Questions (FAQs)
What is the difference between intrinsically safe and explosion-proof vacuums?
Intrinsically safe vacuums are designed to prevent ignition by limiting the energy inside the device, even during fault conditions. Explosion-proof vacuums, on the other hand, are built to contain an internal explosion and prevent it from igniting the surrounding atmosphere.
Can a standard vacuum cleaner be made intrinsically safe with modifications?
No. Intrinsic safety certification applies to the complete system, including its design, materials, and components. Modifying a standard vacuum voids its compliance and may create new ignition risks.
How do I know what zone classification applies to my facility?
Zone classification is determined by a risk assessment that considers the types of hazardous materials present, their concentration, and how frequently they are released. Consult ATEX or NEC 500 guidelines, or work with a certified safety consultant.
Are intrinsically safe vacuums suitable for combustible dust?
Yes. Many intrinsically safe vacuums are certified for both gas and dust environments. Ensure the model you choose is marked for the correct dust group (e.g., IIIC) and zone (e.g., Zone 21 or Class II Division 1).
How often should I service or inspect an intrinsically safe vacuum?
Inspection frequency depends on usage intensity and regulatory requirements. As a general rule, perform weekly visual checks and full maintenance quarterly, or as recommended by the manufacturer and your facility’s safety procedures.
Conclusion
The use of intrinsically safe vacuum cleaners is essential for facilities operating in hazardous environments. Whether dealing with explosive vapors, flammable gases, or combustible dust, these certified systems eliminate the ignition risks posed by standard vacuum cleaners.
Understanding the principles of intrinsic safety, choosing equipment with proper certification, and following best practices for maintenance will ensure your operation remains compliant, productive, and above all—safe.
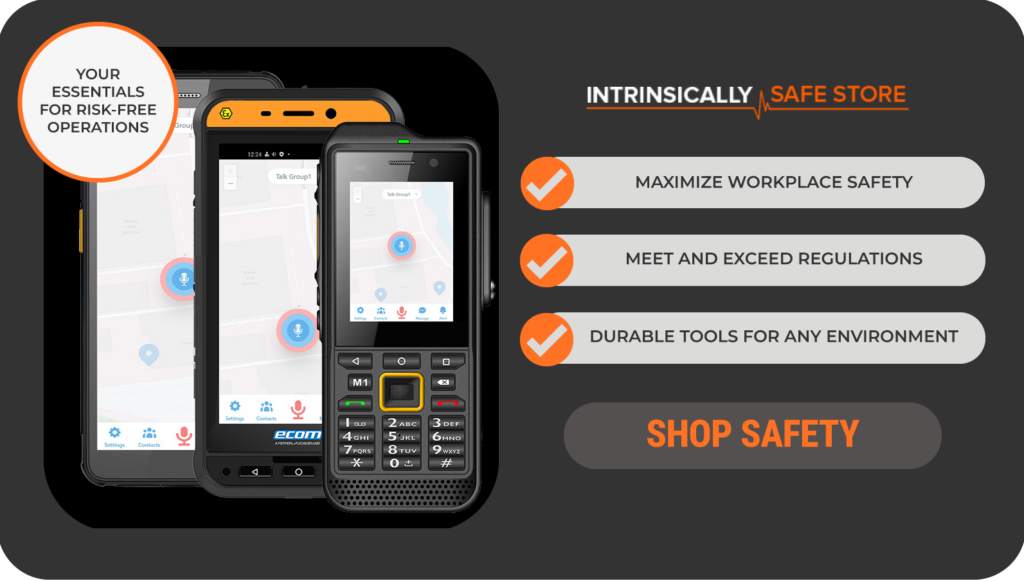