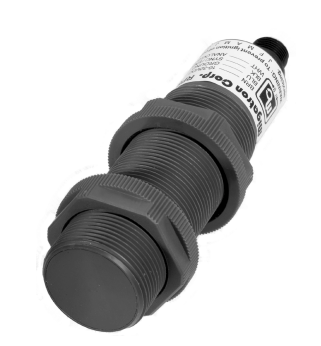
In industrial settings where safety is paramount, intrinsically safe sensors emerge as indispensable components, ensuring the protection of both human life and valuable assets. These sensors are meticulously designed to function in hazardous environments, where the presence of flammable gases, vapors, or dust could lead to catastrophic explosions or fires. By limiting the electrical and thermal energy available for ignition, intrinsically safe sensors prevent any sparks or heat that could ignite a hazardous atmosphere. Their significance is particularly pronounced in industries such as oil and gas, chemical manufacturing, mining, and pharmaceuticals, where maintaining stringent safety standards is not just a regulatory requirement but a moral imperative. As technology advances, the development of more sophisticated intrinsically safe sensors continues to enhance their capabilities, offering greater precision and reliability in safety-critical applications.
The principle of intrinsic safety is rooted in the idea of preventing ignition by controlling the energy within the sensor and its associated wiring. This is achieved through a combination of design strategies, including the use of low-power electronics, energy-limiting barriers, and robust isolation techniques. Such measures ensure that intrinsically safe sensors can be safely deployed in environments where traditional sensors might pose significant risks. Their ability to operate without introducing any risk of ignition makes them indispensable in safety systems that require continuous monitoring and control of potentially explosive atmospheres. As industries continue to prioritize safety and efficiency, the demand for intrinsically safe sensors is likely to grow, driving innovation and improvements in this vital field.
Understanding Intrinsically Safe Sensors: Importance and Applications in Safety Systems
In the realm of industrial safety, the concept of intrinsically safe sensors plays a pivotal role in ensuring the protection of both human life and valuable equipment. Intrinsically safe sensors are designed to operate in hazardous environments where the presence of flammable gases, vapors, or dust could potentially lead to catastrophic explosions or fires. These sensors are engineered to limit the energy, both electrical and thermal, available for ignition, thereby preventing any sparks or heat that could ignite a hazardous atmosphere. The importance of intrinsically safe sensors cannot be overstated, as they are integral to maintaining safety standards in industries such as oil and gas, chemical manufacturing, mining, and pharmaceuticals.
The fundamental principle behind intrinsically safe sensors is to ensure that the energy levels within the sensor and its associated wiring are kept below the threshold that could cause ignition. This is achieved through a combination of design strategies, including the use of low-power electronics, energy-limiting barriers, and robust isolation techniques. By adhering to these principles, intrinsically safe sensors can be safely deployed in environments where traditional sensors might pose a significant risk. This makes them indispensable in safety systems that require continuous monitoring and control of potentially explosive atmospheres.
One of the key applications of intrinsically safe sensors is in the oil and gas industry, where they are used to monitor parameters such as pressure, temperature, and flow rates in pipelines and storage tanks. In these settings, the presence of volatile hydrocarbons necessitates the use of sensors that can operate without introducing any risk of ignition. Similarly, in chemical manufacturing plants, intrinsically safe sensors are employed to track the concentration of hazardous chemicals, ensuring that any deviations from safe levels are promptly detected and addressed. This proactive approach to safety not only protects workers but also minimizes the risk of costly downtime and equipment damage.
In mining operations, intrinsically safe sensors are crucial for monitoring environmental conditions such as methane levels and air quality. Given the confined nature of underground mines and the potential for gas build-up, these sensors provide an essential layer of protection by alerting workers to dangerous conditions before they escalate into life-threatening situations. Furthermore, in the pharmaceutical industry, intrinsically safe sensors are used to ensure the safe handling and processing of volatile compounds, safeguarding both the product and the personnel involved in its production.
The adoption of intrinsically safe sensors is also driven by stringent regulatory requirements that mandate the use of explosion-proof equipment in hazardous areas. Compliance with these regulations not only enhances safety but also demonstrates a commitment to best practices and corporate responsibility. As technology continues to advance, the development of more sophisticated intrinsically safe sensors is expected to further enhance their capabilities, offering even greater precision and reliability in safety-critical applications.
In summary, intrinsically safe sensors are a cornerstone of modern safety systems, providing a reliable means of monitoring and controlling hazardous environments. Their ability to operate safely in potentially explosive atmospheres makes them an essential component in a wide range of industries, where they play a crucial role in protecting both people and assets. As industries continue to prioritize safety and efficiency, the demand for intrinsically safe sensors is likely to grow, driving innovation and improvements in this vital field.
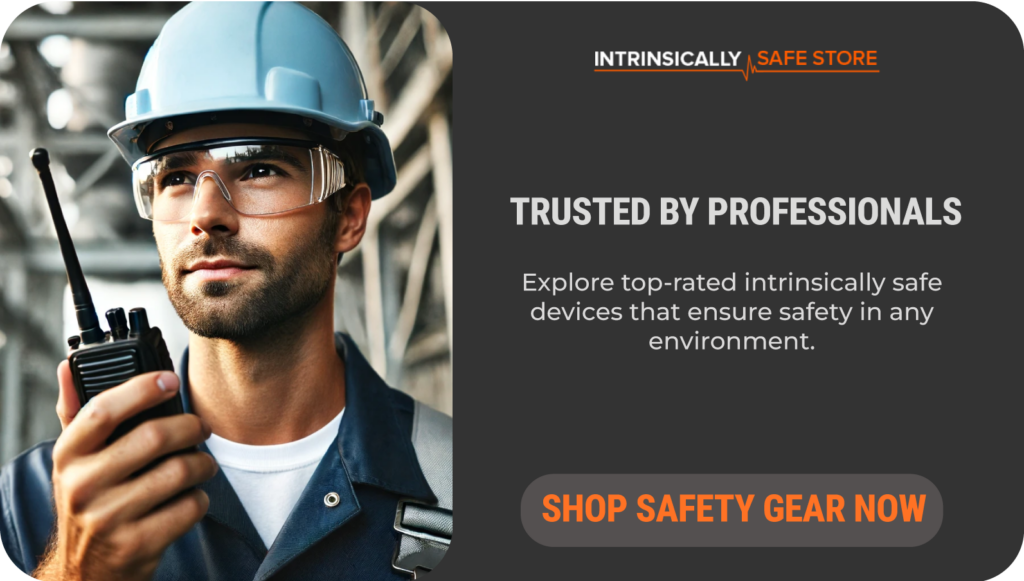
Who Should Understand Intrinsically Safe Sensors: Importance and Applications in Safety Systems
Understanding intrinsically safe sensors is crucial for a diverse range of professionals and industries, particularly those involved in environments where explosive atmospheres are a risk. Engineers, safety managers, and technicians working in sectors such as oil and gas, chemical manufacturing, mining, and pharmaceuticals must have a comprehensive grasp of these sensors to ensure the safety and efficiency of their operations. These individuals are responsible for designing, implementing, and maintaining systems that prevent accidents and protect both human lives and valuable assets. By understanding the principles and applications of intrinsically safe sensors, they can make informed decisions about the best technologies and practices to employ in hazardous environments.
For engineers, particularly those specializing in electrical and instrumentation engineering, a deep understanding of intrinsically safe sensors is essential. These professionals are tasked with designing systems that must operate safely in potentially explosive atmospheres. They need to select appropriate sensors that comply with safety standards and regulations, ensuring that the systems they design can withstand the harsh conditions without compromising safety. Engineers must also consider the integration of these sensors into larger control systems, ensuring that they communicate effectively with other components to provide accurate and reliable data. This requires a thorough understanding of both the technical specifications of the sensors and the environmental conditions in which they will be used.
Safety managers play a critical role in overseeing the implementation and maintenance of intrinsically safe systems. Their primary responsibility is to ensure that all safety protocols are followed and that the systems in place are functioning correctly. This involves regular inspections and audits to verify that the sensors and other safety equipment are in good working order. Safety managers must also stay up-to-date with the latest advancements in intrinsically safe technology and industry regulations to ensure that their facilities remain compliant and safe. By understanding the importance and applications of intrinsically safe sensors, safety managers can effectively mitigate risks and prevent accidents in hazardous environments.
Technicians who work directly with intrinsically safe sensors must have a practical understanding of how these devices operate and how to troubleshoot any issues that may arise. They are often responsible for the installation, calibration, and maintenance of these sensors, ensuring that they provide accurate and reliable data. Technicians must be familiar with the specific requirements of intrinsically safe systems, including the need for proper grounding and the use of approved equipment. By understanding the intricacies of intrinsically safe sensors, technicians can ensure that these devices function correctly and contribute to the overall safety of the facility.
In addition to these professionals, regulatory bodies and industry organizations also have a vested interest in understanding intrinsically safe sensors. These entities are responsible for developing and enforcing safety standards and regulations that govern the use of these sensors in hazardous environments. By understanding the technology and its applications, they can create guidelines that promote safety and innovation within the industry. This, in turn, helps to protect workers and the environment while supporting the continued growth and development of industries that rely on intrinsically safe systems.
The Main Benefits of Understanding Intrinsically Safe Sensors: Importance and Applications in Safety Systems
Understanding intrinsically safe sensors is crucial for industries where safety is paramount, particularly in environments prone to explosive atmospheres. These sensors are designed to operate safely in hazardous areas by limiting the energy available for ignition, thus preventing explosions. The benefits of these sensors extend beyond mere compliance with safety regulations; they are integral to the seamless operation and longevity of safety systems in various industrial settings.
One of the primary benefits of intrinsically safe sensors is their ability to enhance operational safety without compromising on performance. In industries such as oil and gas, chemical manufacturing, and mining, the presence of flammable gases, vapors, or dust is a constant threat. Intrinsically safe sensors mitigate this risk by ensuring that even in the event of a fault, the energy released is insufficient to ignite the hazardous atmosphere. This intrinsic safety feature allows for continuous monitoring and control of processes in these environments, significantly reducing the risk of catastrophic incidents. By understanding how these sensors function and their role in safety systems, industries can better implement them to protect both personnel and infrastructure.
Another significant advantage of intrinsically safe sensors is their contribution to cost efficiency. While the initial investment in intrinsically safe equipment might be higher compared to non-intrinsically safe alternatives, the long-term savings are substantial. These sensors reduce the need for expensive explosion-proof enclosures and complex wiring systems, which are typically required to protect non-intrinsically safe equipment. Additionally, the maintenance and inspection costs are lower, as intrinsically safe systems are generally easier to service and require less frequent checks. Understanding the cost implications and benefits of these sensors can lead to more informed decision-making and resource allocation within an organization.
The versatility of intrinsically safe sensors is another compelling benefit. They are used in a wide range of applications, from monitoring temperature and pressure to detecting gas leaks and measuring fluid levels. This versatility makes them indispensable in safety systems across various industries. For instance, in the pharmaceutical industry, intrinsically safe sensors are used to ensure that the production environment remains free from contaminants that could lead to product recalls or health hazards. In the food and beverage industry, they help maintain the integrity of production processes by preventing contamination and ensuring compliance with stringent safety standards. By understanding the diverse applications of these sensors, industries can leverage their capabilities to enhance safety and efficiency across different operational areas.
Moreover, intrinsically safe sensors play a critical role in ensuring regulatory compliance. Many industries are subject to strict safety regulations that mandate the use of intrinsically safe equipment in hazardous areas. By understanding the importance of these sensors, companies can ensure compliance with international safety standards such as ATEX, IECEx, and NEC, thereby avoiding costly fines and legal issues. Compliance not only protects the company’s reputation but also instills confidence among stakeholders, including employees, customers, and investors.
In essence, the benefits of understanding intrinsically safe sensors are multifaceted, encompassing enhanced safety, cost efficiency, versatility, and regulatory compliance. These sensors are not just components of a safety system; they are pivotal to the operational integrity and sustainability of industries operating in hazardous environments. By appreciating their importance and applications, industries can harness the full potential of intrinsically safe sensors to create safer, more efficient, and compliant operational landscapes.
Embracing Intrinsic Safety for a Secure Future
The adoption of intrinsically safe sensors is not merely a compliance measure but a strategic investment in the future of industrial safety. These sensors are a cornerstone of modern safety systems, providing a reliable means of monitoring and controlling hazardous environments. Their ability to operate safely in potentially explosive atmospheres makes them an essential component in a wide range of industries, where they play a crucial role in protecting both people and assets. By understanding the principles and applications of intrinsically safe sensors, industries can make informed decisions about the best technologies and practices to employ in hazardous environments. This proactive approach to safety not only protects workers but also minimizes the risk of costly downtime and equipment damage.
As industries continue to evolve and face new challenges, the role of intrinsically safe sensors will become even more critical. The ongoing development of more advanced sensors will offer greater precision and reliability, further enhancing their capabilities in safety-critical applications. By embracing intrinsic safety, industries can ensure a secure future, where the protection of human life and valuable assets remains a top priority. This commitment to safety and innovation will not only enhance operational efficiency but also demonstrate a dedication to best practices and corporate responsibility, fostering trust and confidence among stakeholders.
Getting Started with Understanding Intrinsically Safe Sensors: Importance and Applications in Safety Systems
Embarking on the journey to understand intrinsically safe sensors is a crucial step for anyone involved in industries where safety is paramount. These sensors are designed to operate safely in hazardous environments, where the presence of flammable gases, vapors, or dust could lead to catastrophic explosions if not properly managed. The importance of intrinsically safe sensors cannot be overstated, as they play a vital role in ensuring the safety and reliability of operations in sectors such as oil and gas, chemical manufacturing, mining, and pharmaceuticals.
To get started with intrinsically safe sensors, it is essential to first grasp the fundamental principles that govern their operation. These sensors are engineered to limit the energy, both electrical and thermal, available for ignition. This is achieved through meticulous design and rigorous testing, ensuring that even in the event of a fault, the energy levels remain below the threshold required to ignite a hazardous atmosphere. Understanding these principles is key to appreciating how intrinsically safe sensors contribute to overall safety systems.
The next step involves familiarizing oneself with the various types of intrinsically safe sensors available in the market. These sensors come in different forms, including pressure sensors, temperature sensors, flow sensors, and level sensors, each tailored to specific applications. For instance, in the oil and gas industry, pressure sensors are often used to monitor the pressure levels in pipelines and storage tanks, ensuring they remain within safe limits. Similarly, temperature sensors are crucial in chemical plants to prevent overheating and potential chemical reactions that could lead to explosions. By understanding the specific applications of each type of sensor, one can better appreciate their role in maintaining safety.
Another important aspect to consider is the regulatory framework governing the use of intrinsically safe sensors. Various international standards, such as the International Electrotechnical Commission’s IEC 60079 series, provide guidelines for the design, testing, and certification of these sensors. Familiarity with these standards is essential for ensuring compliance and maintaining the integrity of safety systems. Additionally, understanding the certification process can help in selecting the right sensors for specific applications, as certified sensors have undergone rigorous testing to ensure their safety and reliability.
Furthermore, integrating intrinsically safe sensors into existing safety systems requires a comprehensive understanding of the system architecture. This involves assessing the compatibility of the sensors with other components, such as control systems and data acquisition systems, to ensure seamless operation. It also requires a thorough understanding of the communication protocols used by the sensors, as well as the data they generate. By effectively integrating these sensors into safety systems, organizations can enhance their ability to monitor and respond to potential hazards in real-time, thereby reducing the risk of accidents and improving overall safety.
In summary, getting started with intrinsically safe sensors involves a multifaceted approach that includes understanding their fundamental principles, familiarizing oneself with the different types of sensors and their applications, adhering to regulatory standards, and effectively integrating them into existing safety systems. By taking these steps, organizations can harness the full potential of intrinsically safe sensors to enhance safety and protect both personnel and assets in hazardous environments.
Optimal Timing for Understanding Intrinsically Safe Sensors: Importance and Applications in Safety Systems
Grasping the concept of intrinsically safe sensors and their role in safety systems is crucial at a time when industries are increasingly prioritizing safety and efficiency. The best time to delve into this subject is during the initial phases of designing or upgrading safety systems, particularly in industries where hazardous environments are prevalent. This is because intrinsically safe sensors are integral to ensuring that safety systems can operate effectively without posing additional risks. Understanding their importance and applications early in the design process allows for a more seamless integration, ensuring that all components of the safety system are compatible and optimized for the specific needs of the environment.
Industries such as oil and gas, chemical manufacturing, and mining are particularly sensitive to the risks posed by explosive atmospheres. In these sectors, the implementation of intrinsically safe sensors is not just a regulatory requirement but a critical component of operational safety. By understanding the role of these sensors at the outset, companies can better align their safety strategies with industry standards and regulations, thereby avoiding costly retrofits or modifications later on. This proactive approach not only enhances safety but also contributes to operational efficiency by minimizing downtime and maintenance costs associated with non-compliant or suboptimal safety systems.
Moreover, the technological landscape is constantly evolving, with new advancements in sensor technology emerging regularly. Keeping abreast of these developments is essential for safety professionals and engineers who are responsible for designing and maintaining safety systems. The best time to update one’s knowledge about intrinsically safe sensors is during periods of technological transition or when new regulations are introduced. This ensures that safety systems are not only compliant with current standards but also leverage the latest innovations to enhance performance and reliability. For instance, advancements in wireless sensor technology have opened up new possibilities for monitoring and control in hazardous environments, offering greater flexibility and data accuracy.
Another critical time to focus on intrinsically safe sensors is during risk assessment and safety audits. These processes provide an opportunity to evaluate the effectiveness of existing safety systems and identify areas for improvement. By understanding the capabilities and limitations of intrinsically safe sensors, safety professionals can make informed decisions about upgrades or replacements that will enhance the overall safety of the operation. This is particularly important in industries where the consequences of safety failures can be catastrophic, both in terms of human life and financial loss.
In summary, the best time to understand intrinsically safe sensors and their applications in safety systems is during the early stages of system design, technological transitions, and safety audits. By prioritizing this knowledge at these critical junctures, industries can ensure that their safety systems are robust, compliant, and capable of protecting both people and assets in hazardous environments.
Exploring the Role of Intrinsically Safe Sensors in Safety Systems
Intrinsically safe sensors play a pivotal role in modern safety systems, particularly in industries where hazardous environments are a daily reality. These sensors are designed to operate safely in potentially explosive atmospheres, such as those found in oil and gas, chemical processing, and mining industries. Their importance cannot be overstated, as they provide a critical layer of protection by ensuring that electrical equipment does not become a source of ignition. This is achieved through the careful design and engineering of the sensors to limit the energy, both electrical and thermal, available for ignition.
The application of intrinsically safe sensors is vast and varied, reflecting the diverse needs of industries that operate in hazardous conditions. In the oil and gas sector, for instance, these sensors are used to monitor pressure, temperature, and flow rates within pipelines and storage tanks. By providing real-time data, they enable operators to maintain optimal conditions and prevent situations that could lead to catastrophic failures. Similarly, in chemical plants, intrinsically safe sensors are employed to detect gas leaks and monitor chemical reactions, ensuring that any deviations from normal operating conditions are quickly identified and addressed.
One of the key advantages of intrinsically safe sensors is their ability to be integrated into existing safety systems without the need for extensive modifications. This is particularly beneficial for industries that have already invested heavily in infrastructure and are looking to enhance their safety protocols without incurring significant additional costs. The sensors can be seamlessly incorporated into a wide range of systems, from simple alarm setups to complex automated control systems, providing flexibility and scalability to meet the specific needs of each application.
Moreover, intrinsically safe sensors contribute to the overall reliability and efficiency of safety systems. By reducing the risk of ignition, they help to minimize the potential for accidents and downtime, which can have significant financial and operational implications. This reliability is further enhanced by the robust design of the sensors, which are built to withstand harsh environmental conditions and provide accurate readings over extended periods. This durability ensures that safety systems remain operational even in the most challenging environments, providing peace of mind to operators and stakeholders alike.
The importance of intrinsically safe sensors extends beyond their immediate functional benefits. They also play a crucial role in regulatory compliance, as many industries are subject to stringent safety standards and regulations. By incorporating intrinsically safe sensors into their safety systems, companies can demonstrate their commitment to safety and compliance, which can be a significant factor in maintaining their license to operate. This is particularly important in industries where the consequences of non-compliance can be severe, both in terms of financial penalties and reputational damage.
In summary, intrinsically safe sensors are an essential component of modern safety systems, offering a range of benefits that enhance safety, reliability, and compliance. Their ability to operate safely in hazardous environments, combined with their flexibility and durability, makes them an invaluable tool for industries that prioritize safety and risk management. As technology continues to advance, the role of intrinsically safe sensors is likely to expand, offering even greater opportunities for improving safety and efficiency in hazardous environments.
Frequently Asked Questions About Intrinsically Safe Sensors
Intrinsically safe sensors are a critical component in modern safety systems, especially in industries where hazardous environments are prevalent. These sensors are designed to operate safely in potentially explosive atmospheres by limiting the energy available for ignition. Understanding their importance and applications can be complex, so here are some frequently asked questions to help clarify their role and significance.
What are intrinsically safe sensors?
Intrinsically safe sensors are devices engineered to prevent sparks or heat that could ignite flammable gases, vapors, or dust in hazardous areas. They achieve this by ensuring that the electrical and thermal energy within the sensor is kept below the level that could cause ignition. This is accomplished through careful design and the use of barriers or isolators that limit the energy transmitted to the sensor. The concept of intrinsic safety is a preventive measure, ensuring that even in the event of a fault, the sensor will not become a source of ignition.
Why are intrinsically safe sensors important in safety systems?
The importance of intrinsically safe sensors in safety systems cannot be overstated. In industries such as oil and gas, chemical manufacturing, and mining, the presence of flammable substances is a constant risk. Intrinsically safe sensors provide a layer of protection by ensuring that the equipment used in these environments does not become a source of ignition. This is crucial for protecting both human lives and valuable assets. By preventing explosions and fires, these sensors help maintain operational continuity and reduce the risk of catastrophic incidents.
How do intrinsically safe sensors differ from other safety measures?
Unlike other safety measures that may rely on containment or suppression of explosions, intrinsically safe sensors focus on prevention. They are part of a broader safety strategy that includes explosion-proof equipment and other protective measures. However, intrinsic safety is unique in that it addresses the root cause of potential ignition by controlling the energy within the sensor itself. This makes it a proactive approach, reducing the likelihood of an incident occurring in the first place.
What are the applications of intrinsically safe sensors?
Intrinsically safe sensors are used in a wide range of applications across various industries. In the oil and gas sector, they are employed in monitoring systems for pipelines, refineries, and offshore platforms. In chemical plants, they are used to monitor processes and detect leaks or changes in environmental conditions. Mining operations utilize these sensors to ensure safe working conditions underground, where flammable gases can accumulate. Additionally, intrinsically safe sensors are used in pharmaceuticals, food processing, and any industry where explosive atmospheres may be present.
How are intrinsically safe sensors certified?
Certification of intrinsically safe sensors is a rigorous process that involves testing and evaluation by recognized standards organizations. These organizations, such as ATEX in Europe and UL in the United States, set the criteria for what constitutes intrinsic safety. The certification process ensures that the sensors meet the necessary safety standards and can be safely used in hazardous environments. This certification is crucial for compliance with industry regulations and for ensuring the safety of operations.
Understanding intrinsically safe sensors and their role in safety systems is essential for industries operating in hazardous environments. By preventing ignition and ensuring safe operation, these sensors play a vital role in protecting both people and property.
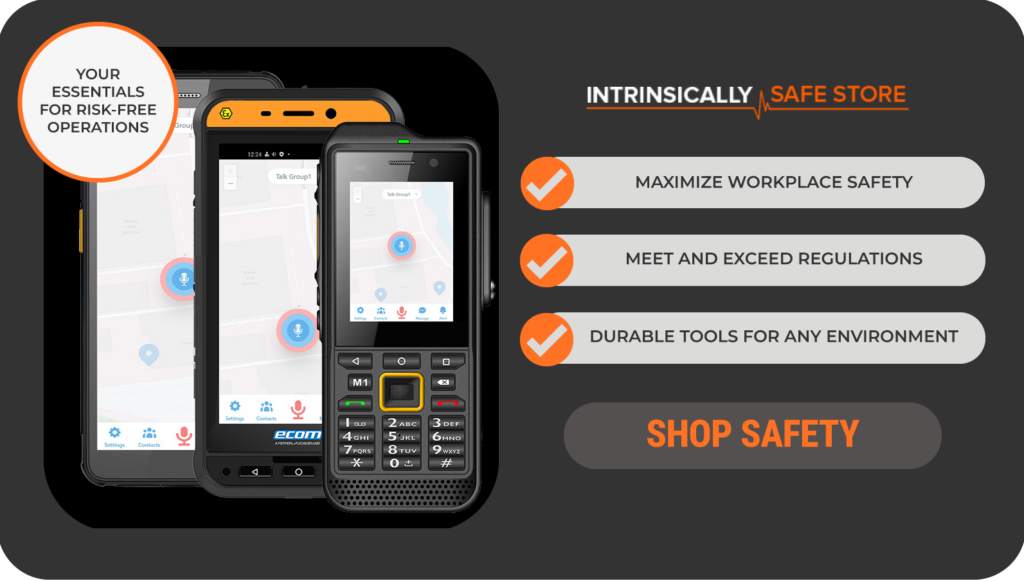