Effective industrial fire safety is an integral component of every industrial warehouse and manufacturing facility. While fires and explosions can stem from a variety of causes and exhibit varying degrees of severity, the ongoing enhancement of industrial fire protection standards remains a priority.
Safety and health experts strive to continually refine best practices for averting fire and explosion incidents. Among these hazards, combustible dust stands as a widely recognized culprit, yet numerous other sources also pose fire risks. Each unique cause necessitates distinct protective measures. Let’s have a look at them.
1. Combustible Dusts
Frequently underestimated yet extremely dangerous, combustible dust poses a significant fire hazard in a wide range of industries such as food manufacturing, woodworking, chemical production, metalworking, pharmaceuticals, and nearly any other sector you can think of.
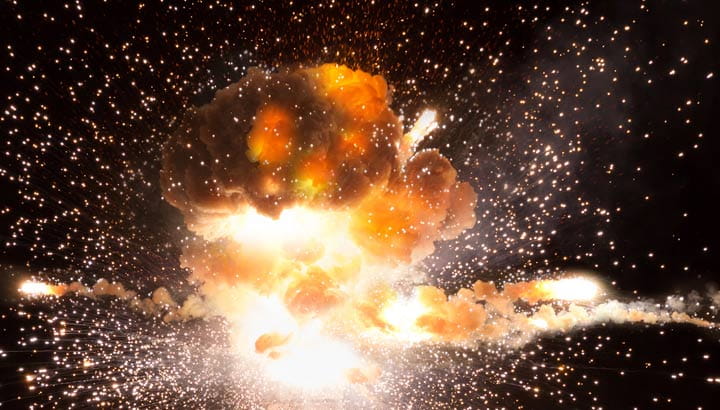
This danger exists because virtually any substance, including food, dyes, chemicals, and metals, can become combustible when reduced to a dust form, even if they aren’t fire hazards in their larger forms.
Containing these explosions is a formidable challenge. In a typical scenario, a flammable material encounters an ignition source, leading to a small fire. These minor fires often go unnoticed but carry significant consequences. Even small fires within industrial facilities result in the loss of products, time, and sometimes physical injuries.
The situation can escalate to something far more devastating. When dust is present in the vicinity, the initial explosion can disperse the dust into the air. Subsequently, this dust cloud itself can catch fire, triggering a secondary explosion that is significantly larger and more severe than the initial one.
If a substantial amount of dust has accumulated, these secondary explosions can potentially lead to the destruction of entire facilities, causing extensive damage and loss of life. Many may recall the Imperial Sugar explosion as a tragic example of the catastrophic consequences of combustible dust buildup.
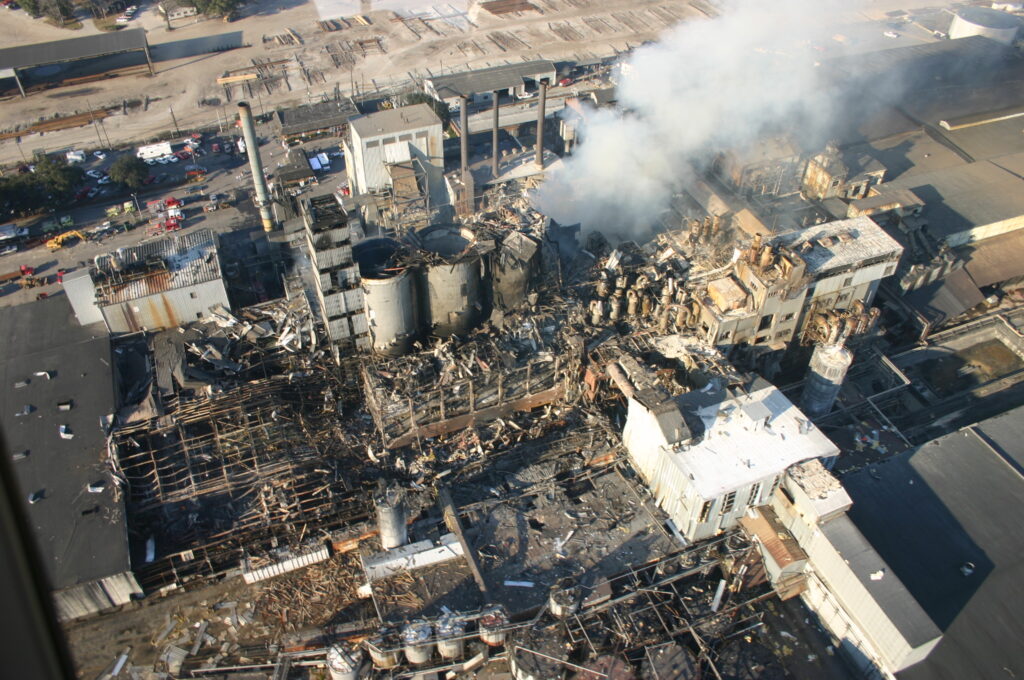
2. Hot Works
Hot works, although often associated with welding and torch cutting, encompass several other activities, such as brazing, burning, heating, and soldering, all of which also pose a fire risk.
This is due to the fact that sparks and molten materials generated during these processes can reach temperatures exceeding 1000⁰F and have the potential to travel more than 35 feet, posing a significant danger.
There have been a few incidents in the past resulting from hot works. Back in 2014, a welder’s torch ignited a fire on a pier in California, leading to over $100 million in damages, including the partial collapse of a warehouse floor.
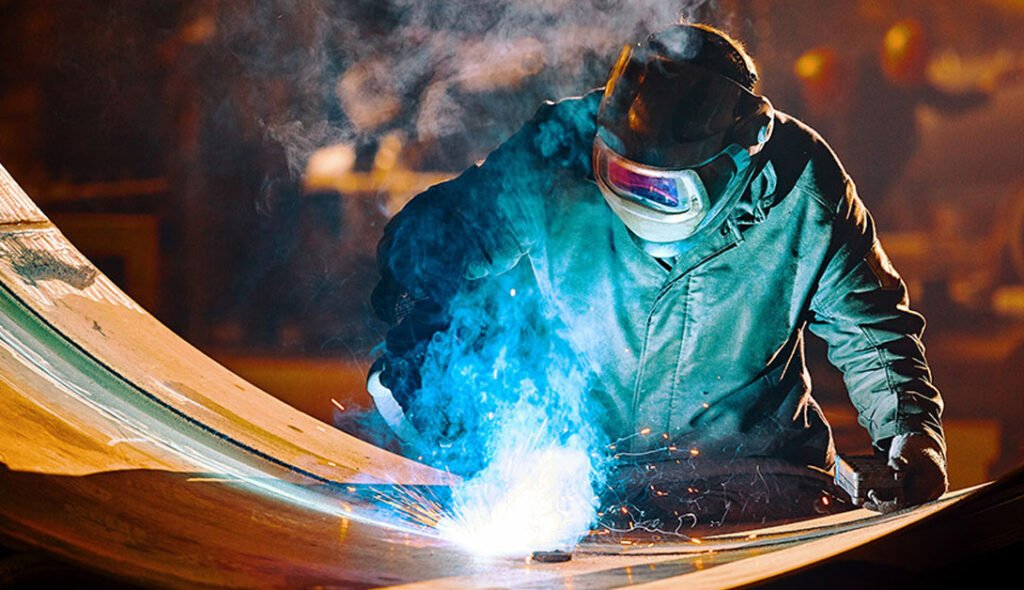
3. Flammable Liquids and Gases.
Highly combustible gases and liquids in chemical plants have a strong tendency to trigger industrial fires and explosions. These substances can lead to fires if they are accidentally discharged or escape into the surroundings, subsequently blending with the air to create a flammable atmosphere within their ignition range.
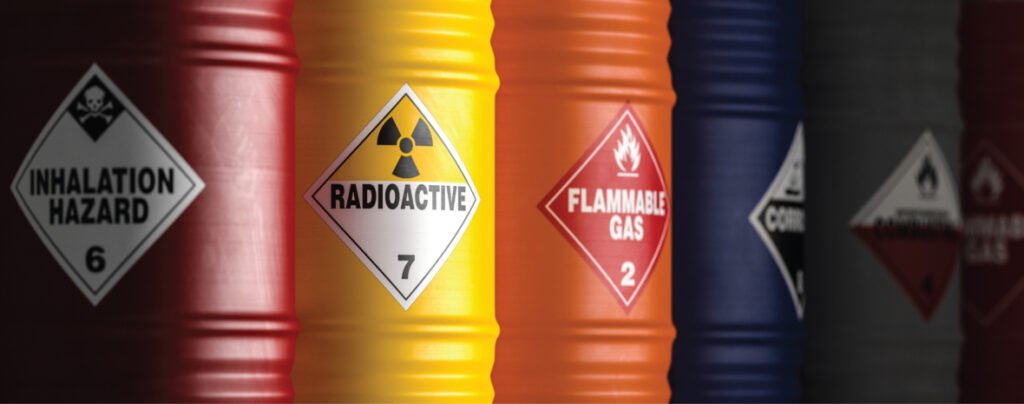
The introduction of an ignition source, such as electrical equipment, welding operations, or sparks, can trigger a chain reaction, leading to the ignition and combustion of the flammable mixture.
Inadequate safety measures, equipment failures, or improper handling can exacerbate the risk, making it essential for chemical plants to rigorously adhere to safety protocols and preventative measures to prevent fires resulting from these volatile substances.
In 2019, a major fire erupted at a Lubrizol chemical plant in Rouen, France, releasing a cloud of toxic smoke and causing widespread concern. The fire involved several flammable chemicals and their interaction led to the blaze. The incident highlighted the potential risks associated with storing and handling flammable materials in chemical facilities.
4. Equipment and Machinery
You have to ensure that you are using intrinsically safe equipment in any hazardous environments. This is due to the high risk that equipment and machinery.
Equipment and machinery in industrial settings can pose a risk of explosions or fires for various reasons. Friction generated by moving parts, if not properly lubricated and maintained, can lead to overheating, potentially igniting nearby flammable materials.
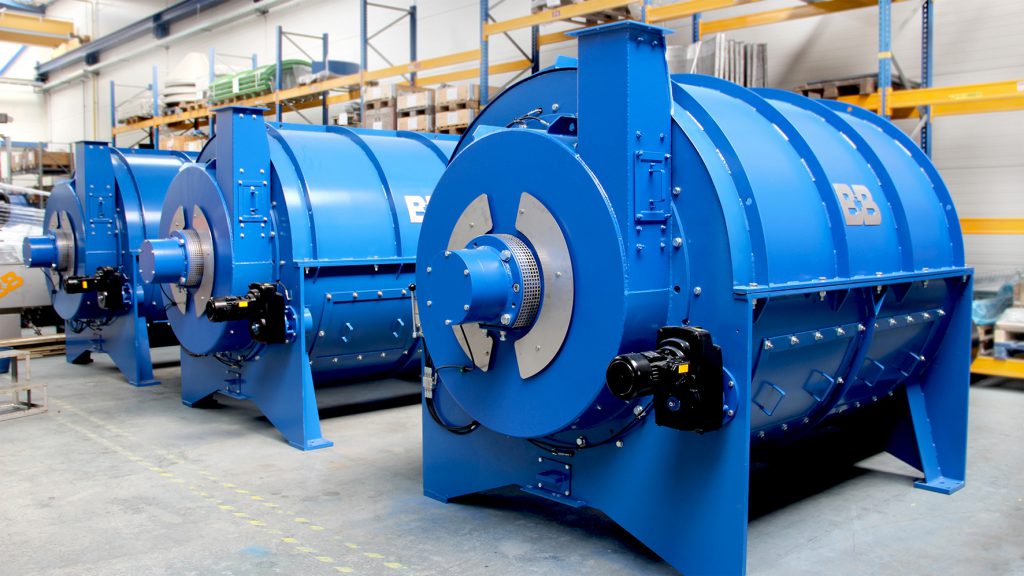
Electrical issues, such as short circuits or damaged wiring, can produce sparks and arcs, serving as ignition sources near combustible materials.
Certain equipment may have hot surfaces as part of their operation, which, if they come into contact with flammable substances or dust accumulations, can cause ignition. Sparks generated by welding and cutting operations can also inadvertently ignite nearby flammable materials if not adequately controlled.
Mechanical failures, such as leaks or ruptures, can release flammable gases or liquids that may be ignited by nearby heat sources or sparks. Inadequate equipment maintenance, including clogged ventilation systems and malfunctioning safety mechanisms, can contribute to hazardous conditions. Additionally, the use of incompatible materials within machinery can result in chemical reactions that generate heat, sparks, or fires.
The primary issue when it comes to fire hazards often lies in heating and hot work equipment, particularly when furnaces are not correctly installed, operated, or maintained.
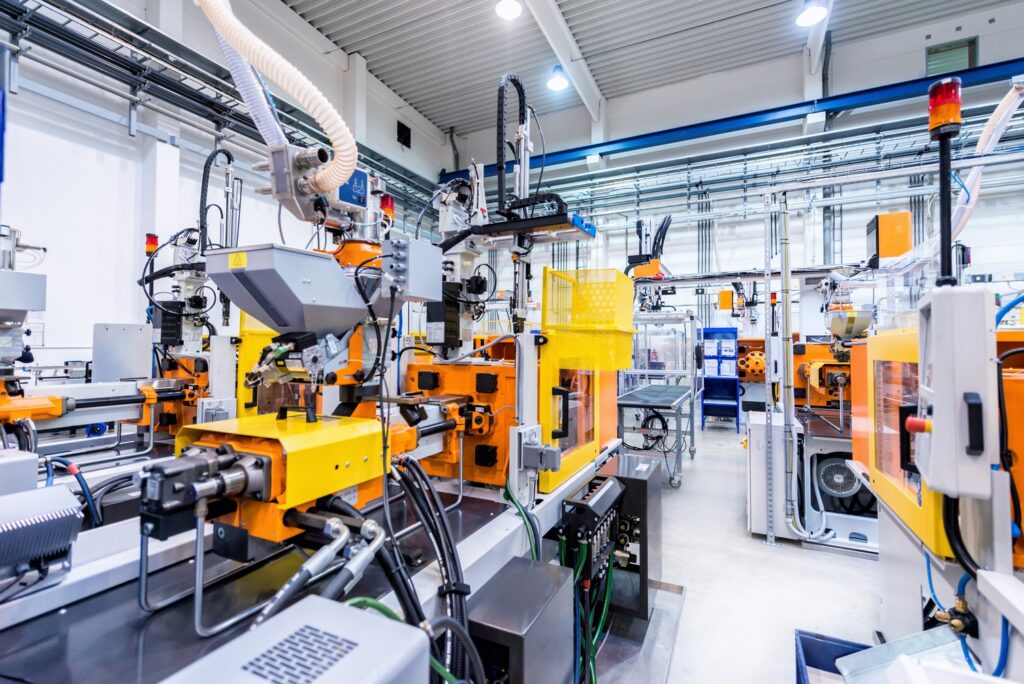
Furthermore, any mechanical machinery can present a fire risk due to the friction generated by moving components. By simply following recommended cleaning and maintenance procedures, which includes proper lubrication, this risk can be almost entirely eliminated.
5. Electrical Hazards
Electrical fire risks encompass exposed or non-compliant wiring, overloaded power outlets, the use of extension cords, circuits carrying excessive loads, and static discharges. These fires can escalate swiftly due to the interplay with several other factors mentioned previously.
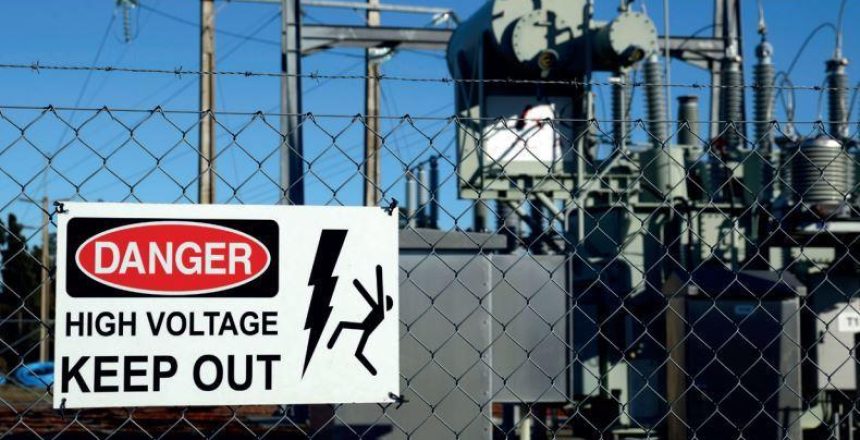
Faulty or deteriorating electrical wiring may generate sparks or heat, which, in the presence of combustible substances, can serve as ignition sources. Exposed or improperly insulated wiring can lead to short circuits and fires. In environments containing flammable gases, liquids, or dust, static electricity generated by electrical equipment can trigger explosions or fires.
Furthermore, electrical equipment, if not appropriately rated for hazardous environments or inadequately maintained, can become ignition sources. Failures of electrical equipment or components, such as transformers or circuit breakers, may result in electrical faults that could lead to fires or explosions.
Inadequate grounding of electrical equipment can increase the risk of electrical arcing and sparks, especially in hazardous environments. Moreover, electrical equipment may come into contact with hot work operations, like welding or cutting, potentially causing sparks and igniting nearby combustible materials.
Safety Mechanisms to Prevent Fires and Explosions.
To prevent fires and explosions and achieve intrinsic safety in industrial settings, a combination of engineering controls and safety mechanisms is essential.
Intrinsic safety involves designing systems to limit energy levels below the ignition threshold of hazardous materials. This can be achieved through methods such as encapsulating electrical components to prevent sparks.
Additionally, using explosion-proof enclosures, implementing gas detectors and alarm systems, conducting hazard assessments, and enforcing strict safety protocols like proper grounding, bonding, and minimizing potential ignition sources drastically reduces risks of fires and explosions.
By systematically implementing these measures, intrinsic safety ensures that the risk of fires and explosions is greatly reduced, protecting both personnel and assets in volatile environments.