When it comes to safety in hazardous environments, nothing is more critical than the proper maintenance of intrinsically safe and explosion-proof equipment. This article, brought to you by the Intrinsically Safe Store, will delve into the essential maintenance protocols for such equipment. We invite you to visit our website to explore a wide range of intrinsically safe and explosion-proof devices.
Understanding Intrinsically Safe and Explosion-Proof Equipment
Designers create intrinsically safe and explosion-proof equipment to prevent the ignition of flammable substances in hazardous areas. Engineers design them to limit the energy, both electrical and thermal, to a level below what a specific hazardous atmospheric mixture requires for ignition.
Importance of Regular Maintenance
Regular maintenance of this equipment is crucial to ensure their reliability and safety. It helps in early detection of potential problems, thus preventing costly repairs and downtime. Moreover, it ensures the equipment continues to function as intended, reducing the risk of accidents.
Maintenance Protocols for Intrinsically Safe Equipment
Here are some general maintenance protocols for intrinsically safe equipment:
- Regular Inspection: Regularly inspect the equipment for any signs of damage or wear and tear.
- Testing: Conduct routine testing to ensure the equipment is functioning correctly.
- Cleaning: Keep the equipment clean and free from dust and debris that could potentially ignite.
- Repairs: Any repairs should be carried out by a certified professional to ensure safety standards are maintained.
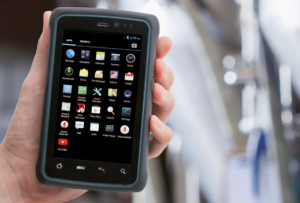
Maintenance Protocols for Explosion-Proof Equipment
Explosion-proof equipment maintenance also involves similar protocols:
- Regular Inspection: Check for any signs of corrosion or damage.
- Sealing: Ensure all seals are intact and replace if necessary.
- Testing: Regularly test the equipment to ensure it is functioning as intended.
- Repairs: Only certified professionals should carry out repairs to maintain safety standards.
Case Study: The Importance of Regular Maintenance
A case study from the oil and gas industry highlights the importance of regular maintenance. A company experienced a near-miss incident due to a failure in its intrinsically safe equipment. The investigation revealed that the equipment had not been maintained as per the recommended schedule. This incident underscores the critical role of regular maintenance in ensuring the safety and reliability of intrinsically safe and explosion-proof equipment.
Prioritizing Maintenance for Safety
Maintenance of intrinsically safe and explosion-proof equipment is not just about compliance with safety regulations. It’s about ensuring the safety of personnel and operations in hazardous environments. Regular inspections, testing, cleaning, and professional repairs are all part of a robust maintenance protocol. Remember, safety should never be compromised.
For more information on intrinsically safe and explosion-proof equipment, visit the Intrinsically Safe Store. Our team of experts is ready to assist you with any queries you may have. Contact us today!