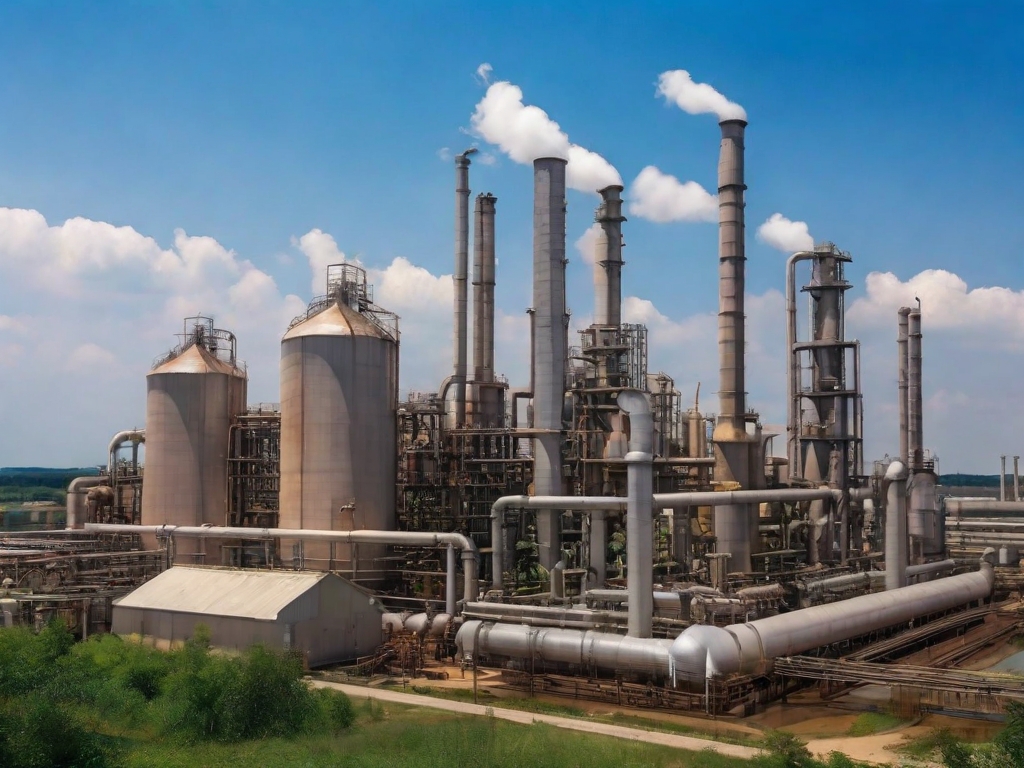
Definition: MIL-STD-461 compliance for VPT DC-DC converters and EMI filters ensures that these electronic components meet the stringent electromagnetic interference (EMI) standards required for military and aerospace applications. This compliance is crucial for ensuring proper system operation in environments with high levels of EMI.
Science Behind It: The compliance process involves rigorous testing across four sections: conducted emissions, radiated emissions, conducted susceptibility, and radiated susceptibility. These tests assess how much EMI the system releases and receives, and how well it blocks these signals. Filters and other components are used to minimize EMI and ensure that the system operates as intended.
Examples in Action:
- The DVMC50 EMI filter is designed to filter conducted emissions of two SVLTR50 series DC-DC converters, meeting MIL-STD-461 Revisions C, D, E, F, and G requirements for conducted emissions and conducted susceptibility.
- The FGDS-20A-50V filter module from GAIA Converter provides EMI compliance for avionics and defense applications, meeting MIL-STD-461 D/E/F and DO-160 C/D/E standards.
Fun Fact: Companies that ensure MIL-STD-461 compliance for their electronic systems can reduce the risk of failing military compliance testing and minimize the need for costly redesigns.
- Compliance with MIL-STD-461 for VPT DC-DC converters and EMI filters ensures safety, regulatory adherence, and performance reliability in hazardous environments.
- Overcoming challenges such as EMI, power integrity, heat dissipation, and component selection is critical for maintaining compliance.
- Implementing best practices like regular testing, proper grounding, shielded cables, and using certified equipment helps sustain MIL-STD-461 compliance in demanding industrial settings.
The Importance of Compliance for VPT Products
Ensuring MIL-STD-461 compliance for VPT DC-DC converters and EMI filters is crucial for several reasons:
Safety in Hazardous Environments
In industries such as oil and gas, where the risk of explosions and hazardous incidents is high, compliance with military standards becomes non-negotiable. VPT products, when compliant, offer a higher guarantee of reliability and safety, thereby contributing to safer operational environments.
Regulatory Adherence
Regulatory bodies mandate that electronic equipment in specific industries meet certain electromagnetic interference (EMI) and electromagnetic compatibility (EMC) standards. MIL-STD-461 compliance ensures that VPT DC-DC converters and EMI filters meet these stringent requirements, thus avoiding legal and regulatory repercussions.
Performance Reliability
MIL-STD-461 compliance guarantees that VPT products can operate effectively in environments with high EMI. This reliability mitigates the risk of equipment failure due to EMI disturbances, ensuring continuous and efficient operations in critical sectors.
Enhanced Product Lifespan
Products that meet MIL-STD-461 standards typically exhibit enhanced durability and longevity. Compliance testing subjects VPT products to rigorous conditions, ensuring they are built to withstand the demanding environments found in industries such as oil and gas.
Competitive Advantage
Companies using MIL-STD-461 compliant VPT products can differentiate themselves in highly competitive markets. Showcasing compliance can strengthen a company’s market position, instilling confidence in stakeholders and customers regarding the safety and reliability of their operations.
By adhering to MIL-STD-461 standards, VPT DC-DC converters and EMI filters not only meet regulatory and safety requirements but also provide a solid foundation for organizations aiming to enhance their operational efficiency and safety.
Take the Next Step Towards Compliance
At Intrinsically Safe Store, we understand the complexities and demands of your hazardous environment operations. Ensuring MIL-STD-461 compliance for VPT DC-DC converters and EMI filters is crucial for optimizing performance and safety. Let us help you achieve seamless compliance with our wide array of certified solutions.
Why Choose Us?
- Expert Guidance: Benefit from our in-depth knowledge on MIL-STD-461 requirements and tailored solutions.
- Comprehensive Products: Access a variety of intrinsically safe and explosion-proof items designed for hazardous environments.
- Trusted Authority: Partner with a global leader in hazardous area solutions.
Get Started Today
Take proactive steps in ensuring your equipment meets MIL-STD-461 standards. Trust Intrinsically Safe Store to be your strategic partner in navigating compliance challenges.
- Consult with an Expert: Schedule a consultation to discuss your specific needs and requirements.
- Explore Our Selection: Visit our online store to browse through our extensive range of MIL-STD-461 compliant products.
- Stay Informed: Subscribe to our newsletter for the latest updates, insights, and industry news.
Make compliance easy. Choose Intrinsically Safe Store—your global authority in hazardous area solutions. Contact us today to begin your journey towards seamless MIL-STD-461 compliance.
Exploring VPT DC-DC Converters
When discussing MIL-STD-461 compliance for VPT DC-DC converters and EMI filters, it’s crucial to understand the specific capabilities and design features of these components. VPT DC-DC converters are renowned for their high reliability and efficiency, making them ideal for operation in harsh and hazardous environments such as those commonly found in the oil and gas industry.
Key Features of VPT DC-DC Converters
- High Efficiency: VPT DC-DC converters are designed to deliver maximum power efficiency, which is critical for systems operating in environments where power conservation is essential.
- Rugged Design: These converters are specifically engineered to withstand extreme temperatures, vibrations, and shocks, ensuring stable performance in the most demanding conditions.
- Comprehensive EMI Filtering: Integrated EMI filters help ensure compliance with MIL-STD-461 requirements by minimizing electromagnetic interference that can disrupt sensitive equipment.
- Wide Input Voltage Range: VPT DC-DC converters support a broad range of input voltages, offering flexibility and adaptability to various power sources found in hazardous areas.
Benefits in Hazardous Environments
For companies operating in hazardous environments, particularly in the oil and gas industry, the reliability and robustness of VPT DC-DC converters provide several benefits:
- Enhanced Safety: Compliance with stringent standards like MIL-STD-461 ensures that the converters do not contribute to hazardous interference, thus maintaining the safety integrity of the entire system.
- Operational Efficiency: The high efficiency and reliability of VPT products minimize downtime and maintenance needs, which is crucial for continuous operations in hazardous environments.
Ensuring Compliance
To achieve MIL-STD-461 compliance, VPT DC-DC converters undergo rigorous testing and validation processes. This involves:
- EMI Testing: Conducted to ensure that the converters do not emit electromagnetic interference that exceeds the levels prescribed by MIL-STD-461.
- Environmental Stress Screening (ESS): To validate performance under varying temperatures, humidity, and mechanical stresses that replicate real-world conditions in hazardous areas.
- Design Verification: Continuous assessment and enhancement of design features to align with the evolving standards and requirements of MIL-STD-461, ensuring long-term compliance and reliability.
The integration of these robust features and thorough testing ensures that VPT DC-DC converters meet and often exceed the stringent requirements of MIL-STD-461, providing peace of mind for companies and individuals operating in hazardous environments.
Testing Procedures for MIL-STD-461 Compliance
Ensuring MIL-STD-461 compliance for VPT DC-DC converters and EMI filters requires a rigorous and systematic approach to testing. Below, we outline the critical steps and procedures involved:
Pre-Test Preparations
Before initiating the testing procedures, certain preparations are necessary to ensure accuracy and repeatability:
- Equipment Calibration: Ensure all testing equipment, such as spectrum analyzers and signal generators, are calibrated according to the manufacturer’s specifications.
- Test Environment Setup: Create a controlled environment free from extraneous radio frequency interference. This may include utilizing shielded enclosures or anechoic chambers.
- DUT (Device Under Test) Configuration: Prepare the VPT DC-DC converters and EMI filters according to the test plan. This includes connecting power sources and loads as per operational requirements.
Conducted Emissions Testing (CE)
Conducted emissions testing measures the unwanted emissions that travel through power cables. Key steps include:
- Measurement Setup: Connect the DUT to the Line Impedance Stabilization Network (LISN) which separates the noise from the power line.
- Frequency Scanning: Perform frequency scanning from 10 kHz to 30 MHz to capture emission levels.
- Data Recording: Document emission levels and ensure they are within the limits specified by MIL-STD-461.
Radiated Emissions Testing (RE)
Radiated emissions testing identifies the electromagnetic field emissions from the DUT that could interfere with other electronic equipment:
- Antenna Selection: Use appropriate antennas to capture radiated emissions, typically ranging from 1 meter to 3 meters.
- Sweeping Frequency Range: Scan the frequency range of 30 MHz to 1 GHz to identify potential interference points.
- Emission Analysis: Analyze and document the results, comparing them against MIL-STD-461 limits.
Conducted Susceptibility Testing (CS)
This testing evaluates how susceptible the DUT is to external electromagnetic interference conducted along power or signal lines:
- Signal Injection: Use signal generators to inject interference signals at designated ports of the DUT.
- Observation and Documentation: Monitor the DUT for any malfunctions or deviations in performance and record all observations.
Radiated Susceptibility Testing (RS)
Radiated susceptibility testing determines the DUT’s ability to withstand electromagnetic fields:
- Field Generation: Employ amplifiers and antennas to generate electromagnetic fields across the DUT.
- Performance Monitoring: Continuously observe the DUT’s operation under varying field strengths and frequencies.
- Result Recording: Note any performance degradation and ensure compliance with MIL-STD-461 standards.
Incorporating these comprehensive testing procedures helps in ensuring that VPT DC-DC converters and EMI filters meet the stringent requirements of MIL-STD-461 compliance.
Common Compliance Challenges with DC-DC Converters
MIL-STD-461 compliance for VPT DC-DC converters and EMI filters ensures the products meet stringent electromagnetic interference (EMI) and electromagnetic compatibility (EMC) standards required for military applications. However, achieving this compliance can present several challenges:
Electromagnetic Interference (EMI)
DC-DC converters are notorious for generating EMI due to their switching nature. These emissions can interfere with the operation of other electronics within the system. Proper filtering and shielding are crucial to mitigate these effects, but achieving the desired EMI reduction while maintaining system performance can be challenging.
Power Integrity
Maintaining power integrity is essential for MIL-STD-461 compliance. Voltage spikes, transients, and noise must be minimized to ensure stable operation. This often requires the use of advanced design techniques and high-quality components, which can increase costs and complexity.
Heat Dissipation
DC-DC converters generate heat during operation. Ensuring effective heat dissipation while preserving the compact size and weight of the converters poses another significant challenge. Overheating can affect performance and reliability, making thermal management an essential aspect of the compliance process.
Testing and Verification
Meeting MIL-STD-461 standards involves rigorous testing and verification processes. Simulating all potential environmental conditions and ensuring consistent performance can be time-consuming and resource-intensive. Inadequate testing can result in non-compliance, leading to costly redesigns and delays.
Component Selection
The selection of appropriate components that meet both electrical and environmental requirements is crucial. Components must not only function correctly under nominal conditions but also withstand harsh environments such as extreme temperatures, humidity, and vibration. Finding the right balance between performance, reliability, and cost can be challenging.
System Integration
Integrating DC-DC converters with other subsystems while maintaining overall compliance requires careful planning and design. Ensuring compatibility and minimizing EMI within the broader system can be a complex task, particularly in densely populated electronics assemblies.
At The Intrinsically Safe Store, we understand these challenges and emphasize the importance of adhering to MIL-STD-461 standards. Our expertise in hazardous area solutions enables us to provide guidance and products that cater to the specific needs of the oil and gas industry, ensuring robust compliance for your critical applications.
Incorporating EMI Filters for Optimal Performance
When it comes to ensuring MIL-STD-461 compliance for VPT DC-DC converters and EMI filters, incorporating the right EMI filters is crucial for optimal performance. EMI filters play a vital role in suppressing electromagnetic interference, which can significantly affect the performance and reliability of electronic systems in hazardous environments such as the oil and gas industry.
The effectiveness of an EMI filter is measured by its ability to attenuate unwanted signals while allowing the desired signals to pass through with minimal distortion. This ensures that VPT DC-DC converters maintain their efficiency and operational integrity in environments where electromagnetic interference is prevalent. By integrating high-quality EMI filters, organizations can safeguard sensitive equipment from potential disruptions and meet the stringent requirements of MIL-STD-461.
EMI filters work by providing a barrier to EMI noise, effectively reducing the risk of interference with other electronic devices and communication systems. In hazardous areas, where equipment downtime can lead to significant financial and safety repercussions, the reliability provided by compliant EMI filters is indispensable.
Technologically advanced EMI filters are designed to handle the specific frequency ranges that are most likely to cause interference in industrial environments. Additionally, these filters are engineered to endure the harsh conditions of hazardous areas, ensuring long-term durability and consistent performance.
For companies operating in the oil and gas industry, ensuring compliance with MIL-STD-461 is not just about regulatory adherence but also about operational excellence. By incorporating EMI filters tailored for use with VPT DC-DC converters, organizations can enjoy improved system reliability, enhanced safety, and uninterrupted performance in the most demanding environments.
Leveraging the solutions offered by trusted providers such as The Intrinsically Safe Store can streamline this process. With a reputation as a global authority in hazardous area solutions, The Intrinsically Safe Store offers a comprehensive range of products designed to meet rigorous MIL-STD-461 testing requirements. This ensures that clients have access to solutions that are not only compliant but also practical for their specific operational needs.
Best Practices for Maintaining MIL-STD-461 Compliance in the Field
Ensuring MIL-STD-461 compliance for VPT DC-DC converters and EMI filters in hazardous environments requires diligent adherence to best practices. These practices are crucial to minimize electromagnetic interference (EMI) and maintain operational integrity.
Regular Testing and Calibration
Conduct regular testing and calibration of your equipment. MIL-STD-461 outlines strict testing requirements that must be met consistently. Regularly scheduled testing sessions will help identify and rectify any deviations from compliance standards early, preventing potential operational disruptions.
Use of Shielded Cables and Connectors
Implement high-quality shielded cables and connectors to mitigate EMI. Shielding is essential in hazardous environments where electromagnetic disturbances can significantly impact the reliability of DC-DC converters and EMI filters. Ensure that all connections are secure and check them periodically for wear or damage.
Environmental Monitoring
Monitor the environmental conditions closely. Temperature, humidity, and other climatic factors can affect the performance and compliance status of electronic components. Utilize sturdy enclosures and consistent environmental controls to protect your equipment from adverse conditions.
Grounding Techniques
Proper grounding techniques are critical in reducing unwanted electromagnetic emissions. Ensure that all grounding points are solid and maintained periodically. Inadequate grounding can lead to significant EMI issues, jeopardizing MIL-STD-461 compliance.
Training and Documentation
Regularly train your maintenance and engineering teams on the latest MIL-STD-461 standards and compliance techniques. Keep detailed records of all compliance-related activities, including testing results, calibrations, and maintenance logs. Documentation serves as proof of compliance and can be invaluable during audits or inspections.
Use of Certified Equipment and Components
Always use certified VPT DC-DC converters and EMI filters. Non-certified parts can compromise compliance efforts and introduce unforeseen risks. Ensure that all components meet the specified MIL-STD-461 requirements and are sourced from reputable suppliers.
Following these best practices will help maintain MIL-STD-461 compliance in the field, ensuring that your operations remain safe, efficient, and consistent with industry standards.
FAQs on Ensuring MIL-STD-461 Compliance for VPT DC-DC Converters and EMI Filters
How does VPT ensure its DC-DC converters comply with MIL-STD-461?
VPT employs a rigorous process to ensure that its DC-DC converters comply with MIL-STD-461 standards. This involves extensive testing in state-of-the-art facilities to simulate real-world conditions. Each product is engineered with advanced filtering and shielding mechanisms designed to mitigate electromagnetic interference (EMI) and ensure that the converters operate reliably in harsh environments.
What tests are included in the MIL-STD-461 standard?
MIL-STD-461 includes a range of tests designed to evaluate electromagnetic compatibility (EMC) across multiple dimensions. These tests typically cover conducted emissions, radiated emissions, conducted susceptibility, and radiated susceptibility. Specific tests include CE101, CE102, CS101, CS114, and RS103, among others. Each test simulates various electromagnetic environments to validate the robustness of the equipment against interference.
What is MIL-STD-461 and why is it important for DC-DC converters and EMI filters?
MIL-STD-461 is a military standard that specifies the requirements for the control of electromagnetic interference characteristics of electronic equipment. Ensuring compliance with this standard is crucial for DC-DC converters and EMI filters used in military and aerospace applications. It guarantees that the equipment can function without causing or falling victim to EMI, thereby ensuring operational reliability and safety in critical mission environments.
How are EMI filters used to achieve compliance with MIL-STD-461?
EMI filters are essential components in achieving MIL-STD-461 compliance. They are designed to suppress conducted and radiated electromagnetic interference both at the input and output of DC-DC converters. By filtering out unwanted signals and noise, EMI filters help maintain the integrity of electronic systems, ensuring that they meet the stringent requirements set by MIL-STD-461.
Can MIL-STD-461 compliance be verified through simulation or is physical testing mandatory?
While simulation tools can provide valuable preliminary insights and help in the design process, physical testing is mandatory for MIL-STD-461 compliance. Physical tests in certified laboratories authenticate that the equipment meets all specified requirements under controlled conditions that closely replicate actual operational environments. Therefore, final compliance validation must always include physical testing.