Welcome to the Intrinsically Safe Store, your one-stop-shop for all your safety equipment needs. We are dedicated to providing you with the most reliable and up-to-date information on safety standards in the industry. In this article, we will delve into the comparison of Intrinsically Safe and Explosion-Proof standards. We invite you to visit our website for more information and to explore our wide range of safety products.
Understanding Intrinsically Safe Standards
Designers create IS standards to prevent the ignition of potentially explosive atmospheres. They achieve this by limiting the available energy, both electrical and thermal, for ignition. They apply intrinsic safety as a protection technique to electrical equipment and wiring, ensuring that even under fault conditions, they cannot ignite a mixture of flammable or combustible material.
Benefits of Intrinsically Safe Standards
- IS equipment can be safely operated while maintenance is being performed.
- It reduces the risks associated with the presence of flammable gases or dust.
- IS standards are globally recognized and accepted.
Understanding Explosion-Proof Standards
On the other hand, designers create explosion-proof standards to contain an explosion. In an explosion-proof enclosure, the equipment can operate at normal temperatures or even produce sparks or arcs without causing an explosion. They built the enclosure robustly to withstand an internal explosion and prevent the ignition of an explosive atmosphere outside the enclosure.
Benefits of Explosion-Proof Standards
- Explosion-proof equipment is designed to contain and isolate potential ignition sources.
- It allows for the operation of standard equipment in hazardous areas.
- These standards are also globally recognized and accepted.
Comparison of Intrinsically Safe and Explosion-Proof Standards
While both standards aim to prevent explosions, they approach this goal differently. The Intrinsically Safe standards limit the energy to a level below what a specific hazardous atmospheric mixture requires to ignite. In contrast, Explosion-Proof standards contain and isolate the explosion within the device.
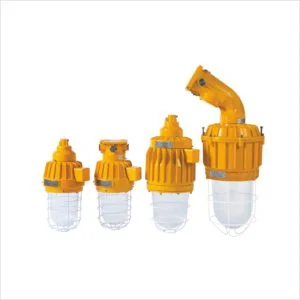
Case Study: Oil and Gas Industry
The oil and gas industry widely uses both standards. For instance, the industry typically uses Intrinsically Safe equipment in areas where explosive gases are constantly present. The design of this equipment allows it to operate in such environments without causing an ignition. Conversely, the industry often uses Explosion-Proof equipment in areas where explosive gases are present only under abnormal conditions.
Choosing Between Intrinsically Safe and Explosion-Proof Standards
The choice between IS and Explosion-Proof standards depends on several factors, including the nature of the hazardous area, the type of equipment used, and the specific requirements of the operation. It is crucial to conduct a thorough risk assessment to determine the most suitable standard for your needs.
Understanding Intrinsically Safe and Explosion-Proof Standards
In conclusion, both Intrinsically Safe and Explosion-Proof standards play a crucial role in preventing explosions in hazardous environments. While they approach this goal differently, they both provide effective solutions for different scenarios. It is essential to understand these standards and choose the most suitable one for your specific needs. For more information and guidance, feel free to contact us at the Intrinsically Safe Store. We are here to help you make the safest choice for your industry.